"TRADE SHOW PREVIEW 78 PETplanet Insider Vol. 17 No. 10/16 petpla.net Beer and milk in the world’s biggest PET containers 50l in PET Cypet Technologies Ltd of Nicosia, Cyprus, manufacturer of single-stage PET processing machines using its own, patented technology, will show 50l PET containers, which are claimed to be the world’s biggest. Other highlights on their booth are a patent-pending handle concept as well as their range of preform moulding systems. Cypet Technologies Hall 14 Booth C58 Preform moulding system The 50l beer keg is in production in Australia. 50l PET containers The 50l beer keg is claimed to be capable of withstanding over 9bar burst pressure, and is now in production in Australia on a Cypet K 53 machine. To complement this 50l keg size, the machine also produces 30l beer kegs as well as 35l conicalshaped PET fermenters for home brewing. Another 50l container is used for transporting milk, with a 180mm neck diameter and with unique moulded-in handles for easy carrying - now in production in Kenya on a Cypet K 38 machine. To complement this 50l milk jug size, the machine also produces a 20l version with the same neck and handles. Cypet claims that its largest K 53 machine model is capable of producing up to 100l PET containers. Such containers can replace HDPE drums, especially for single-trip applications, resulting in weight reduction, with the corresponding substantial savings in raw material cost. One step handle concept A handle concept for PET bottles currently under development will also be shown at the Cypet booth. This is claimed to be a revolutionary handle concept for PET bottles, with the same functionality and convenience of HDPE bottle handles. This is a patent pending, incorporated PET handle, which is moulded into the preform, resulting The patent pending incorporated PET handle is moulded into the preform. With the new handle concept, the bottle is produced complete with handle in one step on a single-stage machine. 50l milk container with a 180mm neck in PET bottles that can successfully challenge HDPE bottles with handles, for sizes ranging from 1-30l. With this handle concept, the bottle is produced complete with handle in one step on a Cypet single-stage machine, eliminating the need to separately mould handles from a different polymer and also the need for a second operation of feeding the handles into the blow moulds during blowing or clipping the handles onto the blown bottles. Recycling is also said to be easier since bottle and handle are made from the same PET material. Preform moulding systems The company will also show its new range of preform moulding systems, which incorporate an innovative post cooling system which is said to make it ideal for thick preforms for large bottle sizes (5-30l). Cypet’s preform moulding system is based on an injection mould with two sets of cores and two post cooling stations with two sets of cooling tubes each. This provides intensive preform cooling for two cycles on the injection cores, for one cycle in the injection cavities and for four cycles in the post-cooling tubes. Cypet preform moulding systems are available with 2, 4, 6 or 8 cavities, for preforms up to 11mm thick for up to 30l bottles. www.cypet.eu","@ID":80}, "INSPECTION 27 PETplanet Insider Vol. 17 No. 10/16 petpla.net Measuring thickness Despite robust practices that support consistent bottle production, like the mandate never to mix different batches of preforms, Chimetto notes that blowmoulder performance is susceptible to variation. Environmental conditions such as temperature and humidity are major factors that cannot always be controlled. For example, “big changes can occur around the blowing machine at night,” he says. “If other machines nearby are shut down, the temperature can drop. There are also natural temperature fluctuations with the weather. These temperature variations affect the blowing operation.” More than a decade ago, Chimetto looked to Agr for help in minimising the impact of these variations on the blowing process. As the relationship developed, he became an early adopter of a “take-no-chances, measure everything” approach to bottle-making. It started in 2003 with the installation of Agr’s Profiler on-line thickness measurement system deployed inside the blowmoulder. The earliest Profiler systems used sensors to measure the material thickness in four different zones along the bottle sidewall, providing feedback that allows the blowmoulder operator to better manage the blowing process. “This was a real benefit,” states Chimetto. “As soon as the operator made an adjustment, he could really see the effect. This eliminated a lot of guessing and especially the potential to make an adjustment in the wrong direction.” Having confirmed the valuable contribution the Profiler made to its quality program, Sanpellegrino installed the device on several high-speed blowing lines (then as fast as 30,000bph) where material distribution was critical for bottle performance. The targeted sites included the Scarperia, Tuscany, plant producing the Acqua Panna brand; Cepina Valdisotto, in the Alps, for Levissima production; and San Giorgio in Bosco, in Padova (Padua), for the Nestlé Vera brand. Profiler’s non-contact, nondestructive measurement enhanced Sanpellegrino’s ability to achieve uniform production, meeting the same standards for shape, dimension, and clarity in every bottle. It also provided real-time process information, allowing operators to counteract the variable conditions the different blowing lines were subject to, saving production time and reducing scrap. “Without the Profiler, the operator had to adjust, observe, test, and verify, and then re-adjust the process until it was right,” Chimetto explains. “With this new tool, the operator had immediate feedback to see whether the changes made were proper. Essentially, it eliminated the need to section-weight to manage the process.” Providing control Fast forward to 2009, a time when blowmoulder speeds were increasing, lightweighting initiatives began to proliferate, and Agr was preparing to roll out its next-generation management tool, the Process Pilot automated blowmoulder control system. Reflecting significant technology advances, the Process Pilot provides not only more comprehensive measurement of the entire bottle sidewall, but also control of the blowmoulder to continuously maintain the proper material distribution. Two key Process Pilot innovations - miniaturised sensors and sophisticated algorithms that determine optimal blowmoulder parameter adjustments - add a new level of precision to bottle-blowing. Outfitted with up to 32 sensors spaced at 12.5mm intervals, the system reads the actual bottle thickness measurements, compares the data with the specified parameters, monitors the comprehensive measurements, and, as changes are identified, automatically adjusts the blowmoulder to continue optimum production. Chimetto immediately recognised the benefit of being able to monitor and manage material distribution in real time on the production line, with Pilot serving as a virtual operator. “This really was the technology that made it possible to close the loop in blowmoulder control,” he emphasises. “I saw the potential to actually monitor the details of material distribution and take it one step further to automatically control the blowmoulder to make the necessary changes to manage the process.” Nestlé Waters Italy agreed to field-test the Process Pilot technology, and its Levissima plant became the first bottling operation in Europe to deploy the closed loop system. Test results showed that the system offered a number of benefits, including the ability to manage the blowmoulder to virtually eliminate the effect of process and environmental variables that impact bottle material distribution, thus reducing scrap and improving production consistency. At production speeds approaching 40,000bph, the processing window for lighter bottles narrows significantly.","@ID":29}, "BOTTLE MAKING 24 PETplanet Insider Vol. 17 No. 10/16 petpla.net Designing a glass-like bottle for spring water From glass to PET Sedona Bottling traditionally marketed their artesian spring water in glass bottles but were keen to create a family of lightweight PET bottles, proposed to meet demand from the event, hotel and leisure sector. Working with Amcor Rigid Plastics, the intention was to create a PET bottle that still looked like glass. Purely Sedona originates from a registered and protected artesian spring in the Oak Creek Canyon in Sedona, Arizona, USA. Oak Creek Canyon is a sacred river gorge that runs along the Mogollon Rim in northern Arizona. The water that emerges from the canyon is naturally purified, yet retains minerals and electrolytes, according to the bottling company. The water’s natural filtration process eliminates contaminants while retaining key minerals that deliver better flavour and nutritional benefits. Oak Creek Canyon water also has a natural pH of 8. The premium spring water has already been offered in glass but the company intended to undertake a re-branding of an existing stock PET bottle. The ScorCreative design team, the award-winning structural design studio co-located at Amcor Rigid Plastics, worked closely with Sedona Bottling to meet its branding requirements while also satisfying engineering demands surrounding the base, shoulder, and also stacking issues. ScorCreative focused on a medicinal style design to showcase the purity and healing properties that are said to be derived from the spring water, according to Rick Rangler, senior design lead for ScorCreative at Amcor. The novel retro design is tall and sleek and similar to a Boston round style bottle. The glass-like container incorporates a 28mm black closure to convey the look of an old-time pharmacy tonic bottle. The product development cycle was compressed with both parties opting for an intense one-day design session at Amcor headquarters. Amcor’s dedicated team of industrial designers and packaging engineers worked closely with the customer, presenting initial concepts and then providing rapid-fire response for multiple design iterations that culminated in a final design at day’s end. The PET bottles are available in 500ml and 1l proprietary bottles. Additional package sizes including 12oz and 1.5l PET bottles are also being examined. www.purelysedona.com www.amcor.com","@ID":26}, "PETpatents www.verpackungspatente.de 92 PETplanet Insider Vol. 17 No. 10/16 petpla.net Internally coated bottle Europ. Patent No. EP 2955120 A1 Applicant: Toyo Seikan Group Holdings Ltd., Tokyo (JP) Application date: 7/2/2014 A plastic bottle designed as a tube to be placed upright which delivers its content by compression is equipped with a special coating on the inside which prevents the product from sticking. The dispensing system and the remaining quantities are currently being improved. Floor with a snapping effect Europ. Patent No. EP 2957522 A1 Applicant: Sidel Participations, Octeville-sur-Mer (FR) Application date: 17/6/2014 The bottom of a PET bottle is shaped in a way that can be collapsed between the two end positions. The bottle is hot filled, closed, cooled and at the end the floor automatically moves from a lower end position to a higher end position. This gives the bottle an excess pressure which makes it more stable. Improved shelf life Intern. Patent No. WO 2016 / 019321 A1 Applicant: The Coca Cola Company, Atlanta and Bericap SC LLC., Cowpens (both US) Application date: 31/7/2015 The application describes a PET bottle with reduced weight and a fitted screw cap. The upper part and the cap are shaped specifically to ensure longer shelf life / optimal product quality. The screw cap is grip-friendly. In-mould bottle label Intern. Patent No. WO 2016 / 017082 A1 Applicant: Yoshino Kogyosho Co. Ltd., Tokyo (JP) Application date: 9/7/2015 Described are the conception and the manufacturing procedure of a plastic bottle with a label applied in the “In-Mould” shape. The bottle is shaped by water pressure and the label is stuck and fixed onto the bottle. Plastic bottle Europ. Patent No. EP 2962947 A1 Applicant: Yoshino Kogyosho Co. Ltd., Tokyo (JP) Application date: 17/12/2013 The international application describes the shaping of the floor of a bottle conceived for hot filling. The bottle is sufficiently stable, but flexible enough to balance out the negative pressure created while cooling down. Floor for lightweight bottles Intern. Patent No. WO 2016 / 019318 A1 Applicant: Coca-Cola Company, Atlanta (US) Application date: 31/7/2015 Many different bottle floor shapes are described for carbonated soft drinks. The material composition / change during manufacturing are being inspected and evaluated.","@ID":94}, "CAPPING / CLOSURES 46 PETplanet Insider Vol. 17 No. 10/16 petpla.net 4.8 Test Procedures Supply of closures for beverage containers involves a myriad of testing procedures to ensure that the caps perform satisfactorily in use and are safe for consumers. To become a supplier to a beverage bottler involves completing a thorough certification procedure. Once completed, there will be recertifications on a yearly basis as well as production audits. When a significant change in an existing design has been made, another extensive certification process may be required. Out of the large number of tests, we have chosen the most common ones for 28mm closures for carbonated beverages to give readers a good overview of what is involved. The values mentioned here might differ depending on the beverage company. 4.8.1 Proper ApplicationTest Filled and capped bottles are cut off underneath the support ring and placed in a pressure chamber. They are then pressurized to 6.9bar (100psi) and held there for 1 minute. No cap can leak at this position. Next the pressure is increased to 12bar (175psi) and held there for 1 minute. No cap can release any pressure at this point. After removal from the chamber, caps are closely inspected for any damage. 4.8.2 Top-load Vent Test Capped and filled bottles are conditioned for 48 hours in an environmental chamber at 40°C (104°F). A top load of 45.5kg (100lb) is applied. No headspace gas may vent during the loading of the bottle. 4.8.3 Cold Removal Torque Test Capped bottles are stored in an environmental chamber at 2-4°C (3540°F). Caps are examined after 24 hours and 1, 3, and 6 weeks. They are slowly unscrewed. When the maximum torque is reached, the value is noted as the seal torque. When the tamper band breaks, the value is noted as the band torque. Acceptable values for maximum torques are 19.6kg cm (17in lb). 4.8.4 Ambient Removal Torque Test Capped bottles are stored at 20-24°C (68-75°F). They are examined for seal and band torque as described in the previous section in intervals of 24 hours and 1, 3, 6, 9, and 12 weeks. The same values obtained earlier are acceptable. 4.8.5 CycleTest at Elevated Temperature Capped bottles are placed in the controlled circulating air oven that is preheated to 42°C (108°F). The temperature is then increased to 60°C (140°F) and held for 6 hours. Then it is reduced to 32°C (90°F) and held for 18 hours. This temperature cycle is repeated three times. All caps must stay on the bottles, but leakers and cocked caps are allowed. 4.8.6 Vent/Flow Performance Test Filled and capped bottles are cut off underneath the support ring and placed in a pressure chamber. The current position of the cap on the bottle is marked, and a pressure of 5.5bar (80psi) is applied. Now the technician slowly opens the closure and notes the so-called vent angle when the closure starts emitting gas. The technician then notes flow rates at various angles until the closure comes off. There is no pass/grade in this test but these values are important to ensure that the closure will vent all gas contained in the bottle before it comes off. 4.8.7 Strip Torque Test Bottles are conditioned at 38°C (100°F) for 1 hour. The warm bottle is then clamped and the cap rotated in clockwise direction until it jumps off the threads. The torque value is then recorded as the strip torque. A minimum strip torque of 34.6kg cm (30in lb) is required to pass. This test ensures that the closure will not fail during capping. product development caps & closures design high cavitation moulds multi-component moulds closure production systems after sales service competent – professional – inspiring Hoechster Strasse 8 | 6850 Dornbirn | Austria | www.z-moulds.com K-Show 2016 October 19th-26th meet us at the Eisbär booth in Hall10 / H46 Moulds at the K-Show 28mm 1881 FlipTop Fontana @KraussMaffei in H15 / C24 Cap 29/25mm 3-start water @Blue Air Systems in H10 / H60","@ID":48}, "BOTTLING / FILLING 36 PETplanet Insider Vol. 17 No. 10/16 petpla.net SPONSORS The China Road Show F.l.t.r.: Michael Chen, Managing Director of Bericap China and Alexander Büchler, PETplanet Insider in front of the Editourmobil 40 filling factories in China By Kay Barton August 4, 2016, China Resources C’estbon Beverage (China) Co., Ltd. We met: Mr Hans Hou, Vice General Manager Mr Chen Jing, Purchase Department Mr Lu Jing, Factory Management Department The southern Chinese city of Shenzhen, which is near the border with Hong Kong, is home to the headquarters of drinks manufacturer C’estbon. Although the name suggests a French origin, the company was actually founded in Shenzhen and continues to be managed from there, to this day. The company was established in 1984 as the Chinese Longhuan Beverage Co. Ltd., is currently the leader in bottled water in a number of regions in the country, and generated turnover of more than US$1.5bn in 2015. It is currently owned by China Resources, the stated-owned investment holding company, which is based in Hong Kong and is active in a variety of business sectors. Its drink production operations supply a range of supermarket chains. PETplanet Insider got to hear all about how Hans Hou and other leaders of the supply chain team participated in and witnessed C’estbon’s progress and success. Hans Hou, C’estbon’s Vice-General Manager, also holds the position of Vice Chairman of the China Beverage Industry Association. With him in conference were Chen Jing, Deputy General Manager of Purchase Department, and Lu Jing, Deputy General Manager of Factory Management Department. Different PET bottle sizes for C’estbon water","@ID":38}, "LABELLING 54 PETplanet Insider Vol. 17 No. 10/16 petpla.net with much more