Gneuss celebrates 40 years
Cap processing for food-safe HDPE
Gneuss celebrated 40 years of its existence with a huge ceremony at the Imperial Palace in the spa gardens of Bad Oeynhausen, Germany. For 40 years now, the Gneuss family has been working with melt filters and extruders for the plastics industry. One focus is the processing of waste plastics for the packaging industry, especially for contact with food. To mark the festivities, the company presented for the first time a food-safe processing method for plastic caps made of HDPE.
The recycling and decontamination of PET is common practice throughout the industry. In contrast to the most widespread solid-state polymerisation (SSP), where solid plastic pieces like flakes or granulate are degassed and polymerised to the desired IV through cycles of vacuum and temperature lasting many hours, Gneuss works with the Multi Rotation Extrusion System (MRS) that they developed themselves.
The MRS extruder is based on the conventional single-screw extruder, but is equipped with a multiple screw section, for optimum devolatilisation. The polymer melt is delivered into a large single-screw drum. The drum contains several small extruder barrels, parallel to the main screw axis. Installed in these small extruder barrels are the “satellite” screws, which are driven by a ring gear in the main barrel. Depending on the design, this section is under vacuum of 25 mbar or, if required by the application, of 1 mbar.
On this basis, Gneuss has developed a system that manufactures food-safe material from defined plastic waste streams. This includes PS, PP and PET for bottle-to-bottle applications. Maxing at 5 minutes, the dwell time in the MRS extruder is very short, and quality fluctuations in the waste streams can be corrected immediately. Depending on the specific system configuration and the feed stream, this results in consistent FDA quality, even if non-food packaging is present in the waste stream.
One North American customer alone has six bottle-to-bottle systems installed.
Now, during the inhouse event, Gneuss showcased a new concept in which a twin-screw extruder is coupled in front of the MRS extruder. This separates the degassing process in the MRS extruder from plastification, a benefit for certain input materials such as high-viscous materials like HDPE. Typical applications include the closed-loop recycling of HDPE bottle caps, HDPE milk bottles or LDPE waste and mixtures of different polymers.
Gneuss has various international food approvals granted and pending that confirm the high cleaning efficiency (super-clean) of the MRS technology. In the example of the defined waste stream of drink bottle caps, a food-safe HDPE is created from which new caps for drinks can be made.
Interview with Daniel Gneuss, President of Gneuss USA
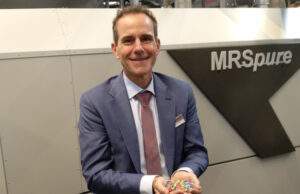
PETplanet: Mr Gneuss, we heard a great deal about bottle flakes to fibres at your event. Is this a future market, especially since the PET bottle industry is desperately seeking flakes?
Daniel Gneuss: I think this market is important, especially in America, where polyester carpets mean a huge demand for fibres. But I also think that it is more and more difficult for fibre manufacturers to get bottle flakes, and in the future, most bottle flakes will go back into bottles.
PETplanet: Hopefully using your systems?
Daniel Gneuss: We’ve shown that our Multi Rotation Extrusion System (MRS) produces a brilliantly consistent quality for bottle-to-bottle recycling. But I worry that in the future conventional stand-alone bottle-to-bottle facilities will have a hard time competing with large scale approaches from resin producers. Blending post-consumer bottle flakes back into a melt stream and creating new resin from 25 or 30% rPET. At today’s recycling rate this is a sensible approach which can also easily scaled up and down depending on the availability of PCR. Gneuss has delivered multiple lines for such production lines and we see growing interest in this technology.
PETplanet: Today, you presented cap recycling.
Daniel Gneuss: Yes, I think there’s still plenty for recyclers to work on in the future besides PET bottle-to-bottle recycling. The cap weighs around 5 to 10% of the bottle weight, and today this doesn’t feed back into the closed loop. With the system presented here, we’re creating granulate for new drinks caps.
PETplanet: Thank you so much Mr Gneuss.