The material of choice for sustainable packaging
based on an article by Dr Frank Welle, The Facts about PET
PET (Polyethylene Terephthalate) was first developed for use in synthetic fibres by British Calico Printers in 1941.* The patent rights were then sold to Dupont and ICI who in turn sold regional rights to many other companies. Although originally produced for fibres, PET began to be used for packaging films in the mid 1960s and then, in the early 1970s, the technique for blowing bi-axially oriented bottles was commercially developed.
Bottle now represent the most significant use of PET moulding resins. Making a PET bottle starts from the raw material: ethylene and paraxylene. These two substances’ derivatives (ethylene glycol and terephthalic acid) are made to react in order to obtain the PET resin. The resin, in the shape of small cylinders called pellets, is melted and injected into a mould to make a preform. The preform – a sort of test tube, shorter than the final bottle but with thicker walls – is then blow-moulded. During the blow-moulding phase, high-pressure air is blown into the preform allowing it to take the exact shape of the mould it is set into. The final product is, thanks to the molecular structure of the material, a transparent, unbreakable, resealable and lightweight bottle.
The strength of the material
It is the strength of the material that contributes to the success of PET. Indeed, carbonated soft drinks can generate pressure inside the bottle reaching up to 6 bar. Such high pressure however, thanks to the alignment of macromolecules (crystallisation) occurring both during the resin spinning process and the blow-moulding process, is not capable of deforming the bottle nor can it make the bottle explode. Another advantage of the material lies in its physical properties that allow for great freedom in design. Throughout the years, the PET industry has increasingly taken on environmental concerns, significantly decreasing the quantity of raw material needed for the manufacture of bottles. Nowadays, a 1.5 l PET container is manufactured with < 30 g of raw material. Another striking feature of PET on the environmental side is that it is fully recyclable. In 1977, the first PET bottle was recycled and turned into a bottle base cup. Soon however, the fibre industry discovered the “new” material source and started using it for making textiles, carpets and non-wovens. Today, even though the “bottle to bottle” recycling process is growing, the fibre market is still the major outlet for recovered PET.
Lightweighting PET
PET bottles are very strong, colourless and lightweight. PET is transparent and it allows the content of the container to remain visible. The strength and lightweight of PET is very important for beverage packaging since it makes the bottles safe for on-the-go or sports use. Over the years, the weight of PET bottles has been reduced and today a 1.5 l bottle can weigh as little as 20 to 30 g. This process of light weighting represents a true benefit with regard to the environmental performance a bottle will have during its lifetime: production, transport to the consumer and end of life cycle. With its excellent material properties, PET is widely used today as a packaging material for liquids such as carbonated beverages and is one of the most suitable materials for the packaging of natural mineral and spring water. PET is used in the packaging sector in the form of films, trays or bottles, its principle use being in bottles.
The interaction of PET with food and water
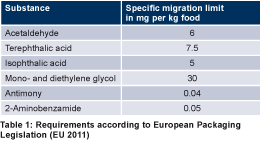
No packaging material is fully inert and so there will always be some kind of interaction with the beverage or foodstuff it contains. In the case of food, mild oxidation may occur due to oxygen permeation. Likewise, carbon dioxide from carbonated beverages can permeate through the packaging material. In certain instances, there may also be a small degree of migration of components from the plastic packaging into the content.
For consumer health protection, all such interaction must be reduced to a minimum. As with all other material in contact with food, PET packaging does comply with all European and national legal requirements. Such requirements include an assessment of the initial raw materials employed (i.e., monomers and additives) and the compliance with any restrictions that are established, such as migration limits. The requirements for the migration of monomers and additives according to the European Packaging Legislation is given in Table 1.
Acetaldehyde
Acetaldehyde is a by-product of the PET manufacturing process. It is produced when PET is heated to a high temperature to produce bottles. Many beverages and foodstuffs contain natural acetaldehyde. The trace quantities of acetaldehyde that may migrate from PET into bottled water are totally harmless, although they may cause the water to have a slightly fruity offtaste. When the concentration exceeds 0.02 mg of acetaldehyde per litre, the consumer may be able to taste it. Based on consumers’ acceptance and local regulation, this is something that should be avoided in some countries whereas it is well accepted in others. PET bottle manufacturers have worked closely with the bottled water companies to optimise the PET bottle production process with a view to minimising levels of acetaldehyde migration. Also acetaldehyde reducing additives are applied in the preform manufacturing process.