creative opportunity when compared to the limited space of traditional labels. As the designer’s role is to make the packaging as attractive as possible to the consumer, this freedom generally leads to more innovative and eye-catching layouts. The extra space also allows the positioning of data such as volume, contents, barcode and other legally required information, in addition to enabling producers to add messages and communications of their own choice. Labels to cover all or part of the bottle By applying film sleeves to entire bottles or parts of bottles, the SSL application involves shrinking the film with heat, causing it to follow the shape of the container to which it is being applied. As it shrinks into place, it adapts to any surface and eliminates any irregularities or restrictions due to container shape. The film can be used to cover the bottle in a number of different ways, too. It might cover part of the bottle - just the cap and shoulders, for example - or the whole bottle. Other means of application include stretch sleeves and roll-on, shrinkon (ROSO) systems. By covering the whole bottle, including the cap, the label sleeve can serve effectively as a seal and, in the case of sensitive products, it can also be used as a light barrier to protect the contents. Fullbody sleeve labels additionally enhance the potential for further lightweighting, as they can strengthen the bottle walls, improving handling performance and the whole consumer experience when applied to lighter bottles. To take advantage of the many positives that the sleeve labelling process and the new substrates offer, equipment manufacturers have been working to develop machinery that fits in more closely with producers’ needs. This has led to the production of machines that combine the simplicity of consolidated roll-fed technology with shrink-sleeve processes for highspeed applications. Labelling onto ultra-lightweight bottles Within most labelling equipment, labels are applied to the bottles by machinery separately handling each bottle. This handling might weaken an ultra-light bottle in some manufacturers’ systems. This can result in poor quality labelling and reduced machine efficiency. To overcome the problem, some producers are ‘nitrogen-dosing’ their beverages - that is adding liquid nitrogen to the filled bottle prior to capping. When a droplet of nitrogen is added to the filled bottle and trapped by the capping process, it expands as it vaporises. This greatly increases the pressure within the bottle and has the effect of strengthening the bottle. Naturally, leading equipment manufacturers are already building labelling machines that can handle even the most lightweight bottle and manage the extra demands of bottle lightweighting - without the need for nitrogen dosing. Compared to traditional Transversal Direction Orientation (TDO) where sleeve labels are already formed in tubes on the reel, the sleeve labelling solution from Sidel, the Rollsleeve, can apply labels with a Machine Direction Orientation (MDO) on very lightweight bottles, as the final tube creation and welding are performed directly in the labelling machine. Labels for product personalisation Inventing ways in which the consumer experience can be made more personal is a current trend within buying public. This is one reason why SSL, which affords greater freedom for graphic design, is growing rapidly in popularity, particularly among those producers operating in well-established markets. The larger area available for graphics naturally presents designers","@ID":56}, "BOTTLING / FILLING 32 PETplanet Insider Vol. 17 No. 10/16 petpla.net SPONSORS The China Road Show fulfilment of customers’ requirements. Eight of the 17 plants in China are OEM bottling plants only. The company works with all of the well-known national and multinational brands. In China, these include Coca-Cola, PepsiCo and Danone. The company is currently valued at around US$430m. During my stay in Taichung I got to visit one of the two plants there that bottle solely on an aseptic basis. Long standing business relationships with suppliers such as Sidel and Husky are reflected in the state-of-the-art equipment. At this plant, THC bottles tea and coffee products. During my visit a batch of up to 36,000 bottles of aseptically bottled water, packaged under the Coca-Cola Group Shuisenhuo brand name, was running on the conveyor belt. This was a rare sight that I was quite privileged to witness. The Taichung factory’s equipment includes a Sidel SBO 20 blower, FMa 70/20, a labelling machine and multi-packing machinery from SMI Italy, for shrink-wrapping and subsequent packaging in cartons. The factory produces around 40 different products, in approximately 180 million cartons each year, in 600ml and 975ml standard bottling sizes. The preforms, which are produced on Husky equipment, feature an 1881 neck finish and weigh 20-37g. For the Taiwanese market the company uses G-line, HyPET 3.0, HyPET 4.0, and HPP Husky machines, which produce 1.6bn of the group’s 10bn total preform output, which are destined for both further processing as co-packers and for straightforward sale. At its second aseptic plant in Taichung the company recently installed a complete Sidel solution, consisting of a Combi Predis FMa Capdis with a blowmoulding, bottling and sealing unit. With its deployment of dry decontamination technology, with the preform and seals, this plant is able to achieve an output of up to 40,000bph. When I arrived in the headquarters, Julia Tang, Sales Representative, and Joanne Liu, Project Manager Trading Department guided me through THC’s World of Information, while we discussed company philosophy and (PET) packaging. The real fossils in the marble flooring of the entrance area are supposed to symbolise history, the presentation of a group of flying geese symbolises teamwork, while a large scale, reallife stalactite aims to sharpen one’s sense for small-scale and continuous change and its impact. On the first floor, visitors find the packaging museum and the PET bottle skywalk. The museum is home to fixed exhibits and to 900 information sheets that provide information about them. A step-by-step history of packaging is displayed on a series of touch screens. This section also features a product showroom, a hall of company awards, an interactive PET game and much more; it is the permanent manifestation of THC’s strategy and “open house” orientation. It would be quite possible to spend a few hours on the first floor – but the second floor features a fully equipped cinema which, in addition to showing movies, is used for meetings and presentations. It was there that I was introduced to Keith Dai, whose father founded the company. He assumed the role of company Chairman in 1996. “We serve global players as well as small, local companies. But we do much more than just that. We want to communicate our philosophy and mission in society as a whole,” Dai explains. “It isn’t just about making profits, but ensuring that our work and our service is received positively at the local level and that its philosophy is understood. Regardless of the changing technology behind the global manufacturing of drinks, drinks will always be a necessity.” “When we talk about packaging, the environmental perspective should be one of the top topics,” he continues. “In the future, in my opinion,","@ID":34}, "MOULD MAKING 20 PETplanet Insider Vol. 17 No. 10/16 petpla.net SPONSORS The China Road Show New manufacturing locations abroad The vision of 25% exports By Kay Barton August 6, 2016, Guangdong Yizumi Precision Machinery Co., Ltd. We met: Mrs Karen Yu, Overseas Marketing Director Mr James Zhang, Director & Deputy General Manager Mrs Maggie Chen, Sales Assistant When PETplanet Insider interviewed Yizumi Precision Machinery Co., Ltd., a mechanical engineering company from Foshan during Chinaplas 2015, we learned about the company’s journey from foundation to the present day. The report was published in issue 09/15. On our return to the country as part of the China Road Show, I was able to find out more about its development and history, “live” and “on location”. Yizumi is made up of six divisions: Injection Machinery, Die Casting Machinery, Rubber Injection Machinery, High Speed Packaging, Robotic Automation and Moulds. It maintains four factories in the local region, including one acquired through the takeover of a mould maker. Its manufacturing facilities and headquarters at Gaoli in Shunde, Foshan, include an extensive range of park and sports facilities for the employees, and extend to an area of almost 7,500m2. As I later found out, ensuring that the employees are involved and happy is one of the company’s top priorities, which is why it invests a lot in its staff leisure and recreational facilities. In addition to the administration and development departments, the location is home to the construction of die casting, rubber injection and packaging machines, as well as moulds. It is here that I met with Overseas Marketing Director Karen Yu and Maggie Chen, Sales Assistant, and found out more about the corporate strategy. Since my last meeting and interview, the company has been listed on the stock exchange. Yu showed me around the individual divisions. In the packaging machines division, I came across systems from the PET-A2 series, which we reported on previously. “We have defined some clear goals for the end of 2018. We want to maintain an average annual growth rate of 20% within China,” Yu says. “We are one of the top three companies in the Chinese market with our injection machines, and in the top two for die casting and rubber injection machines.” Yizumi is focusing strongly on its international business. It is seeking to drive exports to the level of 25% of its business and it is planning to build additional manuSet in stone: Karen Yu with Kay Barton at Yizumi’s company entrance","@ID":22}, "CAPPING / CLOSURES 48 PETplanet Insider Vol. 17 No. 10/16 petpla.net Please order your copy at the PETplanet Insider book shop: https://petpla.net/books Bottles, Preforms and Closures - A Design Guide for PET Packaging Second Edition by Ottmar Brandau € 115,00 180 pages © Copyright Elsevier 2012 * This article was published in Bottles, Preforms and Closures, Ottmar Brandau, Chapter 4.5 and 4.6 Copyright Elsevier 2012 4.9 General IM Process Parameters for CSD Closures The process steps for injectionmoulded caps for CSD applications are much alike. However, there are minor differences to be found depending on cap design, gating solutions, and resin as well as machine capabilities. The following information represents a typical cycle time breakdown for a 28mm CSD cap (Figs 4.38–4.40, 4.47, and 4.48). Figure 4.38 Typical cycle time breakdown for injection moulding of CSD caps (picture courtesy of Corvaglia Ltd.) The cap’s physical, as well as optical, performance is quite often related to certain process steps as follows: 4.9.1 Injection Time The injection time depends on three factors: the machine, the mould design, and the plastic resin. 4.9.1.1 Machine Depending on the IM machine capability, the injection speed as well as the resulting injection pressure is subject to optimisation. 4.9.1.2 Resin Some resins cannot be injected with high speed, as degrading or burning effects would occur. The higher the melt flow rate of the resin, the faster the injection can take place. 4.9.1.3 Cap and Mould Design 4.9.1.3.1 Number of Cavities The more cavities a mould has, the longer it takes to fill. With cold runner systems, the length of the runners requires additional resins, shot for shot. In hot runner moulds, the pressure drop will increase by every additional cavity installed. The smaller the pressure drop, the faster the mould will be filled. 4.9.1.3.2 Product Shape A product having a short flow path and a heavy wall thickness offers the best conditions to achieve the shortest possible fill times. 4.9.1.3.3 L over t Ratio The ratio between flow path (L) and wall thickness (t) influences the fill speed drastically. The higher the ratio, the more injection pressure will be required to fill the product. This high filling pressure requires much more clamping force to counteract. In addition, the mould is under higher load. 4.9.2 Hold Time Cap designs with heavy wall cross sections shrink considerably after the injection process step and may show sink marks because the resin solidifies and continues to do so although in contact with intensely cooled mould surfaces. The purpose of the hold time is to maintain pressure on the melt in order to finalise filling while the product shrinks in the cavities. The quality of the products gating area is also influenced by the injection–hold process step. 4.9.3 Cooling Time The cooling time parameters used depend on two major factors: cap and mould design as well as cooling water supply of the moulding plant. The cooling water temperature should be within a range of 8-14°C. In order to achieve the best possible cooling time, the cooling water should be delivered at a system pressure between 4 and 6 bar measured at the mould. A proper control can be achieved if the system water pressure is monitored at the inlet as well as the outlet of the mould cooling. A maximum pressure difference between inlet and outlet is required to receive maximal water flow. All connections must be of adequate cross section, installed and laid out correctly, avoiding kinks that cause flow restrictions. Preferably, clean, filtered, and treated water which will not clog or corrode the cooling channels should be used. The mould design also has an impact on the ideal cooling time. By optimising the wall thickness of the part forming components as well as the cooling water flow rate, the cooling time can be tuned to a minimum.","@ID":50}, "BOTTLING / FILLING 31 PETplanet Insider Vol. 17 No. 10/16 petpla.net gwk Gesellschaft Wärme Kältetechnik mbH Scherl 10 · D-58540 Meinerzhagen Tel. +49 2354 7060-0 Fax +49 2354 7060-156 [email protected] · www.gwk.com PERFECT COOLINGANDTEMPERATURE CONTROL. Worldwide. Profile of Taiwan Hon Chuan equipment in China Suzhou Plant (Headquarters) Compression moulding machine: Sacmi x4, others x10, printing machine x4 Shandong Jinan Plant Bottle blowing machine: Sidel (SBO14, SBO8), Krones (S-14) Injection moulding machine: Husky (G-PET 56, G-PET 72, HyPET 72) Compression moulding machine: Sacmi x10 Suzhou Hongxing Plant Bottle blowing machine: Sidel (SBO14-01, SBO14-02, SBO14-03, SBO10, SBO6, SBO8) Injection moulding machine: Husky (G-PET 72, HyPET 72), Netstal (NS 96) Shanxi Taiyuan Plant Bottle blowing machine: Sidel (SBO14, SBO8, SBO20), Krones Injection moulding machine: Husky (G-PET 56, G-PET 72, HyPET 72-1, HyPET 72-2, HyPET 96) Compression moulding machine: Sacmi x9, others x2 Hubei Xiantao Plant Bottle blowing machine: KHS Injection moulding machine: Husky (G-PET 72-1, G-PET 72-2) Hunan Changsha Plant Bottle blowing machine: Sidel (SBO14, SBO8) Injection moulding machine: Husky (G-PET 56) Compression moulding machine: Sacmi x4, others x7 Guangdong Qingxin Plant Bottle blowing machine: Sidel (S-01, S-02) Injection moulding machine: Netstal (NS 96), Husky (G-PET 72-1, G-PET 72-2, HyPET 96, HyPET 72), TMC (T-1, T-2) Compression moulding Machine: Sacmi x19, others x1 Printing machine x2 Fujian Zhangzhou Plant Bottle blowing machine: Krones (S-14-1, S-14-2) Injection moulding machine: Husky (G-PET 72-1, G-PET 72-2) Yunnan Kunming Plant Bottle blowing machine: Sidel, Tech-Long Injection moulding machine: Husky (HyPET 72), Unique (UP 72) Henan Zhengzhou Plant Bottle blowing machine: Sidel (SBO24) Injection moulding machine: Husky (G-PET 96) Hubei Wuxue Plant Injection moulding machine: Husky (G-PET 72) Anhui Chuzhou Plant Injection moulding machine: Husky (HyPET 96, G-PET 72-1, G-PET 72-2, G-PET 72-3), Milacron (MG 32-1, MG 32-2, MG 32-3, MG 32-4) Compression moulding machine: Others x1 Shaanxi Xian Plant Injection moulding machine: Unique (UP32) Henan Gongyi Plant Compression moulding machine: Sacmi x2, others x1 Jilin Changchun Plant Compression moulding machine: Sacmi x1 Henan Anyang Plant Compression moulding machine: Sacmi x1 Anhui Lu’an Plant Compression moulding machine: Sacmi x1, Other x2","@ID":33}, "CAPPING / CLOSURES 42 PETplanet Insider Vol. 17 No. 10/16 petpla.net Different applications, neck finishes for various, part 9 Closure for PET bottles & Resins PETplanet Insider is publishing extracts from successive chapters of Ottmar Brandau’s “Bottles, Preforms and Closures,” which was published by hbmedia. A newly revised version is reissued under the Elsevier imprint. 