New challenges in sport caps making
Attention to the environment, complex closures and ergonomics: the caps manufacturers are more and more raising the bar in their new developments. In this scenario, the Italian company Maca Engineering offers a complete range of automatic machines and systems for the production and assembly of aluminium and plastic caps and closures.
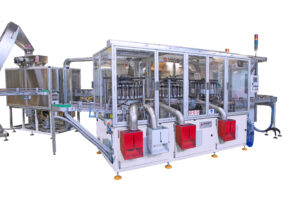
machine with an output of up to 36,000 pieces per hour
Maca Engineering has experience in tailor-made solutions to realise complex closures through fast, reliable and fully automated machines for over 30 years. Maca supports its customers with feasibility studies and design proposals in order to find the best possible solution in the initial phase of research or the market launch of a new product. Around 80% of key components and structural assemblies (including machine units, dies, etc.) are produced in-house and countermarked with an identification number. One of Maca’s main production areas is the assembling lines and slitting/folding machines for plastic caps and closures: not only pre-threaded flat plastic caps, but also pre-threaded sport plastic caps, complex closures for alcoholic drinks or pre-threaded agrochemical caps.
One example, is a line for folding, assembling “TE ring” and spout and slitting for the production of sports caps. In particular, it is a flexible continuous rotary assembly machine model ARV and a continuous rotary slitting machine model ITVE. Structurally the ARV machine consists of three flywheels with 24 punches each capable of assembling up to three components with an output of up to 36,000 pph. The first flywheel is dedicated to folding body flap, the second flywheel for inserting ring and the third flywheel for inserting spout. For greater efficiency the ARV model provides some features such as ejection of defective pieces (for example, not assembled pieces), that occur without the machine stopping its process. Rejecting defective parts stations are located after each flywheel and consist of a sensor. If it detects an error (non-compliant piece for colour or incorrect assembly), it discards the piece, and this can happen at any stage of assembly.
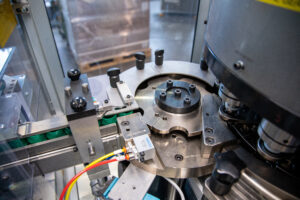
The second model, ITVE, is a machine that cuts the bottom part of the cap. Thanks to the exit conveyor belt with the integration of a vision system, it checks for possible deformation of caps and ensures the correct presence of the components inside caps. Finally, it provides a straight end-line conveyor for cardboard boxes (four boxes in accumulation, one box in the filling position, and three boxes in discharge). Maca has the ability to assemble up to four components (body, ring, spout and valve) using the 3-Flywheel ARV and an additional ARV for inserting the valve. The machines can be supplied at low, medium and high speed, based on individual requirements.
Abou Maca Engineering: Since a few years Maca Engineering became part of the Arol Group, which includes: Arol Closure Systems, the global point of reference in the design, manufacture and distribution of capping machines & capping turrets, caps feeding systems, caps orienting systems and caps sorters; Unimac-Gherri the specialist in filling and capping of glass, metal and plastic containers with twist-off and pre-threaded caps for dense, semi dense and pasty products and Tirelli, which develops and produce filling, capping and labelling systems mainly for home and personal care industry.