Continuous developments
Sacmi Hall B5 – Booth 101, 302-304
Sacmi will be introducing its Smart lines for cap and preform production at Drinktec. The focus will be on the new digital architecture of the machines and processes and the development of new standards that are already compliant with the coming regulations.
Sacmi bases its digitalisation strategy on a set of key principles, which it offers as a set of three specific packages and services. Smart Pack integrates advanced sensor technology and on-board machine checks into Sacmi cap and PET preform lines. Developed for “real time reaction”, Smart Pack is intended to increase plant availability and component service life of its components, while simplifying the operator’s work. Sacmi says that the system predicts drifts and detects errors, such as the wrong resin, that could cause damages at both economical and reputational level.
The H.E.R.E. MES plant supervisor, which is designed specifically for the needs of cap manufacturers, includes advanced monitoring, order scheduling, and tracking functions. The third package is the new Smart Care service, which collects and manages data from customers’ machines and plants, in the cloud. This enables remote monitoring of plants’ health status and makes use of proactive problem-solving services.
Tethered caps
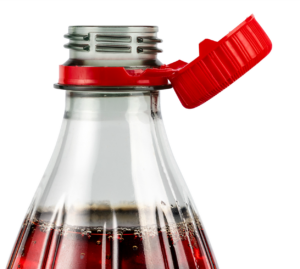
Sacmi has already developed a range of products intended to enable its customers to transition to tethered caps, as mandated by EU Directive 2019/904. Its offers are in two strands: a flexible process for post-production processing with a slitting-folding machine; and a complete range of tethered caps, which is already available and can be adapted to most commercially-available bottle types. Sacmi will be showcasing its new caps for 26 mm finish for CSD and a range of lightweight products that are compatible with the new tethered standard.
Downstream of the cap production process, Sacmi also offers full integration with tamper evidence band slitting and folding machines (SFM). It can be integrated with its new PFMC (pull force machine), which performs checks and tests on the band during production, and with the CVS-cut system, which checks the quality of the tamper evidence band cut.
PCR (post consumer resins) and recycling
Sacmi’s standard range of preform presses have had, for several years, the option of processing up to 100% rPET, and up to 50% recycled PET in the form of flakes.The company will be presenting a solution that allows the percentage of rPET flakes to be increased up to 70-75%. This enhancement redesigns the entire process for optimal handling of flake and granule mixtures, with no need for two separate processing hoppers. Sacmi says that this development offers increased efficiency and ease of use, and will facilitate the switch to a complete food-grade PET recycling supply chain.
The company is preparing to further expand its recycling approach for food grade use products to include the entire cap-preform system. It is also continuing research and prototyping of new biocompatible polymers, such as cellulose-based fibres and blends.
CM-Flow extruder & computer vision
The advanced features and controls on Sacmi’s compression machines are designed to increase availability and efficiency, thus reducing waste. The company says that the compression process, which operates at lower temperatures than the injection process, helps progress in the drive to cut waste.
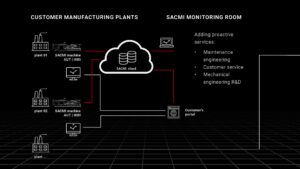
The new CM-Flow extruder is available on all new CCMs but can also be installed on several existing machines. This feature saves energy by improving the quality of the extrusion process and reduces the risk of black spots of up to 50%, according to monitoring and analysis carried out with customers who are already using the solution. This is an additional option and does not replace the ‘Smart Pack’ service, which is available on all the new-generation presses. In the case of ‘vision’ systems, Sacmi offers several families of solutions based on artificial intelligence (AI) algorithms for performing quality controls on the cap, T.E. band cut and PET preform. These systems provide a basis for developing quality control towards proactive process monitoring through real-time availability of relevant data and information, which can be used to detect production deviations in advance and to predict the necessary corrections.