4.6.2 Compression Moulding CM machines work very differently from IM machines. There is of course an extrusion screw, but it is running continuously because the screw has no part in the transfer of the molten plastic into the mould. Single-cavity tools are mounted on a rotary table with practically no limitation as to maximum cavitation. Figure 4.36 shows the various stations of the machine with the extruder on the left and the wheel turning counterclockwise. A drop of precisely measured resin, cut from a continuous extruded stream, is placed into a transfer wheel. The same wheel also takes finished caps out of the main wheel. At position (1) the transfer wheel comes to a position above an empty cavity of the main wheel and drops the plastic into it. At position (2) the cavity lifts vertically up into the core and the actual moulding takes place. In position (3) the plastic now spreads between core and cavity, climbing up the cap sidewalls under relatively low pressure. It therefore leaves no sprue point, which may be a great advantage should the cap surface need decorating. During position (4) the fully formed cap is now cooling. In position (5) the cavity moves down leaving the cap on the core. In position (6) a stripper ring pushes the finished cap onto the transfer wheel. An additional transfer wheel then places the finished caps onto a conveyor (Fig. 4.37). Figure 4.36 Schematic of compression machine cycle (picture courtesy of Sacmi)","@ID":44}, "TRADE SHOW PREVIEW 69 PETplanet Insider Vol. 17 No. 10/16 petpla.net PROCESS PILOT® makes producing a better PET bottle as easy as 2 3 1 MEASURE CONTROL OPTIMIZE every bottle for changes in material distribution process variation, inside the blowmolder material utilization and orientation to achieve maximum bottle performance CONTACT US TODAY TO LEARN MORE! AGRINTL.COM | +1.724.482.2163 | [email protected] VISIT US AT BOOTH 11B40 NGR Hall 9 Booth C30 Recycling solutions The Austrian-German Next Generation Group, comprised of Next Generation Recyclingmaschinen GmbH, BritAS Recycling-Anlagen GmbH and Dr. Collin GmbH, is showcasing new processing methods, technology and profit-generating services along the plastics value chain. Widening the lead in plastics recycling technology S.M.A.R.T. Dialog from NGR is intended to virtually enable the machinery to speak, and it provides the process analyses to ensure recycling success at minimal cost alongside key operating data. As part of a live demo, the system will be demoed for the professional audience on mobile devices. Many steps are increasing the output of NGR systems while also providing lower energy consumption. The P:React series will be presented for the first time; it follows the new LSP process (world premiere). With this technology, rPellets with better properties than virgin material can be produced and decontaminated reliably and within minutes, according to the company. Additional offerings in the area of post-consumer recycling further round out the NGR range of products and services. “Zero scrap production” in live demo At the booth, a new pilot plant solution from Dr. Collin will manufacture PP film. The film edge trims and film rolls will be further processed into rPellets by an NGR recycling machine. The processed plastics will then be returned back into film production. An inline melt characterisation unit developed by Collin will also provide advanced quality control of the new plastics raw material during the recycling process. In this setup, the processing parameters will be further monitored, recorded and analysed in real-time on the recycling machine, and displayed for attendees on mobile devices in easy-tounderstand charts. This new form of human-machine communication is designed as S.M.A.R.T. Dialog: it provides for considerably improved equipment utilisation, rationalisation in terms of service and maintenance, and provides all the data to evaluate the recycling investment. In live operation, Collin laboratory and pilot systems will show how plastics and processing methods, in both the raw materials industry as well as in plastics converting, can provide the basis for even higher-performance product design. Modularity, precision, flexibility and the highest repeatability are all achieved. This year, Collin will provide a live demo at the NGR booth of an interesting technology for post-industrial and post-consumer recycling. Continual development of filtration technology The melt filtration system plays a critical role in the production of high-quality post-consumer pellets. BritAS will present the latest version of its successful band-melt-filter which is claimed to be easy to operate, to support more flexible applications and to allow for minimal operating costs. www.ngr.at www.britas.de www.drcollin.de","@ID":71}, "BOTTLING / FILLING 33 PETplanet Insider Vol. 17 everything will have to, or should be set up on a bottle-to-bottle basis, which certainly isn’t an easy goal to achieve. However, we are working on getting it established. In the future there will be many applications for PET bottles, with the example of milk products, for instance.” I dug deeper and asked about specific uses of PET for new product groups. “Beer is certainly an interesting and - above all else - a gigantic market. We are naturally fighting for the widespread acceptance for beer coming in plastic packaging. At the same time, the costs for the changeovers aren’t low.” Looking at the company and its development, the question of further options for expansion inevitably arises. Dai sees considerable potential in South East Asia. “Even though we’ve been active here for many years, we still see increasing demand,” he observes. “If you look at annual growth rates in GDP, in comparison with other markets such as China, we can expect these markets to provide a lot of business for us.” One forward-looking piece of technology that the company is now introducing, in the course of the increasingly widespread use of IoT (“Internet of Things”), is the integration of QR codes on the inside of caps. These are used for a variety of applications, including interactive advertising, the tracking of production processes, providing product information and online sales. Manufacturers will also be able to receive ad-hoc feedback from the market on the product and to categorise customers. On this basis, every cap can be given its own code. www.honchuan.com.tw You make a great product – why hide it? We’ve seen the future of canning and it’s Klear. Milacron’s Klear Can technology gives manufacturers a cutting-edge, cost-competitive alternative to metal cans for fruits, vegetables, soups, meats and other products – and it’s transparent, so you can show off your goods. Using the same machinery as metal cans, going Klear requires minimal investment. With the option to use colored plastic cans, in-mold labels, or standard labels, the possibilities are endless. Ready to see what you can do? Contact us or visit www.Milacron.com to learn more. October 19-26, 2016 Hall 15/C06, Hall 01/A39","@ID":35}, "TRADE SHOW PREVIEW 68 PETplanet Insider Vol. 17 No. 10/16 petpla.net K 2016 – 2nd part of the PET selection K 2016 is opening its doors in Düsseldorf, Germany at 10 a.m. on October 19th. Tickets can be purchased online, printed at home or downloaded as codes, saving both, time and money. Possession of a ticket includes free of charge travel to the trade fair by bus and rail in Düsseldorf. In our second trade show preview, we have gathered a new selection of exhibits which are sure to be of interest to the PET beverage industry. www.k-online.com Erema Hall 9 Booth C05 & C28 Careformance: Erema launches recycling 4.0 At the K 2016 show, Erema will be building on the success of the Intarema technology presented in 2013, this time with its trade fair theme of “Careformance – We care about your performance” to grow its pioneering role with Industry 4.0 applications. Careformance consists of four components, with the Intarema system forming the basis for further smart factory applications. In addition to previous machine data, specially integrated sensors – the QualityOn package – can be used in the future to record and evaluate Melt Volume Rate (MVR), colour and moisture. The QualityOn package enables recyclers and producers to make their recyclates with consistent quality in accordance with the special requirements of their customers and document them transparently using online data acquisition and analysis. Recipes recorded electronically can be compared with each other and modified. In order to make use of the vast amount of machine, quality and process data in a worthwhile and user-friendly way, Erema has developed a sophisticated Manufacturing Execution System (MES). With re360 one can keep track of the productivity of an entire range of machinery in five modules. The extent to which re360 was developed with customer requirements in mind becomes clear with the link to Spare Parts Online, Erema’s online webshop. Any upcoming maintenance work and the replacement of individual parts are displayed in good time by re360. Spare parts can be ordered directly via the online webshop to keep downtime as low as possible: interconnection in the sense of maximum productivity. The customers’ respective Erema systems and previous orders are stored at Spare Parts Online. www.erema.at Laser-marking of monolayer dairy PET packaging Holland Colours has introduced a new generation of their light barrier technology for UHT milk packaging, Holcomer III. It is said to include enhanced light-barrier and laser-marking benefits such as 100% UV blocking and up to 99.9% visible-light blocking in a monolayer PET bottle, but with lower production and laser-marking costs. Laser-marked letters and numbers are clearer and easier to read than printed ones, and unlike those cannot smudge or be accidentally wiped off. Holcomer III is claimed to overcome the traditional challenge posed by laser-marking monolayer PET milk bottles. The core of the issue is that organic polymers like PET show only limited sensitivity to IR lasers used in laser marking, so laser additives have to be added for the technique to work. However, these additives can cause a slight influence on the colour (greyish), which is exactly what you do not want in pure, dairy applications. But using Holcomer III, producers can maintain the snow-white dairy appearance of the bottle without compromising the legibility of the laser marking. www.hollandcolours.com Holland Colours Hall 7.1 Booth E45","@ID":70}, "TRADE SHOW PREVIEW 75 PETplanet Insider Vol. 17 No. 10/16 petpla.net W W W . I N T R A V I S . C O M V I S I T U S A T 2 0 1 6 H A L L 1 1 , B O O T H A 5 8 Will tomorrow’s batch be flawless, too? We tell you. Today. The five pillars of plastics recycling The machine and plant manufacturer Herbold from Meckesheim, Germany will present their five pillars for an efficient and cost-effective recycling of plastic waste. In the first pillar, the company identifies solutions for presize-reduction if the feeding material is too bulky for the usual procedure or if the material is in a first step only to be coarsely shredded for a subsequent sorting, classification or inspection. Size reduction is said to be the second pillar. In Herbold’s patented granulators with forced feeding of the SB type, the material is not fed into the grinding chamber by gravity but as a continuous and even flow by means of feeding screws. Pillar 3 is assigned to fine grinding. Herbold impact disc pulverisers are high-speed fine grinders (pulverising below 1mm), used with granular and brittle materials. In pillar 4, washing, separating and drying, end of life post-industrial and post-consumer plastic products are used, mixed and contaminated plastics. Before they can be used again, they have to be washed and/or separated. With the commissioning of the film washing line at Rodepa Plastics B.V. Herbold Meckesheim proved that a high-quality end product can be obtained by separating undesirable plastics with the hydrocyclone separation step. The fifth pillar refers to agglomerating/densifying. With extreme materials such as stretch film or foams, a sufficient mechanical or thermal drying is not possible without high energy consumption. As a solution, Herbold presents its Plastcompactor compacting machine. The friction originating between the compacting discs of the compactor heats, dries and compacts the material at the same time. The recycling of PET bottles has a double advantage: the material is being crystallised at the same time. The end product is said to be agglomerated material with good flow properties and a high bulk density, ideal for dosing and mixing. www.herbold.com Plastcompactor HV Series (exhibited will be the HV 50 with new feeding device) Herbold Meckesheim Hall 9 Booth B42","@ID":77}, "TRADE SHOW PREVIEW 81 PETplanet Insider Vol. 17 No. 10/16 petpla.net Reprocessing of PET industrial and post-consumer waste Purified polymer The Gneuss Processing Unit (GPU) has been available for several years now and has proved itself on the reprocessing of bulky PET waste such as post-consumer bottle flake and industrial waste from fibre and film manufacture. This GPU consists of the Gneuss MRS extruder with its devolatilisation and decontamination performance together with the Gneuss Rotary Disc melt filtration systems and the Gneuss Online Viscometer for intelligent dynamic viscosity control, monitoring and logging. Since the last “K“, Gneuss has continued with its intensive development programme, so that the MRS extruder is claimed to represent a robust, rugged and reliable system especially tailored for recycling applications. Gneuß Hall 9 Booth A38 Subsequently, the purified and homogenised polymer is fed by means of a melt pump into the Jump, where the second important stage of the process takes place. Here, too, a large surface area of the polymer melt and optimum residence time of the polymer under vacuum are decisive factors. The polymer melt is kept under vacuum as it passes over slowly rotating elements. Through control of the residence time and the speed of the rotating elements, controlled polycondensation takes place, whereby controlled IV boosting of typically 0.02 to maximum 0.3dl/g is achieved. The design of the Jump system avoids the ingress of oxygen, so that the yellowing effect encountered during the recycling of PET is reduced to an absolute minimum. After the PET melt has passed through a stilling chamber in the Jump system, the polymer is pumped directly into the production process (for example direct extrusion spinning, strapping) or to a pelletising (chip cutting) system. The Jump system is available for different capacities of between 100 and 2,000kg/h. At the “K”, Gneuss will show an MRS 90i for a throughput rate of 400kg/h, for industrial waste recycling with intermediate material buffer, auger and crammer/feeder. The extruder is coupled to the new Jump system, model V600. www.gneuss.com A further development is the extension of the venting system with several openings in the barrel. Depending on the application, these additional openings can be in the form of several openings in the MRS section of the barrel or venting ports in the barrel of the plasticising section. Additionally, the company has developed the Jump system. This is installed directly downstream of the Processing Unit and is intended to ensure an accurate and controllable IV boost of the PET by up to 0.3 in the melt phase. The Jump system is claimed to be a compact, quick and efficient alternative to conventional SSP (solid state) systems and enables direct reintroduction of the polymer into the production process without the need to remelt the PET. Depending on its properties, industrial waste is first fed through a shredder or a knife mill until the size is reduced so that it can be fed into the extruder. This can mean either compaction of the size reduced waste or a crammer feeder fitted directly to the extruder. The first important processing stage: melt decontamination takes place in the extruder. With its devolatilisation capacity, the MRS extruder can process PET waste with high residual moisture levels and/or contamination (such as spin finish oils) without the need for any pre-treatment of the waste. In the Multi Rotation section (MRS) of the extruder a huge polymer surface area and rapid surface exchange rate under vacuum ensure that all these volatile contaminants are reliably extracted. Solid contamination is extracted with the fully-automatic and process-constant Rotary Melt Filtration System. With filtration finenesses of down to 20μm and below, a pure and particle-free polymer melt is guaranteed. Industrial waste recycling line as to be shown at the „K“: MRS 90i extruder equipped with dosing feeder and crammer – feeder system, Rotary Filtration System RSFgenius, Online Viscometer VIS and Jump system. IV boosting system Jump","@ID":83}, "MATERIAL / RECYCLING 12 PETplanet Insider Vol. 17 No. 10/16 petpla.net Comparison of MTR versus SSP Concepts for bottle grade PET by Martin Hittorff, Uhde Inventa-Fischer Product Management PET and HOD Process Department The challenges for the producers of PET are numerous including maturing consumption levels and the trend to lightweight bottles, the uncontrolled fluctuation of prices for raw materials and energy, the competition of mega-plants and regional protection duties. Uhde Inventa-Fischer in 2007 has given an answer to those challenges named Melt To Resin (MTR) technology. MTR is a completely integrated one-stage process providing bottle grade IV PET melt directly from the Discage reactor (finisher). PET is produced from the raw materials purified terephthalic acid (PTA), isophthalic acid (PIA) and ethylene glycol (EG) using a melt polycondensation process. Conventional routes have in common that they require a second, subsequent solid-state post-condensation (SSP) step to further increase the molecular weight of the polymer. During this solid-stating, PET precursor chips are typically subjected to a temperature above 220°C under a counter-flow of purified nitrogen. However, the SSP stage is energyconsuming and, as it is an extra step, it also has the disadvantage of requiring additional plant equipment and operating personnel. Execution of MTR MTR technology requires a special design of the melt distribution system from the outlet of the Discage reactor to the cutters and a solid processing step called Chips Conditioning to achieve the final low acetaldehyde (AA) content of the resin. MTR technology is proven, since there is more than 3m t/a of PET resin capacity in operation. With MTR customers are able to produce at or over nominal capacity and downstream users of PET make use of specific features of MTR resin like low heat of fusion, low dust content, uniform IV in pellets and dust and low AA re-generation. Recently the leading supplier for SSP technology introduced the use of an under-water cutting system to keep the temperature of the PET pellets on a high level. For the sake of easy distinction we shall name this process “new style” SSP, which will definitely reduce energy consumption compared to the “old style” SSP. However, even the “new style” SSP is using external energy input at the crystallisation stage and is operated at high temperature and under nitrogen atmosphere, which requires the operation of huge blowers, additional conveying systems and a nitrogen purification. In the subsequent diagrams the MTR technology is compared to “old style” and “new style” SSP technology. Investment (Capex) and Operational Cost (Opex) are based on realistic consumption figures published by the technology suppliers and site conditions for the case of a 750t/day site located in South-East Asia. The main driver for the lower Capex cost of the MTR technology is the fact that no investment is required for the SSP equipment, SSP building and SSP erection. Fig. 1: Process block diagram of the three competing concepts for production of bottle grade PET resin","@ID":14}, "MATERIAL / RECYCLING 14 PETplanet Insider Vol. 17 No. 10/16 petpla.net Dust content and IV uniformity The MTR Technology provides low dust content of the product, even without installation of a