Acetaldehyde reducing additives
Traces of acetaldehyde can migrate from the PET bottle wall into natural mineral water. The main goal in preform and bottle manufacturing is to reduce the acetaldehyde concentration in PET. From migration theory, the bottle wall concentration of acetaldehyde is directly proportional to the migration under the same storage conditions. This means that the reduction by a factor of two results in half of the migrated amount of acetaldehyde into bottled water.
2-Aminobenzamide, also known as anthranilamide, is the most popular acetaldehyde reduction additive and called an acetaldehyde scavenger used in PET preform manufacturing. This additive reacts chemically with acetaldehyde to form a non-odorous and higher molecular weight substance. As any other additive, 2-aminobenzamide must be approved for the application in PET bottles and the specific migration limit of 2-aminobenzamide of 0.05 mg/kg food (Table 1) has to be controlled in routine tests by the mineral water filling company.
Monomers (ethylene glycol and terephthalic acid)
In general terms, the migration of monomers from plastics can never be totally prevented. PET, however, is highly inert compared to other plastics. Thus, only extremely small quantities of monomers may migrate into bottled water. For example, a study has shown that the level of migration of the monomers ethylene glycol and terephthalic acid from PET bottles is far below statutory limits. Nonetheless, water bottling companies constantly monitor levels of monomer migration from PET bottles.
Antimony
Antimony trioxide is the major catalyst used to polymerise PET. In principle, the catalyst will remain in the PET after polymerisation. Typically, concentrations of antimony in PET bottles are below of 300 mg/kg PET. Alternative catalysts for the polymerisation of PET have also been developed, mostly based on titanium, aluminium or germanium. However, to date the alternatives developed have not succeeded in making a major commercial breakthrough and antimony trioxide remains by far the dominant catalyst employed by resin suppliers. As with all the substances employed in the manufacture of PET, antimony is subject to strict statutory regulations in Europe. The maximum permitted level of antimony migration from a PET bottle into the finished product is 0.04 mg/l (Table 1). Under normal storage conditions, the level of antimony migration from PET bottles is extremely low. The limit value for antimony migration from PET packaging may not be exceeded during the shelf life of the beverage, even when bottles are stored in warm climates for many months. The limit value for antimony in water is considerably lower than the limit value for migration from PET packaging. In Europe, for example, a maximum of 0.005 mg of antimony may be present in one litre of natural mineral, spring or drinking water at the time of packaging. Even if, from a legal point of view, the migration limit of 0.04 mg/l is valid for bottled .
Bio-PET
Traditionally, the monomers of PET are manufactured from fossil-based resources. However, a synthetic route for ethylene glycol, one of the two monomers, was developed from biomass as early as in the late 1980’s. Sugar-cane is transformed to bio-ethanol. In the second step, bio-ethanol is oxidised to the monomer ethylene glycol, which is subsequently used for the polymerisation of PET. A mass fraction of about 30% by weight is realised when using bio-ethylene glycol as monomer for PET. The second monomer of PET, terephthalic acid, is not commercially available using bio-based resources. However, synthetic routes from biomass to terephthalic acid are available in laboratory/pilot scale. From a chemical point of view, bio-PET is indistinguishable from fossil-based PET. Therefore, the same manufacturing facilities for PET pellets, preforms and bottles can be used. Also, bio-PET is fully recyclable along with fossil-based PET. Such bio-based equivalents to fossilbased polymer are called “drop-in” biopolymers.
* Neumann, E H. Thermoplastic polyesters in Encyclopaedia of Packaging Technology, ed Bakker M. John Wiley, New York 1986.
https://www.petcore-europe.org/images/news/pdf/factsheet_the_facts_about_pet_dr_frank_welle_2018.pdf