de-dusting device, because of the use of an under- water cutting system and because of considerably fewer solid transport and handling steps. Furthermore in the MTR Technology the IV of dust particles and the IV of the PET pellets is identical, because there is very little IV-increase in the chip-conditioning system. AA content resin and AA content preform Comparing the AA content of MTR technology resin with SSP resin typically shows lower AA content for SSP chips. The reason is obviously the different focus of the final process step of the two technologies: MTR technology: Chips Conditioning = focus on AA removal SSP technology: SSP reactor = focus on IV increase With long residence time at a temperature of approximately 220°C in the SSP reactor, the AA content will automatically drop to very low values. UIF has run numerous trials at industrial scale preform machines, which all showed a significant lower AA content in preforms from MTR technology resin: MTR SSP IV resin [dl/g] 0.83 0.80 AA resin [ppm] 0.75 0.6 AA preform [ppm] 1.7-1.9 2.9-3.2 Table 1: Comparison of AA in preforms, Husky Hypet 300 72 cavities, 21.3g preforms, 285°C The reason for the lower AA content in preforms from MTR resin is the lower specific energy input during preform making, which has its explanation in the lower degree of crystallisation and the overall lower thermal stress of the MTR production process. Summary The latest development of “new style” SSP technology has definitely reduced the energy consumption compared to previous SSP technology. In one way it can be said that the SSP technology has finally followed the path that UIF has started with the use of the latent heat crystallisation in the MTR technology in the year 2007. But MTR is claimed to be still ahead of the competing technologies for the production of bottle grade PET resin with respect to total project cost, energy consumption, plant flexibility, fixed cost, raw material utilisation and maintenance cost. Additionally MTR technology is said to offer a variety of benefits for downstream users of PET resin, which include lower energy of fusion due to lower degree of crystallisation, low dust content and no difference in IV between normal size pellets and small size pellets or dust. MTR is intended to be one of the most economical ways to produce bottle grade PET resin fulfilling high product quality standards. www.uhde-inventa-fischer.com Fig. 6 Degree of resin crystallinity of MTR and SSP technology Fig. 4 Comparison of dust content and IV uniformity Fig. 5 Comparison of AA content of resin and AA-re-generation in preforms","@ID":16}, "TRADE SHOW PREVIEW 71 PETplanet Insider Vol. 17 No. 10/16 petpla.net Kreyenborg Hall 9 Booth A55 i NOCONSTRAINTS LABELINGMACHINE Interchangeable modules with or without cart. Free to decide how to fit your labeler at any time: before, during and after purchasing. Models for all speeds. CHOOSE THE SPECIALIST PH. +39 0376 389311 | MAIL: [email protected] WEB: www.pelabellers.com Hall W2 – Stand 2Y427 Drying, storing, mixing, conveying, dosing Kreyenborg Plant Technology GmbH, based in Senden, Germany will be putting particular focus on a range of topics regarding drying and crystallising, as well as comprehensive solutions for bulk-material handling processes. The Infrared Rotary Dryers IRD is used for crystallising and drying virgin or regrind materials for a number of plastics, including PET. Through the use of the continuously functioning IRD, the need for energy-intensive processing using dry air is said to be completely eliminated. The raw material is heated directly with infrared light that works especially gently, so that the vaporising moisture is diverted from the core of the material toward the outside. The raw material is conveyed evenly through the machine, and, by the rotating of the drum, carefully circulated and evenly heated. This eliminates clumping. The low rotation speed prevents breaking, abrasion and the raising of dust from the product. For the first time, Kreyenborg are presenting their new PET-Booster. This continuously operating system dries PET within 7-10m. The focus here is specifically on applications in the extrusion of plastic films and fibres with degassing extruders. Varying levels of input moisture that result in process fluctuations in the extrusion process (as well as fluctuations in end-product quality) can be eliminated with the PET-Booster. By feeding pre-heated material with a consistent, low input moisture level, a smaller extruder and vacuum degassing system can be used. Among the company’s new exhibits is a pneumatic conveying system. Thanks to many years’ experience with the conveying of poorly-flowing bulk materials - for example bottle flakes or film flakes, that still present a challenge to the industry - Kreyenborg has incorporated hopper loaders into the process. The conveyers are distinguished by their container geometries that avoid bridging and even have internal bridge-breakers. The containers come standard with an extremely large outlet. The conveyors have a compact central filter unit with a large filter area, to meet the requirements for dusty regrind materials. www.kreyenborg.com","@ID":73}, "INSPECTION 26 PETplanet Insider Vol. 17 No. 10/16 petpla.net Agr’s automated blowmoulder control ensures Sanpellegrino bottles align with distinct mineral water brands Control is better Joining the latest technology to its tradition, Nestlé’s Sanpellegrino Group relies on Agr’s Process Pilot Automated Blowmolder Control System to ensure that each PET bottle blown on the line has the desired quality and performance attributes - regardless of the environmental, equipment or material variations that might occur during the production process. A long-term relationship between Agr International (Butler, Penn., USA) and Sanpellegrino Group is enhancing PET bottle manufacturing across three of the five mineral water brands in the portfolio of the Italian company Nestlé Waters. A staunch practitioner of a “take-no-chances, measure everything” approach to bottle-blowing, Sanpellegrino has been a leader in embracing the progression of Agr’s on-line thickness measurement technology, today represented by the Process Pilot automated blowmoulder control system. Not only does the Process Pilot measure every bottle for changes in material distribution, but it also controls the blowmoulder proactively to manage desired distribution while the addition of CrystalView, Agr’s latest advancement, optimises bottle crystallinity/material orientation to maximise bottle performance. Especially with several efficiency and lightweighting initiatives in progress, these capabilities are key in allowing Sanpellegrino to achieve consistent bottle quality to meet each brand’s objectives. An integral part of the company’s market strategy is its commitment to delivering the same customer experience with every single bottle. “The customer experience is very important to us,” affirms Fabio Chimetto, Applications Group Packaging Manager, Sanpellegrino Group, headquartered in Milan. “We strive to give the highest quality - of the product and the container it is supplied in - for a given market.” Distinct terroirs, consistent experience Italy boasts one of the highest per-capita consumption rates of bottled water in the world. It’s no wonder, considering that geology has graced the country with an abundance of natural mineral springs, found all the way from glacial Alpine peaks to the volcanic terrain of Sicily. As in wine, terroir plays an important role in mineral water, with a particular set of characteristics tied to a specific topography. Unlike wine, however, variations in these characteristics are most unwelcome. According to Italian law, commercially bottled mineral waters must be recognised by the Ministry of Health, tested regularly, and certified to remain stable and constant throughout all four seasons. They must all be bottled at the source - no transporting or blending; one reason why the Sanpellegrino Group has five different offerings in the category. The brands span the spectrum from the namesake S.Pellegrino, favoured sparkling mineral water in fine dining, and its still mineral water companion Acqua Panna, to the premium Levissima, “Italy’s favorite local mineral water,” and Nestlé Vera, the everyday consumer product. In between is the regional stand-out Recoaro. The majority of the company’s output goes to market in PET bottles in a wide range of packaging formats and sizes - 0.25l, 0.33l, 0.5l, 0.75l,1l, 1.25l, 1.5l, 2l - targeted for retail sale. With production of this huge volume emanating from two dozen bottling lines operating in seven different plants spread across the Italian landscape, hitting the consistency bullseye is no mean feat. This is especially true when it comes to PET bottle-blowing, a function performed in-house at each individual site. The reason to self-manufacture is simple, Chimetto observes: “Transporting empty bottles would kill the business.” Process Pilot’s automated controls manage the blowmoulder to eliminate the effect of process and environmental variables that impact bottle material distribution. For Sanpellegrino Group’s Fabio Chimetto, it is critical for the customer to have the same repeated experience handling the bottle to protect the brand and retain market share.","@ID":28}, "TRADE SHOW PREVIEW 80 PETplanet Insider Vol. 17 No. 10/16 petpla.net Piovan supervision software for the smart factory Winfactory 4.0 This is not a new version of the historic Winfactory, which Piovan launched in 2008 as the first remote factory monitoring and control instrument. This new application is supposed to be ready for “Industrie 4.0”, the group of protocols and technologies, being implemented, that constitutes the core of the 4. industrial revolution: the digital manufacturing. The integration between the production, distribution and information structures of the manufacturing industry is the key Smart Factory concept. Piovan has implemented this with the evolution of its process control and management software based on the “Industrie 4.0” guidelines, creating communication networks with an exchange capacity well ahead of schedule (2020) to allow for connections between the various parts of the technological ecosystem. Ready to communicate Winfactory 4.0 uses OPC-UA (Open Platform Communication - Unified Architecture), the protocol selected by “Industrie 4.0” before issuing the Smart Factory specifications: developed by the OPC Foundation in 2015, it defines the communication rules and data exchange between the various entities that make up the system. Thanks to the use of this protocol, Winfactory 4.0 makes it possible to supervise and ensure dialogue between Piovan machines and machines of other manufacturers (OEM). There is no longer the need for an interface that “translates” the data provided by each device into a common format: the information exchange becomes immediate and the various systems can interact independently. A similar communication platform allows access and use of the software on tablets and smartphones. Despite the complexity of the technological challenge that Piovan undertook, Winfactory 4.0 allows the utmost flexibility in managing equipment and processes. Advanced management of energy use In parallel with the development of Winfactory 4.0, Piovan created a group of integrated functions that allow for the control of very accurate operative parameters to be used to manage factory energy sources: knowing how and why they are used for each individual process based on the production volumes, the efficiency level of their use is determined. The data volumes necessary to identify the KPI and best practices to adopt to optimise energy consumption, just one of the factors that greatly influences production costs, can be collected quickly from various factories that are far from one another. This is the Big Data collection and analysis concept, made sector-specific to meet the needs of Piovan’s clients. Winfactory 4.0: configurations Based on the type of industrial processing, Winfactory 4.0 can be configured in several ways. Piovan developed different modules to manage each situation, from the production of PET to flexible film preforms or preforms for specific sectors like the medical and automotive industries with a completely customisable setup for each aspect based on the particular type of process. The energy configuration is not specific for the plastic sector, but is focused on monitoring the use of energy based on the type of industry and can be integrated in all superior configurations. The possibilities of Winfactory are further extended by a series of optional and on-demand functions and services like, for example, tracking, OPC-UA server, remote assistance, line power, formula, production and necessary material reordering management. The system itself automatically manages the use of the lines based on what and how much must be produced, for example, by selecting to maintain the lowest possible critical level. For example, producing a lot with a certain formula is more convenient if it can be done at a factory that was already used for the same type of mix, since there are fewer interventions necessary to clean the machines. With the installation of the OPC-UA protocol, both the basic and additional Winfactory 4.0 features can be made available on the machines, systems and automation devices not produced by Piovan and can interface directly with the management system at the individual plant as well as the company network. In this way, information can be shared between the various systems and data can be collected to optimise the processes, creating the Smart Factory of the fourth industrial revolution. Piovan’s new Winfactory 4.0 will allow for the optimisation of all processes, the qualitative improvement of production and evolution towards more efficient manufacturing in the use of global energy resources. www.piovan.com Piovan Hall 9 Booth C59","@ID":82}, "TRADE SHOW PREVIEW 77 PETplanet Insider Vol. 17 No. 10/16 petpla.net Effect pigments and additives for the food and cosmetics packaging markets Colour: from idea to production Masterbatches, pigment mixtures, liquid dyes and colouring pastes: the precise and quick translation of a colour idea into a production-ready colouring and additive system is the core competence of Karl Finke GmbH of Wuppertal, Germany. The company will be presenting a range of colourings with a focus on innovative effect pigments and new additives for irreversible laser marking. The company’s recentlyannounced collaboration with dosing technology specialist Movacolor will, they claim, set new standards for Finke’s Fibasol liquid colourings. Finke Hall 7.1 Booth A08 cal properties of the material, they are claimed to be the right choice for transparent applications. Blow moulding equipment Finke recently upgraded its technical centre in Wuppertal, Germany with new equipment for PET blow moulding, which is intended to speed up the development of design concepts for PET dyeing. The new equipment is intended to make the transition from concept to production-ready colouring and additive systems even faster. “Comprehensive advice and support for our customers from design stage to end product is very important to us”, says managing director Felix Finke. “With PET becoming more and more important in the packaging market, the new PET bottle moulding system was the logical next step in the development of our technical centre.” Finke keeps the complete new formula production and development process in vision. Colourists and technicians work with customers’ original material. Individual production conditions are simulated in Finke’s state of the art technical centre, because the right dye or pigment composition depends not only on the polymer and envisaged application but also, to a large extent, on the type of processing. OEMs and brand manufacturers will be able to save valuable time, because the dyeing systems are perfectly adapted to their needs and can be applied in their production processes immediately. Apart from the new PET blow moulding system, Finke operates several injection moulding systems as well as film and sheet extruders. PE and PP bottles can be produced in mono- and co-extrusion processes. www.finke-colors.eu The aesthetic appeal of plastics products depends on colour and colour effects. Finke’s Fibaplast, Fibafekt or Fibacomp masterbatches enable a wide variety of special effects, such as metallic gleam, pearly shine, rainbow and colour flop, to be realised. Special technical processes allow for lacquered-like finishes or soft-grip surfaces. Even fragrances can be incorporated into the material. Apart from an abundance of aesthetic effects, Finke masterbatches are supposed to enable a number of functional solutions for the indelible product marking, including invisible safety formulations and additives for irreversible laser marking. Dosing of liquid colourings: new cooperation Perfect dosing of liquid colourings is essential in the injection moulding process. In order to help improve performance even further, Finke has entered a collaborative alliance with Movacolor, the dosing technology specialist. The exact coordination of Fibasol liquid colourants with Movacolor dosing technology results in a ready to use system for plastics producers. Fibasol liquid dyes are pigment mixtures in a liquid binding agent; they can be used in almost all thermoplastics. In contrast with masterbatches, they are not restricted to a particular polymer carrier, which means that the same dye can be used for colouring a variety of plastics. These liquid dyes are declared to be temperature resistant, nonfading and physiologically harmless. This means that they are suitable for the colouring of PET, PE or PP food, or for cosmetics packagings. As they do not impair the physical or chemi-","@ID":79}, "MARKET SURVEY 50 PETplanet Insider Vol. 17 No. 10/16 petpla.net 10/2016 MARKETsurvey Company name Kaeser Kompressoren SE Siad Macchine Impianti Gardner Denver Ltd Postal address Telephone number Web site address Contact name Function Direct telephone number Fax E-Mail Carl-Kaeser-Str. 26 96450 Coburg, Germany +49 9561 640 0 www.kaeser.com Mr Wolfgang Hartmann Marketing Manager +49 9561 640 252 +49 9561 640 890 [email protected] Via Canovine, 2/4 24126 Bergamo, Italy +39 035 327611 www.siadmi.com Mr Giovanni Brignoli Compressor Division, Food & Beverage Product Leader +39 035 327609 +39 035 327694 [email protected] Claybrook Drive, Redditch, B98 0DS, Great Britan +44 1527 838600 www.gdhighpressure.com Mr Trevor Perry Sales Director +44 1527 838601 +44 1527 838630 [email protected] 1. Machine designation / model number Sigma PETAir BS Line VITO VH & WH Range 2. Number of models in range 25 19 21 13 3. Output in m³/hour 336 - 2,772 1,000 - 6,000 300 - 5,500 420 - 3,200 4. Compressor type High pressure blowing air (up to 40 bar) Low pressure air Screw type Low pressure screw High pressure blowing air (up to 40 bar) Piston type High pressure piston (booster) Piston Single 3 stage reciprocating machine Integrated system 5. Lubricated or oil-free Oil free Oil free Low pressure compressor Lubricated Oil free Booster compressor Lubricated Oil free Integrated system Yes Yes 6. Machine layout \"V\" (2 cylinder), \"W\" (3 cylinder) V V V and W configuration 7. Number of compressor stages 1+1 2 screw + 2 booster 3 3 8. Are special foundations required? No No No No 9. Cooling system Air (water option) Water Water Water cooling system - radiator / adiabatic 10. Belt or direct drive Belt Direct drive with high efficiency shaftless motor Low pressure compressor Direct Direct Booster compressor Belt Belt Integrated system","@ID":52}, "Congresses PET symposiums and lectures WikiPETia.info PET knowledge management system Pulse The monthly PET price index Worldwide PET magazine Social Media Connecting worldwide Events Fairs, open houses, on-site sessions ... No.4 2016 petpla.net D 51178; ISSN: 1438-9452 25.04.16 PETplanet is read inmore than 140 countries MAGAZINE FOR BOTTLERS AND BOTTLE-MAKERS IN THEAMERICAS,ASIA, EUROPEANDALLAROUND THE PLANET BEVERAGE +ingredients Page 10 MARKETsurvey Suppliers of resins / additives Page 27 petpla.net D51178; ISSN:1438-9452 No. 9 2016 PETplanet is read inmore than 140 countries MAGAZINE FOR BOTTLERS AND BOTTLE-MAKERS IN THEAMERICAS,ASIA, EUROPEANDALLAROUND THE PLANET 07.09.16 MARKETsurvey Bottle-to-bottle recycling plants Page 41 TheChinaRoadShow Page 12 bottlemaking Page 21 Page 52 PETplanet is read in more than 140 countries petpla.net News Daily PET business news Editours Worldwide editorial reporting The whole world of","@ID":78}, "90 PETplanet Insider Vol. 17 No. 10/16 petpla.net PETbottles Home + Personal Care Tanning oil with artistic detail Under the brand name “Byron Bay Australia”, a tanning oil with an artistic and handmade strap which passes through a dedicated opening in the bottle is available in the Netherlands. 200ml of the product, which contains various oils, fill a coloured PETG bottle with a screwed-on pump sprayer. A cap protects it against improper misuse and dirt. Customised self-adhesive labels on the front and back complete the packaging at POS. All-in-1 micellar cleansing water The brand “Garnier Skin Active” is selling an all-in-1 micellar cleansing water in a 400ml bottle. The product - in two layers - must be shaken before application to effectively remove even waterproof make-up and to gently clean and refresh. The clear bottle makes the two layers visible, and the product can be easily dispensed through a hinged lid clasp with a dosage opening. A front non-label-look and a back label, which has a silver sheen on the inside, reflect the lights on the store shelf. www.garnier.de Fairy with new size Procter & Gamble have revised the shape of the bottle and the filling capacity of the Fairy Super Concentrated series. Whereas the previous bottle contained 450ml and was stockier, the new bottle contains 500ml, is slimmer and at the same time taller. The mandarin and ginger blossom scented product enables exact dosage with built-in grip areas and a screwed-on hinged lid. Two self-adhesive labels complete the presentation at the POS. www.fairy.de","@ID":92}, "MARKET SURVEY 51 PETplanet Insider Vol. 17 No. 10/16 petpla.net Preforms Filling equipment Resins / additives Preform / stretch blow moulds Caps and closures Preform and single stage machinery Bottle-to-bottle recycling plants Compressors Closure systems Two stage SBM machinery Compressors Compressors - not often in the spotlight perhaps, yet a vitally important component of PET production, and with significant potential in energy-saving. Our annual market survey takes a closer look at these unsung heroes of the PET industry, featuring five compressor+ manufacturers and their product range: ABC Compressors, Boge Kompressoren GmbH & Co. KG, Gardner Denver Ltd, Kaeser Kompressoren SE and Siad Macchine Impianti. Although the publisher has made every effort to ensure that the information in this survey is up to date, no claims are made regarding completeness and accuracy. ABC Compressors Boge Kompressoren Pol. Ind. Azitain 6 20600 Eibar, Spain +34 943 820 400 www.abc-compressors.com Mr Ignacio Azcuna Product Manager +34 630 751 355 +34 943 820 235 [email protected] Otto Boge Str. 1-7 33739 Bielefeld, Germany +49 5206 601 0 www.boge.com Mr Klaus D. Korzeng Business Unit Manager - PET +49 5206 601 200 [email protected] Horizon Boge BS Line Boge FLEXPET System (BFP) Boge FLEXPET oil free system (BFPO) 5 8: BS 14-0 to BS 38-0 4: SRHV 170-10 to SRHV 470-10 2: K 8 BOOSTER & K 15 BOOSTER 425 - 6,000 1,150 - 3,000 (singles or unlimited multiples thereof) 94 - 274 (singles or multiples thereof) 58 - 116 (singles or multiples thereof) Oil free reciprocating compressor Oil free SO range - fixed speed or frequency controlled 10 bar screw compressors S or SLF range - fixed speed or frequency controlled oil-lubricated 10 bar screw compressors Oilfree SO range - fixed speed or frequency controlled 10 bar screw compressors Oil free booster range 40 bar fixed speed or frequency controlled SRHV oil-lubricated booster range 40 bar K BOOSTER oil free booster range 40 bar Oil free LP air with oil free HP air as fully frequency controlled modular system Separat prepressure compressor with HP base frame solution Separat prepressure compressor with HP base frame solution Oil free Oil free Class 0 Oil free Class 1 - optional Class 0 by BC converter Oil free Class 0 Oilfree Class 0 Oilfree Class 1 - optional Class 0 by BC converter Oil free Class 0 Oilfree Class 0 Oilfree Class 1 - optional Class 0 by BC converter Oil free Class 0 Horizontal opposed Individual system components custom designed system layout Skid mounted fully wired, piped and factory tested base frame solution Skid mounted fully wired, piped and factory tested base frame solution 3-4 LP two stages HP two stages - system four stages Two system stages Two system stages No No No No Water cooled Water cooled Air cooled or water cooled Air cooled or water cooled Direct drive Direct Belt or direct Belt or direct Belt Belt Direct Belt and direct Belt and direct direct","@ID":53}, "PETnews 6 PETplanet Insider Vol. 17 No. 10/16 petpla.net Indorama Ventures announces completion of JV agreement with Dhunseri Petrochem Indorama Ventures Public Company Limited (IVL), a global chemical producer, announced the completion of a joint venture (JV) in India of IVL’s PET Company, Micro Polypet Private Limited (MicroPet), with Dhunseri Petrochem Ltd. (Dhunseri). Simultaneously, IVL has acquired a 50% stake in Dhunseri’s PET Company in India, Dhunseri Petglobal Ltd. By combining the two companies as equal partners, the resulting total capacity of 700,000t/a will make the new JV the second largest in India. The potential for growth in the PET industry in India is significant given that per capita consumption of PET in India is currently at 0.6kg/a as compared to 2.6kg/a in China and 10.9kg/a in the USA. The JV will gain from synergies as being the sole producer of PET resin in Northern and Eastern India and with all its manufacturing sites being effectively integrated with third party PTA suppliers. IVL’s global market reach and high utilisation rates are expected to supplement the Indian city Haldia’s location benefit at Eastern India’s largest port while MicroPet enjoys a strong location advantage in the high-demand territory of North India. www.indoramaventures.com Meet PETplanet at China Brew China Beverage 2016 The China Brew China Beverage trade show, which has been held in Beijing on 11 occasions since 1995, will move to Shanghai New International Expo Center, Shanghai on October 2016. The liquid food manufacturing and packaging trade show, which runs from October 11–14, is expected to cover 100,000m2 with over 800 exhibitors.. Meet the PETplanet team in hall W2 booth 2Y445. www.chinabrew-beverage.com Amcor Rigid Plastics agrees to acquire assets of Sonoco’s Global Plastics blow moulding business Amcor Rigid Plastics has entered into an agreement to acquire the assets of Sonoco’s Global Plastic blow moulding business in North America. Sonoco manufactures custom rigid plastic bottles, jars, overcaps and closures for the food, beverage, pharmaceutical, health and beauty and personal care markets in seven plants located in the U.S. and Canada. “This acquisition will directly support our strategy to meet our customers’ growing needs,” said Mike Schmitt, Amcor Rigid Plastics president. “The combined assets and talents of Amcor Rigid Plastics and Sonoco will allow us to meet strategic customer growth objectives while expanding our extrusion and injection moulding assets and adding advanced decorating capabilities.” The acquisition is subject to regulatory approvals. Until the transaction is closed, Amcor Rigid Plastics and Sonoco will continue to operate as two separate companies. www.amcor.com ALPS machines leak test more than 25 billion ","@ID":8}, "CAPPING / CLOSURES 44 PETplanet Insider Vol. 17 No. 10/16 petpla.net 4.7 Economic Guidelines There are so many different cavitation systems in production today, with different vintage machines and a variety of mould and closure designs, that it is very difficult to give concrete economic advice for just any configuration. We will therefore only spell out several key components that are important to closure production and point out the importance of cycle time on profitability. The first data sheet compiles capital costs as a percentage of the total. The numbers are meant for a high-end machine with closed-loop injection parameter controls, fast movements, and a carefully designed and optimised mould with 64 cavities. Similar data can be compiled for a CM machine. Injection machine costs 29.2% Chiller 2.1% Closure conveyor 0.3% Resin vacuum loader and mixer 0.3% Air compressor 0.5% Wiring piping start-up machine 1.6% Import tax machine 1.7% Total costs machine 35.7% Injection mould costs 52.9% Temperature controller costs 2.3% Additional equipment costs 0.8% Additional logo inserts 0.0% Spare parts 2.4% Installation costs – mould 1.6% Import tax mould 3.0% Total cost mould 63.1% The most striking observation may be that the machine cost is only 29.2% of the total, whereas the mould weighs in with 52.9%, a reflection of the highly advanced mould technology available today. It is also an indication of how important it is for any prospective processor to cooperate with knowledgeable and skilled mould makers. Adding these two percentages we can see that auxiliaries make up about 18%. If a dehumidification system is required, this would have to be added to the list. Next we look at operating expenses. We have broken them out for three different cycle times: 5, 7, and 9s. Raw materials including colourant contribute between 60% and 70% to the overall cost. It also becomes clear that running a faster cycle in turn reduces the cost impacts of labor, energy, and especially amortisation. This has of course a great impact on profitability. Although sales prices are subject to regional and other differences, we have charted a graph comparing them for a typical European moulder. The increase in cycle time from 5 to 9s results in a cost increase of about 15%. This does not seem Typical operation cost schedule for injection moulded caps to have a drastic impact. However, assuming that the moulder can sell all caps in a year and paid the same amount for the equipment, the resulting difference in profit per year paints a different picture. The increase in cycle time from 5 to 9s results in a drop of profit of over 60%, increasing simple payback time from 1.4 to 3.9 years! In essence, a fast IM machine with precise controls and a well-designed mould is paramount to make money in the closure business. Operating Costs 5s cycle 7s cycle 9s cycle Cost of raw material per kilogram $1.30 $1.30 $1.30 Colour Red Red Red Percentage of colourant in raw material 1% 1% 1% Cost of colourant per kilogram $14 $14 $14 Number of caps per box 4,000 4,000 4,000 Running costs for the factory per 1,000 caps 0.8% 0.8% 0.7% Cost of 1 operator per 4 machines per year 1.8% 2.3% 2.8% Packaging material per box 5.2% 4.9% 4.6% Energy costs 4.3% 5.6% 6.8% Rejects 0.7% 0.7% 0.6% Repair costs per year 0.5% 0.6% 0.7% Total costs of raw material 63.8% 59.6% 56.0% Total costs of colourant 6.7% 6.3% 5.9% Total direct costs per year 83.7% 80.7% 78.1% Sales/admin costs (6% of production costs) 5.0% 4.8% 4.7% Building and land costs 1.5% 1.9% 2.3% Interest on working capital 0.8% 0.8% 0.8% Amortisation of mould 5.8% 7.6% 9.2% Amortisation of machine 3.1% 4.1% 4.9% Total indirect costs per year 16.3% 19.3% 21.9% Total cost 100.0% 100.0% 100.0%","@ID":46}, "MOULD MAKING 21 PETplanet Insider Vol. 17 No. 10/16 petpla.net The perfect image Precision within seconds. Closure cap decoration with rotary pad printing machines. www.tampoprint.de Visit us at the exhibitions in Germany: K-2016, Düsseldorf, Hall 4, Stand 4C46 BrauBeviale 2016, Nuremberg, Hall 4, Stand 4-617 View into Yizumi’s assembly hall facturing locations abroad: a technical centre in Germany and additional service units in key sales markets. A strategy paper on customer service prioritises comprehensive customer care, with commitments to standards such as delivery of spare parts within 24 hours; preventative measures and maintenance on location; and in-depth training of the machine users. We drove to the nearby manufacturing facility in Wusha, which has a workshop that is a bit bigger than the one in Gaoli. This location hosts development and construction work as well as the sales of the injection moulding machines. A gigantic construction hall is home to machine after machine; part of the building is dedicated to fully electrical machines. “By the end of 2016 we forecast that we will have sold 4,500 machines, with 3% of this total for PET applications, across all our divisions,” she says. “Our forecast turnover is US$ 200m. By the end of the year we are forecasting that 20% of our PET injection moulding machines will be sent for export, mainly to Asia and the Middle East area.” I asked Director & Deputy General Manager James Zhang to outline expected developments in Yizumi machines. “We are continuing to improve the efficiency of manufacturing our PET preform moulds and high speed PET preform injection systems, and are developing some new projects this year,” Zhang replies. “Our main project is a middle speed PET preform injection moulding system for the manufacturing of 15g PET preforms with 56 cavity moulds and a 10-second cycle time. This system is very competitive when compared with normal speed injection systems. We are also developing a range of different hot runner moulds for PET. We can make between 2 and 96 cavity moulds for different PET preform types, which offer an excellent performance with a short delivery time.” www.yizumi.com.hk Karen Yu with Kay Barton in front of a 32 cavities preform machine","@ID":23}, "CAPPING / CLOSURES 43 PETplanet Insider Vol. 17 The lower forming pressures used also create less residual stress in the finished cap. Cycle times as low as 3.2s are possible. A CM machine may also be equipped to form a liner made from a different material as a second step. This makes them ideal for closures for hot-fill bottles. 4.6.3 Comparison of IM–CM The main differences between the two methods stem from the fact that in IM the entire tool has to move for each cycle whereas in CM individual cavaties move. This and other differences make CM more energy efficient: Less mass is moving for the production of each cap Material temperatures are lower A continuously running turret requires less energy than the discontinuous operation of an IM machine Compression pressure is lower than injection pressure CM also does not need sophisticated systems to center two mould halves, but instead relies on relatively simple guide bushings. Because it does not need the plates and complex hot runner systems used in IM moulds, CM tools are generally less expensive, especially when the capital cost is compared with the output per year. Another advantage is that the lack of hot runner channels speeds up colour changes. CM is somewhat limited in tool complexity and is mainly used for standard beverage and hot-fill caps. CM tools do not allow slitting the caps right inside the mould, and these slits must therefore be added in a secondary operation. Many processors try to minimise these, and therefore a case can be made for either proFigure 4.37 Compression machines like this Sacmi CCM011 are an attractive alternative to IM. (picture courtesy of Sacmi) cess. An ample supply of spare parts and knowledgeable technicians that can come at short notice may be the deciding factors when machinery buyers have trouble making a decision between the two processes. PET Line #GermanBlingBling #PETLine We do more. CHINA BREW CHINA BEVERAGE 2016 Shanghai New Intern. Expo Center 11 – 14 October, Hall B, Booth 2200","@ID":45}, "LABELLING 56 PETplanet Insider Vol. 17 No. 10/16 petpla.net Labelling machines with integrated servo technology No contact, no wear Modern labelling machines with integrated servo technology offer complete flexibility for a precise container dress. Markus Müller, Heuft Product Manager Labelling, explains the advantages in an interview with Hilmar Wagner, Editor Public Relations. Mr Müller, where and why is servo technology used in labelling machines? Müller: “State-of-the-art, wraparound labellers have a servo-controlled toothed belt so that the rotating speed of the containers can be exactly controlled and finely adjusted. Modern self-adhesive and wet glue labellers are equipped with servocontrolled rotating platforms in order to apply labels perfectly onto up to 72,000 bottles or jars per hour. They are responsible for the fine alignment of the containers with millimetre accuracy. Servo technology is also in the dispensing head of our self-adhesive labelling machines. It distributes the labels from the roll precisely. Generally speaking, this technology permits a flexible and accurate positioning of the labels. In addition, servos are very efficient and economical especially when they manage without gears and have lifetime lubricated bearings – as do the Heuft machines. This makes them practically maintenance-free and non-wearing.” Are there other advantages? Müller: “Yes, servo labellers show their true strengths - above all - along filling lines with a great variety of brands, particularly in the premium sector: specific container diameters require specific rotating cams. The cam of a modern servo machine is changed fully automatically, whereas in the past cam segments had to undergo an elaborate mechanical replacement. Consequently program changes function within a very short time at the push of a button, and considerably less change parts are needed for this. The marketing aspect is also an important argument: you never know what the Marketing Department will devise next – perhaps the introduction of embossed bottles or containers with the no label look plus special windows in the label where it is necessary to align using different characteristics. A tremendous amount of flexibility is required for this. Those who have a machine such as the Heuft Tornado S flex, which is already prepared for all eventualities from the outset, are at an advantage.” Do you have an example? Müller: “The mechanical cam had to be changed completely in the past, and all the brands, including those which already existed, had to be commissioned again from scratch in order to carry out the precise application of a newly introduced wrap-around label to the bottle neck. This requires a lot of time, energy and money. In contrast with servo technology only the one, newly added brand has to be extended and the cam programmed accordingly. This keeps the time and effort involved within limits.” Let’s get back to the fine alignment of the containers: How does this work? Müller: “Using optical detection procedures and servo technology: typical container characteristics such Markus Müller, Heuft Product Manager Labelling","@ID":58}, "MATERIAL / RECYCLING 11 PETplanet Insider Vol. 17 No. 10/16 petpla.net 11 MATERIAL / RECYCLING and government ministries. It has the exclusive right to issue the EU ecolabels in Germany. The RAL quality assurance association is active in the development phase in Germany, but having established itself in the German market, wishes to send a strong signal internationally. As the German market is very open and lots of old stock is transformed, it is important to RAL to think in the direction of a circular economy to save resources and promote the reuse of material, in addition to the regulatory EU Directive 282/2008. The “Gütegemeinschaft Wertstoffkette PET-Getränkeverpackungen e.V.” RAL quality assurance association currently has 28 members, mainly consisting of PET recyclers, preform manufacturers and bottle-fillers for mineral water and juices. www.wertstoff-pet.de Fig.1. Ecological impact that is used in designing bottles K 2016, October 19-26, 2016 | Düsseldorf | Germany CIBUS TEC, October 25-28 | Parma | Italy SITEVINITECH, October 27-29 | Mendoza | Argentina Pack Expo, November 6-9 | Chicago | USA GULFOOD, November 7-9 | Dubai | UAE BRAU BEVIALE, November 8-10 | Nüremberg | Germany EMBALLAGE, November 14-14 | Paris | France PLASTIC & RUBBER, November 16-19 | Jakarta | Indonesia DRINK TECHNOLOGY INDIA. December 15-17 | Bombay | India With Sacmi, the beverage specialists are always at your side. With our unbeatable technological know-how and continuous research we are creating new containers and closures designed to ensure outstanding performance. The new IPS injection system for preforms, the CCM compression press for caps and the quality control systems fully designed and built by Sacmi, allows for large-scale production with considerable advantages in terms of efficiency and flexibility. The outcome? Reduced plastic volumes, less energy consumption and lower running costs.All in a bottle: the one you’ll soon be making. 0% 20% 40% 60% 80% 100% 2,5 2,0 1,5 1,0 0,5 0,0 Implementation weight reduction/recyclate usage kg CO 2 -equivalents","@ID":13}, "TRADE SHOW PREVIEW 83 PETplanet Insider Vol. 17 No. 10/16 petpla.net mould technology that facilitates the filling of very thin wall sections. X-Mould is intended to give designers the power to design a 500ml bottle preform weighing as little as 7.2g that presents no production issues - and which can be processed on existing equipment. A new shine on old moulds, with Xcore With Xcore, it intends to offer a new metalising service for existing injection mould cores that will provide a cost-effective way of modifying preform dimensions, down-gauging containers, and advancing materials saving. Xcore will be an alternative and lower-cost solution to corechange programs for preform light-weighting within the range of 0.2-0.5g, when an investment in a completely new set of cores is hard to justify. Sipa calculates that on, for example, a 96-cavity tool, metallising cores to cut wall thickness down from 2.0mm to 1.9mm, achieving a weight reduction from 11.0g down to 10.7g, would pay for itself 2.6 times more quickly than changing the cores. A new generation of hot halves Hot halves have been given a thorough revision in the latest generation - the third - of Sipa injection moulds for PET preforms. New technical features include the incorporation of Xflow technology to produce a considerable enhancement in flow throughout the mould, creating a better balance and reducing pressure drops. Xflow makes use of the very latest concepts in polymer fluid dynamics to allow Sipa engineers to develop new design solutions that take greater account of melt rheology and so arrive at flow balances in the mould that are almost impossible to reach with traditional calculation systems. Third generation nozzles have an improved temperature profile and reduced pressure drop. Ease of maintenance has been improved, since it is now easier to remove nozzle inserts and install new ones; in addition, the performance of the nozzle tip over its guaranteed five million cycle lifetime has been improved. The new hot halves are compatible with standard cold halves and equipment used in the PET preform production sector. They use the same mechanical and electrical interfaces and same hot runner thickness, providing extra flexibility in use. www.sipa.it ATTNDRIES GENTLY AT A CONSTANT DEW POINT LUXOR A 80-2400 Now with ATTN ATTN brings more security in your drying processes. The automatic temperature and dew-point leveling is now available for all dryers in the Advanced (80–2400 m³/h) series. Setting a consistent dewpoint prevents the over-drying of granulate. ATTN together with ETA plus® provides a useful system, that protects your material, ensures quality and saves you energy. motan-colortronic gmbh [email protected] www.motan-colortronic.com Please visit us Hall 9 Stand C64","@ID":85}, "MOULD MAKING 16 PETplanet Insider Vol. 17 No. 10/16 petpla.net SPONSORS The China Road Show Customer services for moulds By Kay Barton August 4, 2016, Otto Hofstetter Shenzhen Ltd. We met: Mr Johnson Li, Operating Manager As part of our China Road Show we visited Swiss mouldmaker Otto Hofstetter AG’s (OHAG) Service Centre in the city of Shenzhen in southern China, where we met Mr Johnson Li, the company’s Operating Manager. The customer base served by the office in Shenzhen primarily uses tools with 96 and 128 cavities, and the establishment of the service centre has made it possible for OHAG to respond to customer enquiries at short notice and, in addition, to provide technical service and support, spare parts, and general overhaul of moulds. Local preparation and maintenance of moulds has enabled a big reduction in waiting times for Chinese customers and guarantees a level of service equivalent to that provided to European users of OHAG equipment, whether from the workshop or on-site at customers’ premises, if required. A full range of spare parts is held on site at the Shenzhen facility or can be delivered from the global headquarters in Switzerland at short notice, usually by air freight. The Chinese Service Engineers were carefully trained to ensure that they attend to their tasks according to “In addition to China, including Hong Kong, we serve South Korea and parts of South East Asia from here,” Li explains. The period in the winter months before the Chinese New Year, which is the least busy time of the year for the drinks packaging industry, is when most of the servicing work takes place; it is in those weeks that the processors have the time available to maintain their injection machines. “In addition to the technical side of things, our activities include the usual work in the areas of communication and sales, which are scheduled in agreement with our headquarters in Switzerland.” Before Johnson Li joined the China operations of OHAG, he worked for Colgate Guangzhou, specialising in the injection moulding and blow moulding of toothpaste tubes. www.otto-hofstetter.swiss OHAG’s Operating Manager Johnson Li studying PETplanet Insider The local engineers were trained to their tasks according to the guidelines and quality standards of the OHAG HQ. the guidelines and quality standards of the HQ. In the initial phase, Swiss specialists visited Shenzhen and instructed their colleagues on the job. To deepen their knowledge, Chinese employees came to Uznach, Switzerland for individual training to suit the specific requirements of their market. Even now they can fall back on their colleagues at the Hofstetter HQ at any time. However minor an uncertainty may appear to be, they are quickly provided with the necessary answers and support from the appropriate competencies.","@ID":18}, "TRADE SHOW PREVIEW 72 PETplanet Insider Vol. 17 No. 10/16 petpla.net Conair Hall 10 Booth J59 R-Pro conveying system The patent-pending R-Pro (Resin-Protection) densephase vacuum-conveying system developed by Conair to minimise pellet fracturing, “angel hair” and equipment wear caused by conventional dilute-phase conveying will make its first appearance at a European tradeshow when K 2016 begins. Other innovations on display will include a new FLX-128 Plus conveying control, which can now be set up to operate the R-Pro system, a new Mobile Drying/Conveying (MDC) system with standard colour touchscreen control interface, and several examples of equipment from Conair’s auxiliaries. The R-Pro system is a new approach to vacuum conveying. The R-Pro system is said to reduce the severity of typical problems such as pellets smear against the sides of aluminium tubing, deforming and creating long streamers or “angel hair” that can clog the system at high speeds. Comprised mainly of standard vacuum-conveying components, R-Pro results in slower flow and less resin damage without limiting throughput. It is claimed to be cost-competitive and can be retrofitted to existing systems. The new FLX-128 Plus system can not only control R-Pro systems, but also integrates Conair’s newest lineproofing systems. The FLX-128 Plus flexible control system utilises a combination of centralised I/O and expansion modules, interconnected via industrial Ethernet to provide control of up to 128 receivers, 40 pumps (plus 2 back-up pumps) and 256 source valves. For the first time anywhere, a mobile drying/conveying system (MDCW) will be shown with Conair’s newest DC-A touchscreen control interface. The MDCW combines a Carousel Plus Dryer with a conveying blower, dust collector and direct-feed vacuum receiver to convey dried material to the throat of a processing machine – all assembled on a safe, convenient wheeled cart. www.conairgroup.com MARKET BENCHMARK DOUBLE ACTING DIRECT COUPLED MOTOR HEAT RECOVERY SYSTEM HORIZONTAL OPPOSED www.abc-compressors.com BRAU BEVIALE - Nuremberg 8-10 November EMBALLAGE - Paris 14-17 November CBB - Shanghai 11-14 October","@ID":74}, "LABELLING 57 PETplanet Insider Vol. 17 No. 10/16 petpla.net as swing tops, embossing and even hairline mould seams are identified by camera and used as reference points for the adjustment. The servos below the platforms then rotate and orientate the bottles so precisely that the labels always remain stuck exactly in the positions intended for them. This practically excludes false positioning. The same applies to bubbles and folds which can occur e.g. when glueing over the mould seam.” Does this servo-controlled adjustment have other positive effects? Müller: “Definitely! Orientation marks are no longer necessary; this makes the containers cheaper. The risk of material breakage and wear are reduced at the same time. Because force is exerted during a conventional mechanical adjustment: special fingers engage with the rotating bottles. This can damage them. The fingers themselves wear out eventually. By comparison everything works completely without contact using servo technology. And where there is no contact, there is no wear.” Even the servos themselves, as mentioned above, are practically non-wearing. But what happens should one fail? Müller: “Replacing the motors is very easy. Any mechanic can deal with this in no time at all without having to call an electrician. The new servo is then programmed fully automatically at the machine afterwards.” Is it possible to combine several labelling procedures in one machine using servo technology? Müller: “Yes, we have recently installed such a flexible labeller for an important Russian fruit juice and baby food producer. The machines of the Heuft Tornado flex series apply self-adhesive front and back labels to bottles and tamper evident labels to food jars from above first. Their safety tabs are then folded down and rolled on neatly. Wrap-around labels are applied afterwards aligned for this purpose. This functions absolutely precisely because the servos always know the exact position of the containers as soon as the lid labels are present. In addition they ensure a fast change to another type of packaging, because completely different rotating cams are required for the wraparound labelling of baby food jars and the self-adhesive labelling of juice bottles. This changeover is possible at the push of a button thanks to the servo technology!” Mr Müller, thank you for talking to us! www.heuft.com","@ID":59}, "imprint EDITORIAL PUBLISHER Alexander Büchler, Managing Director HEAD OFFICE heidelberg business media GmbH Bunsenstr. 14 69115 Heidelberg, Germany phone: +49 6221-65108-0 fax: +49 6221-65108-28 [email protected] EDITORIAL Kay Barton Heike Fischer Gabriele Kosmehl Michael Maruschke Ruari McCallion Waldemar Schmitke Wolfgang von Schröter Anthony Withers WikiPETia.info Doris Fischer [email protected] MEDIA CONSULTANTS Martina Hirschmann [email protected] Johann Lange-Brock [email protected] phone: +49 6221-65108-0 fax: +49 6221-65108-28 LAYOUT AND PREPRESS EXPRIM Werbeagentur Matthias Gaumann | www.exprim.de READER SERVICES Till Kretner [email protected] PRINT Chroma Druck & Verlag GmbH Werkstr. 25 67354 Römerberg Germany WWW www.hbmedia.net | petpla.net PETplanet Insider ISSN 1438-9459 is published 10 times a year. This publication is sent to qualified subscribers (1-year subscription 149 EUR, 2-year subscription 289 EUR, Young professionals’ subscription 99 EUR. Magazines will be dispatched to you by airmail). Not to be reproduced in any form without permission from the publisher. Note: The fact that product names may not be identified as trademarks is not an indication that such names are not registered trademarks. 3 PETplanet Insider Vol. 17 No. 10/16 petpla.net Dear friends of PETplanet Insider, The K fair is just around the corner. It is of interest to everyone involved in the world of plastics, and thus also to PET, which leads us smoothly to the world of beverages. Whilst many areas of the plastic industry are growing, the supplier landscape for PET bottle fillers is stagnating at a high level. There are numerous reasons for this. On the one hand, in countries such as China there is serious overcapacity, causing sales of machines and plants to collapse. Europe has been stagnant for years, with any investment going towards replacing machinery. South America seems to swing constantly from feast to famine. Investments in North America are going primarily to large water bottlers, who dominate the mass market. India struggles to realise its full potential, whilst in developing African countries, investment hotspots are few and far between. Small wonder then, that all of us involved in editing our K-fair preview are finding press releases dominated by the theme of evolution rather than revolution. The beverage industry overall may be showing signs of stagnation, but the beer sector is proving more robust. There, the craft beer movement has given birth to completely new companies, all of which need to be supplied with equipment. The classic providers of breweries and filling plants have tended to target large multi-nationals and now have a problem providing this fast-growing sector with technologically and financially appropriate equipment. The prices of good technology are such that the typical ROI is perhaps 15 years or maybe more. So the traditional suppliers are falling over themselves to offer better value equipment with perhaps simpler technology, but with an ROI of only three years. Winning these customers back when they have grown becomes very difficult. Thus slowly and discreetly there emerges a new supplier market for the beverage industry, and in the water and soft drink industry we will experience the same thing as has happened with beer. Established suppliers could also miss a trend here - which will make the large plant business difficult later on. So let’s keep our eyes and ears open and watch how exhibitors at K fair try to meet the demands of these new and expanding trends. Yours, Alexander Büchler","@ID":5}, "BOTTLES 91 PETplanet Insider Vol. 17 No. 10/16 petpla.net Fragrance pearls in a conical bottle 160g of fragrance pearls with various fragrance varieties of the brand “fresh air” are available in the Netherlands in an upright, conical and clear bottle. A membrane to be removed before first usage is sealed under the screw cap with openings and a foam pad to release the fragrance. The cap is then screwed on again, and the room will be scented for a certain period of time. A label attached to the neck of the bottle explains its handling and usage. Quick-dry blow-drying spray The drugstore discounter dm is selling a 200ml quickdry blow-drying spray under the private label Balea, which makes hair dry quicker while blow drying and makes it easier to brush. The product consists of two layers which must be stirred before usage by shaking the bottle. A manual, light pink coloured pump dispenser is screwed onto the transparent bottle, protected by a cap of the same colour against involuntary operation or damage. www.dm.de processing+filling+packaging+ logistics In conjunction with: Forum organizer: International trade fair for the beverage and liquid food industry A MEMBER OF drinktec worldwide featuring dairy processing REGISTER NOW! drinktechnology-india.com/tickets","@ID":93}, "INSPECTION 28 PETplanet Insider Vol. 17 No. 10/16 petpla.net In addition to reducing process variation and ensuring uniform bottle production, the Agr automated control system provides a critical stream of information that supports a proactive approach to blowmoulder maintenance. Sanpellegrino technicians look at data captured by the Process Pilot to uncover process trends over several days of production. Deviations can signal potential trouble spots, indicating, for example, the need for maintenance on a particular blowing station or problems developing in a mould. “This helps us drive maintenance where it’s needed,” Chimetto says. There are now five Agr systems managing material distribution on Nestlé PET production lines throughout Italy. Lightweighting, Round 1 The Process Pilot has allowed Sanpellegrino to move its lightweighting plans forward with confidence, knowing that in the new bottles the right amount of material will wind up in the right place. Lightweighting has long been a Sanpellegrino goal, not only for savings in material costs, but also for advancing the corporate sustainability programme. At the same time, “what is right for the consumer is not automatically the lowest weight,” Chimetto remarks. It is critical for the customer to have the same repeated experience grasping, opening, and handling the bottle in order to protect the brand and retain market share. The first lightweighting project designated for the Sanpellegrino/Agr collaboration was an effort targeting a 22% reduction in total bottle weight - a massive opportunity for material cost savings. The focus was a halfliter round Levissima bottle produced on a Sidel Series II Combi blowmoulder with blowing and filling integrated in one system. Despite the blowmoulder’s stable operating history, at production speeds approaching 40,000bph, this “was not a straight-forward task,” Chimetto recalls. The processing window narrows significantly on lighter bottles when they are produced on faster machines. “We need to strike the right balance between performance and weight. There is no margin left - every bottle must be blown properly,” he comments. The impact of poor bottle quality shows up immediately in downstream handling. Bottles that are not properly blown can fall over, interrupting or stopping operations in the capper and labeller, wasting valuable production time. Bottles that are not strong enough to support the vertical load create additional stress in the labeling, while, if the neck has “suffered” from excessive heating, the capping functions are also badly impacted. From a marketing perspective, the consequences are just as serious: substandard bottles that lean create a very poor customer experience. Sampling bottle quality is not the answer in the high-production environment. According to Chimetto, “You must do either a very robust and aggressive sampling effort, which is marginally effective and labor intensive, as by the time you do the sampling and measurement, the bottles are already in the capper and labeller. Or you equip the blowmolder with an automated measurement and management system such as the Process Pilot. If you do not do this, you take risks that either result in a drop in efficiency or customer complaints, or both.” Together Sanpellegrino and Agr refined the parameters for the halfliter bottle, bringing it into full-scale production in 2010. “With the Process Pilot installed on this line, managing the process, we were able to reduce the weight of our half-liter bottle to 9.5g while maintaining a very stable process,” notes the packaging manager. Lightweighting, Round 2 Sanpellegrino recently took delivery of three additional Process Pilots. One of these will be mated with the new Sidel Matrix Combi blowing/filling/capping systems as the company upgrades older lines originally configured with independent blowmoulders, airveyors and fillers. As part of the corporate-wide move toward standardised production lines, the Combi platform was attractive for its smaller footprint, gentler handling of bottles before filling, and eliminating the need for airveyors. One of the first applications for the new equipment line-up is removing further material from a 2l square bottle, reducing the weight down below 28g. Given Sanpellegrino’s vast bottle volumes, the weight savings promises a significant return on investment, but, once again, there are a few production issues to resolve. “A square bottle is very difficult to produce. Unfortunately, they do not make a square preform,” Chimetto quips. It is not only the stretching of the round preform into a square shape that presents a challenge. Attaining exacting standards of material distribution is critical for bottle performance and the customer experience. Weighing two kilos when filled, the bottle has to be convenient and reliable in consumer use. “Just to lift a bottle of this size requires some squeeze to ensure a proper grip,” he explains. “What happens when the cap is removed? We must take into consideration the feel, Nestlé Waters Levissima plant","@ID":30}, "LABELLING 67 PETplanet Insider Vol. 17 of the print heads and ink flushing are automated to keep downtimes to a minimum, and the ink tanks are easy to reach and are refillable during printing. The printing module adjusts automatically to the height of the beverage closures. Hapa’s “redcube plus” delivers direct digital print on-demand in the highest print quality. New opportunities The flexibility of direct digital printing on beverage closures offers companies new opportunities to increase brand awareness. Digital print in general is market-proven to realise efficient and effective communication. It can be applied to other applications such as rigid plastic boxes, metallic crown corks, or any other flatsurfaced component, tasks the “redcube plus” is able to easily fulfill. Products can be individualised as late as possible in the production process, opening chances for personalisation of products and for new or seasonal launches and campaigns. Swiss partnership Behind the CLDP line’s development stands an exciting partnership between two Swiss market leaders: IMD Ltd., producers of inspection and handling systems, and Hapa. The partners, located within close proximity of each other, offer customers the advantage of being able to sit with representatives of each company to tailor solutions toward capturing new marketing parameters. www.hapa.ch www.imdvista.ch","@ID":69}, "MATERIAL / RECYCLING 10 PETplanet Insider Vol. 17 No. 10/16 petpla.net A quality association for environmentally friendly PET bottles A circle of PET life - displaying the whole supply chain, part 1 In the non-alcoholic soft drinks packaging sector, the PET bottle has achieved a high level of market acceptance, with a more than 80% market share in Germany. This success brings with it a huge responsibility for both industry and consumers: if a product is so well received in the market, it must be produced in a process that saves resources and is environmentally friendly and climate friendly. Although the recovery rate of used PET bottles in Germany is high (99.9%) thanks to a well functioning deposit system, there are various countries where deposit and collection systems do not work well yet or have not yet established themselves. This often results in mountains of rubbish. Primarily via rivers, these reach the oceans and threaten the global ecosystem. The “Gütegemeinschaft Wertstoffkette PET-Getränkeverpackungen e.V.” RAL quality assurance association in Germany is an organisation aimed at preventing this litter and producing more economically using fewer resources. Production processes and the product are monitored with a view to optimising the PET bottle’s supply chain. This improvement not only has an impact on resource efficiency, positive cost savings and climate protection during production, but also functions as a quality award to attract consumers. The association was founded to promote the further evolution of PET drinks bottles with respect to ecological factors, i.e. to close the resource chain for PET packaging material and therefore increase the rPET content in drinks bottles. We met Andreas Normann, Head of Sales at Hansa Heeman AG and Chair of the “Gütegemeinschaft Wertstoffkette PET-Getränkeverpackungen e.V.” RAL quality assurance association at the company’s location in Bruchsal. The Hansa-Heemann AG Group fills approximately 2bn bottles a year. The plant in Bruchsal is equipped with the latest machinery from KHS and Sidel. As expected with these quantities, Hansa Heemann AG manufactures its preforms on site. Andreas Normann explains to us that HansaHeeman encouraged the blocking of machines and/or merger of individual production steps at the Bruchsal location to be able to guarantee these large sales volumes on the market. Andreas Normann reports that the idea for the RAL quality assurance association had already emerged in 2011/12. The basic idea that drove the association was improving the PET bottle’s life cycle assessment. The association defined standardised parameters and measurements for the production of PET bottles to guarantee product safety. There are regulations for bottle-fillers, preform manufacturers and recyclers. According to Andreas Normann, these regulations have to be evaluated, supplemented and expanded from time to time. They include, for example, instructions for recyclate manufacturing: DIN standards and EFSA regulations are prerequisites, and this also applies to preform and bottle manufacturing. All regulations are transparently viewable on the association’s website. One important factor to significantly improve the PET bottle’s life cycle assessment is the use of rPET. The Ifeu Institute for Energy and Environmental Research Heidelberg, Germany has documented this in many scientiic studies. For this reason, some companies especially emphasise rPET use. The quality association together with the Institute has developed a model for the ecological impact that is used in designing bottles (see fig.1). The RAL quality assurance association is a working group of executive nature: the applicants are subject to rules. There is a quality committee that assesses the anonymised data and further develops processes. If individual parameters are not met during the inspection, the member is given a second chance to improve, and a deadline is set. If the desired result has still not been achieved, this may lead to the certification mark being withdrawn. This process ensures that there is compliance with the statutory minimum requirements and standards at the member companies. The RAL (German Institute for Quality Assurance and Certification) is a well respected institute in Germany that enjoys the trust and confidence of consumer associations, the industry Andreas Normann, Head of Sales at Hansa-Heeman and Chair of the “Gütegemeinschaft Wertstoffkette PET- Getränkeverpackungen e.V.” RAL quality asurance association at the company’s location in Bruchsal, Germany. By Heik Fischer","@ID":12}, "LABELLING 64 PETplanet Insider Vol. 17 No. 10/16 petpla.net Poland’s most popular mineral water gains a new labeller Labelled as required When Poland’s biggest brand of mineral water was looking for a multifunctional labelling machine which is easy to operate and meets all quality criteria, they decided on the Innoket Neo from the KHS Group. A total of three machines in this new series are in service at Nałęczów in Poland. One of the main reasons for the bottler investing in this particular piece of equipment was its free-standing labelling station concept which is claimed to give the operator optimum access and a high level of safety. Cisowianka is a natural mineral water which is filled directly at source not far from the Polish town of Nałęczów near Lublin. The region’s extraordinary microclimate makes it a famous spa, its excellent air quality primarily valued by people with cardiovascular disorders who come here to take a cure. The filler of this special water, ZL Nałęczów Zdrój, runs one of the most technically modern mineral water bottling plants in Europe. Founded in 1979 in Drzewce very close to Nałęczów, it has been drawing its water from a source about 100m below the ground for over 35 years. The company is proud of its high standards of quality and safety; it does not change the natural features of its water in any way. Outside Poland premium brand Perlage is the best-known Nałęczów water, filled into dark-blue bottles and exported to restaurateurs in many countries in Europe, America and Asia. One of the special features of the equipment is the application of a selfadhesive shoulder label to the bottles. Downtimes during reel changeovers or faults are prevented by redundant labelling units, thus ensuring machine availability. For maximum bottle protection the machine does without the otherwise usual, abrupt bottle flowgate; instead, the bottle flow is very gently moved through a feed screw which is driven by servomotors. The customer uses the Innoket Neo to label Poland’s leading Cisowianka mineral water brand in three varieties: still, medium and sparkling. On average 450,000 bottles are processed per day – which is well below the machine’s maximum output, as Kamil Banaśkiewicz, technical project coordinator at ZL Nałęczów Zdrój, emphasises: “We fill several hundred million bottles per year here at our plant, with our KHS labeller one of the most reliable machines in our production shop.” The machine’s use for these three concrete variants of mineral water is based on the specific requirements of the connected lines: the container material, the number of labels per bottle and the efficiency. The Innoket Neo series is of course also suitable for any other labelling task and filling line, so that the customer is currently talking about a further project. The variety of containers processed by the Polish bottler is infinitely larger; throughout its entire portfolio the sizes of container vary from 0.3 to 1.5l. There are all types of glass and PET container and can, from the classic PET bottle to the premium glass bottle. It is thus obvious why great attention is paid to flexibility with each new investment in plant engineering. Format changeovers made easy “For us, both the quality at KHS and the after-sales service were of equal importance,” says Banaśkiewicz. The KHS Innoket Neo also had the client convinced with its clever details. For format changeoLabels waiting for use Combination of cold glue and self-adhesive labelling When it came to packaging its natural commodity, the company did not want to make do with the usual standards and began looking for a specific system. It soon found that the KHS Innoket Neo series best satisfied its labelling requirements. Available in six different sizes, it caters for a number of different labelling processes and capacity ranges. In Nałęczów the customer opted for a combination of cold glue and self-adhesive labelling, with the basic dressing consisting of paper labels for the front and back of the PET bottles. On this count the Innoket Neo is convincing with its rotating glue pallets which, together with other innovations, are intended to permit long labelling station maintenance intervals of up to 20,000 hours. This is equivalent to three to four years in three-shift operation.","@ID":66}, "RECORD BREAKING SPEED IN CLOSURE PRODUCTION The world’s fastest plastic closure folding and slitting machine capable of more than 60 parts/second, designed and built using Swiss precision technology. Slitting tamper evident bands is more efficient and accurate than molding bridges in the mold Multiple injection molds processed on one folding/slitting machine possible Higher efficiency and faster cycle times Lower energy consumption on a small footprint PackSys Global – a cut above the rest, easily meeting the performance demands of the beverage industry. PackSys Global AG T +41 55 253 3700 [email protected] @packsysglobal PackSys Global designs and builds full lines for manufacturing: Laminate, extruded and aluminum tubes Plastic beverage caps Monobloc aerosol cans PackSys Global also provides solutions for decorating aluminum screw caps. PackSys Global now comprises three other Swiss companies: Combitool Solutions, Madag Printing Systems and Texa Packaging. A Member of Brückner Group www.packsysglobal.com","@ID":25}, "INSPECTION 29 PETplanet Insider Vol. 17 No. 10/16 petpla.net Your recycling needs. Our grinding solutions. +49 2154-94390 [email protected] triaplastics.de Hall 09 / Booth E05 the handling, and any deformation as the bottle is tipped and contents poured. If the material is not properly distributed, the bottle will bend.” The material reduction requires extra caution as the margin for error shrinks and the remaining material must be in exactly the right places for the bottle to perform properly. “The Process Pilot system makes it possible for us to monitor the material distribution to a very precise degree,” Chimetto comments, “and with the automated controls, it maintains the distribution throughout the production run. The total cost reduction potential provided by Agr’s Process Pilot in labor, energy, scrap and material looks to provide for rapid payback and offers a competitive return on investment.” Optimising material orientation: CrystalView The partnership continues as Agr commercialises the next level of bottle optimisation, its CrystalView system for crystallinity/material orientation management. Working as an add-on option to the Process Pilot, CrystalView provides even more refined control of the blowmoulder, allowing it to maintain desired thickness distribution while pushing the envelope on lower stretching temperatures, optimising crystalline structure (orientation). Sanpellegrino just recently completed an evaluation of the Process Pilot with CrystalView, and Chimetto is pleased with the results: “My team tells me the system makes it possible to see quality of the base in greater detail than we ever could before,” he says. This granular view helps anticipate issues, typically those involving crystallinity due to overstretching or running the process too cold. “The sooner you know of the potential variation, the better.” As an example, he cites an instance where test data revealed that two mould stations out of 20 were operating beyond the standard deviation. Previously, this condition would not have been detected until it showed up in a whitening of the base area, a waste of production time and material. The data were enough to indicate that these two stations needed attention. “We stopped the blowmoulder, made the adjustments, and further improved the overall process.” Finding the best stretching temperature is currently a trialand-error process. When overstretching is present, it is obvious. The operator knows the processing temperature needs to be raised to stabilise the process, but how much? Without a method to monitor the results, it is a matter of guesswork, taking time and risking the creation of waste, Chimetto points out. “This is where CrystalView will add value, giving us the opportunity to increase the temperature the minimum amount necessary, not just whatever the operator might think it is.” Along with the energy savings derived from operating at the lowest possible temperature for optimal production, Chimetto anticipates that the CrystalView will have the greatest impact on bottle stiffness and barrier properties. Stiffness relates to the customer experience through bottle feel, especially avoiding the oversplashing effect. Barrier properties are important for the shelf-life of the company’s carbonated beverages. A delicate balancing act “We want the best stretching, not overstretching. My team is very enthusiastic about this new equipment configuration, and I see some real advantages in these areas,” Sanpellegrino’s Applications Group Packaging Manager concludes. www.agrintl.com www.sanpellegrino.com","@ID":31}, "LABELLING 55 PETplanet Insider Vol. 17 packaging, whereby smaller batches - with their own specific labelling - are produced in very short lead times. Often undertaken in connection with a public celebration or sporting occasion, this kind of personalisation of the standard ‘everyday’ label often starts with a marketing idea. This idea then has to go through the design and production phases for the necessary artwork as well as the storage, transportation and distribution of the customised packages. The whole process for even a short-term change of label can, in fact, take well over four months from concept to delivery of the products to the point of sale. The Coca-Cola 2013 summer campaign entitled “Share a Coke” was one such example of product personalisation. Running in over 30 European countries and featuring each participating country’s 150 most common names in place of the company’s iconic logo, the campaign made the most of shorter, adaptable printing runs. It proved an outstanding success and demonstrates the impact of effective labelling. The introduction of ‘iprinting’ - which allows printing directly onto the bottle - is adding even greater possibilities for personalisation. We are already seeing the development of machines which allow consumers to mix their own drinks, with the potential for them to also have their own image printed onto the bottle. Working together for better, more sustainable labelling The same labels that have such an impact in a beverage product’s success can also have a substantial effect on the performance of the machinery upon which they are produced. So, compatibility of labels and equipment is always a key issue. Manufacturers of today’s leading labelling equipment, such as Sidel, therefore collaborate closely with label manufacturers in order to respond jointly to feedback that they actively seek from producers. However, there is more to successful labelling than the efficient application of an attractively designed label. Labelling solutions need to be designed to both maximise the impact the packaging makes on the consumer and to minimise the commercial and environmental cost of production. This requires boosting productivity through accelerated label application and cutting costs in terms of materials used and in production maintenance. www.sidel.com","@ID":57}, "TRADE SHOW PREVIEW 70 PETplanet Insider Vol. 17 No. 10/16 petpla.net Sacmi Hall 13 Booth A63 • 28mm, 33mm and 38mm screw closures • Robust and trouble free capping • Established DoubleSeal™ technology - for secure sealing performance - for better protection against micro-organisms • Slit FLEXBAND® band technology for enhanced tamper evidence • O 2 barrier and scavenging options for screw flat caps supporting longer shelf life and fresher taste • Sports closures for aseptic filling and hot filling without aluminum foil • Special closures for syrups and carton packaging Unique range of screw and sports closures designed for cold fill and aseptic application BERICAP Technology for juices, RTD teas, health drinks www.bericap.com 1,000 caps p/m with 24 cavities at a cycle time of 1.4s For the first time at the Düsseldorf fair, Sacmi’s compact line with the 24-cavity CCM compression press synchronised with the cap anti-tamper band slitter will be presented. The Colora cap digital printing solution has reached a high level of development that allows coloured caps to also be decorated, thus exploring what some consider being the final frontier of digital decoration: unlimited colour development, ultra-high definition, yet also flexibility to ensure the right response whatever the customer’s production/promotional needs. Preforms & inspection systems In the manufacture of PET preforms with injection technology, Sacmi has launched an “open-source” platform that aims to become the industry benchmark with the new IPS 400 platform. It is characterised by design specifications such as automated unloading of preforms directly into the container and, above all, maximum compatibility with the market’s most commonly used moulds. These are complete, integrated solutions, designed to make use and maintenance tasks easier and to give the manufacturer a competitive advantage through efficiency. That’s why Sacmi has developed and market-launched advanced vision and quality control systems, including ultra-high speed control (in both factory and test facilities) of preforms. The latter is performed by the PVS, the various versions of which allow inspection of every part of the preform, identifying any potential defects and eliminating any risk of inefficiencies. www.sacmi.com Petrochemicals portfolio Reliance Industries Limited (RIL) is India’s largest private sector company, with a consolidated turnover of US$ 44.7bn, cash profit of US$6.1bn and net profit of US$4.2bn for the year ended March 31, 2016. RIL is the first private sector company from India to feature in Fortune’s Global 500 list of ‘World’s Largest Corporations’, currently ranking 215th in terms of revenues and 126th in terms of profits. RIL’s petrochemicals business portfolio consists of polymers, polyester, fibre intermediates, elastomers and chemicals. Integration from refinery to petrochemicals provides feedstock security, logistics advantage and economies of scale. RIL’s wide product portfolio, world-scale capacities, integrated operations and presence in growing domestic market supports high operating rates and provides earnings stability. www.ril.com Reliance Hall 6 Booth D11","@ID":72}, "LABELLING 66 PETplanet Insider Vol. 17 No. 10/16 petpla.net CMYK digital printing on beverage closures „redcube plus” The “redcube plus” is a scalable UV DOD inline printing module designed to deliver accurate and reliable print of up to 720dpi onto blank or preprinted substrates – on demand and just in time. An upgrade path from single to multi-colour spot or CMYK printing is easy. UV pinning is available to fulfil white and/ or colour-on-colour printing. complex, costly, and time-consuming processes. Equipped with the “redcube plus” digital printing module, the new CLDP system from IMDvista – distribution partner of Hapa – produces beverage closures printed in up to seven colours, spot or CMYK printing plus white, with a print resolution of 720dpi. “redcube plus” at the heart of the CLDP system The complete IMDvista beverageclosure printing solution follows a waterfall sorter with bunker, flexible guide channels, and a spacing unit. The combined IMDvista-Hapa printing solution is housed in a separate cabinet. It begins with a pre-treatment station that ensures robust print results. At its heart is the UV DOD piezo inkjet “redcube plus” printing module. Scalable and flexible, it has an upgrade path from single colour to CMYK plus white. The system uses UV inks produced by Hapa Ink, which are solventfree and Nestlé positive-list compliant. All text and graphics are printed in a single pass at a speed of up to 1,500 pieces per minute, depending on closure size. Immediately following printing, the closures are LED-cured. After the ink is cured, the printed closures pass through an integrated IMDvista print inspection system. An automatic reject station blows out any “bad print” pieces from the line. Rounding up the printing cabinet is an automatic sampling station allowing the operator to pull out samples at any time. All data transfer for the system is fully digital. A single HMI operates printing and inspection, simplifying digital product changes. Print-job management and a printing history are included functions. Convenient handling Designed to deliver accurate, reliable and high-quality print results, the “redcube plus” is easy for existing line personnel to operate. Cleaning Direct digital printing onto closures is a novel application. It offers multicolour and colour-shading artwork opportunities as well as advantages over tampon and analogue printing methods, by increasing production flexibility, reducing changeover times substantially, and accelerating lead times. Producers can go straight from design approval to print, cutting out Hapa’s “redcube plus” lies at the heart of the IMDvista Closure Digital print solution. Hapa’s latest UV DOD printing module “redcube plus” lies at the heart of the IMDvista Closure Digital Print (CLDP) solution, a premiere for the beverage-closures market. It delivers full-colour printing of graphics and text in a CMYK plus white application, at a remarkable speed of up to 1,500 pieces per minute.","@ID":68}, "MOULD MAKING 19 PETplanet Insider Vol. 17 No. 10/16 petpla.net SPONSORS The China Road Show A top 3 moulds manufacturer By Kay Barton August 5, 2016 Guangdong Guozhu Precision Mold Co., Ltd. We met: Ms Laura Cai, Overseas Marketing Manager Mr Jungui Yang, Representative of Blowing Equipment Ms Janet Lee, Sales Representative Ms Sharon Li, Sales Representative Mould manufacturer Guozhu Precision Mold, of Guangdong, has been serving the PET industry for more than 20 years. The company is part of Guozhu Holdings Ltd., which also owns Guozhu Plastics Co., Ltd. and Guozhu Blowing Equipment Co., Ltd. It was established in 1993 by Mr Yingren Cai, who was then 50 years of age. While he saw huge opportunities for PET production in China over the years to come, the company started off with just one task: blowing bottles for the drinks industry. In 1995, having gained experience in the use of PET technology, the company developed its first injection moulding and blow moulding dies for PET, PP and PE. Its first semi-automatic blow moulding system was debuted in 1998. Guozhu subsequently received certification from Coca-Cola, first as a supplier of bottles in 2000 and then as a supplier of tools in 2002. It secured its first export contract in 2004. In 2008, the company unveiled its first injection moulding machine for preform manufacturing; in 2012, it upgraded it to a fully turn-key unit. In other areas, Guozhu launched China’s first-ever rotary blower in 2001, initially as a six cavity machine; by 2010, it had been developed to 24-cavities. “Over the years, competition increased, so we decided to expand our portfolio and our technologies, moving into activities such as the production of sealing caps,” Laura Cai, Overseas Marketing Manager, explains. “We now cooperate with a variety of other machinery manufacturers in China, who offer our moulds to their customers.” In the PET area, the company’s product range includes PET/PP preform moulds with up to 144 cavities, blow moulding dies for rotary, linear and semi-automatic systems and solutions for PE/PP closure injection moulding with cycle times approaching 3.5s. Its offerings for beverage caps range from 29/25 to PCO 1881, and with up to 72 cavities. Guozhu’s latest annual production figures show that it made about 8,000 cavities for preform moulds; about 6,000 for bottles and about 2,000 for caps and handles. Its products are compatible with almost all of the wellknown machinery suppliers. In addition, the company offers spare parts for moulds originating from European and American companies, thus helping to reduce customers’ production downtimes caused by waiting for essential replacements. Guozhu manufactures its products using equipment from Makino, Mikron, Okuma, Studer and others. The company’s production space extends to approximately 6,700m2, including its prototyping section and test lab. It employs 185 staff. In 2015 the company sold 30 rotary, 50 linear and around 50 semi-automatic blowing machines, achieving a turnover of US$25 million. Its mould sales remain heavily weighted towards its domestic market; between 10% and 20% are exported. Around half of its machinery products are destined for export. Its customers include Coca-Cola, Nongfu Spring and Huiyuan. “We are one of the top three mould manufacturing companies in China, and one of the top five suppliers of blow moulding equipment.” explains Cai. We were advised that GDXL from Foshan is Guozhu’s main competitor in the mould segment, with companies such as Tech Long Machinery leading the competition in blow-moulding systems. Guozhu is currently focusing on a new area of business: the production of PET medical packaging. Its first moulds, with 16, 24 and 32 cavities and destined for the production of collection tubes for blood samples, have already been manufactured. As well as tube production, the company wants to gain an increased market share in tools for medical applications. http://en.guozhu-pet.com F.l.t.r.: Jungui Yang, Laura Cai, Kay Barton, Janet Lee and Sharon Li Overseas Marketing Manager Laura Cai (left) with Sales Representative Janet Lee","@ID":21}, "LABELLING 58 PETplanet Insider Vol. 17 No. 10/16 petpla.net Change in the Gulf region beverage packaging market and the replacement of aluminium-sealed water cups Labels for a changing market ENPI Group, which is based in Dubai, operates from two primary locations: one each in Sharjah and in the Kingdom of Saudi Arabia (KSA). It supplies markets in the Middle East and Africa with self-adhesive labels, wraparound roll-form and cut labels, shrink sleeves, and aluminium pre-cut lids and rolls. Its products are used in the cosmetics, food and beverage, pharma, FMCG and airline segments. The Sharjah facility is equipped with a digital line and eight narrow-web Flexo lines, while the KSA plant has a selection of Flexo and Gravure lines. The business mix was, until recently, made up of 50% self-adhesive labels and 23% wrap-around, shrink sleeve and aluminium products for beverage packaging. The remaining 27% came from other segments. However, the last 12 to 18 months have seen several surprising changes. In 2015, the beverage packaging segment’s business share jumped from 23% to 31%. This coincided with a significant slide in aluminium’s market share; labels in other materials largely replaced aluminium, although the market for wraparound and shrink sleeves also increased. The past year has seen labels start to play a key role in the packaging of beverages in ENPI Group’s markets, with consequent impact on product presentation and marketing. For example, mineral water bottles had, previously, appeared in only two colours: red or blue. As beverage companies seek to target the full spectrum of markets and segments, bottles are now appearing in many colours. Child consumers represent an increasingly important market. In the past, the kids’ segment was essentially confined to chocolates and biscuits; beverage companies in the Middle East and Africa are now focused on beverages. Companies are manufacturing bottles for water, soft drinks and juices; labels and labelling play a crucial role in developing the market. Disappearance of aluminium-sealed water cups An example of the kind of dramatic change that has taken place in the market in the Gulf region is the virtual disappearance of 200ml PET water cups sealed with aluminium foil. The introduction of 200ml PET bottles saw the role of foil decline to almost zero. Since their arrival, the market share of 200, 250 and 500ml PET water bottles, available at low prices and with attractive values for children, has grown significantly. As well as drinks and juices, the children’s market for water is also growing and is expected to continue to do so. The PET cup with printed foil was not child-friendly; it was an injury hazard while tearing open the foil, which meant that they had to be kept away from children, for safety. PET bottles are not subject to those issues. Growing children’s market The ability to supply bottles in small stock keeping units (SKUs) has made the market more convenient for all segments of clients. The cost of packaging is lower, and they are also easier to transport. These advantageous features have made","@ID":60}, "LABELLING 63 PETplanet Insider Vol. 17 No. 10/16 petpla.net The evolution of shrink sleeve systems Dressed up bottles Since the birth of the PET bottle, there has been a search about how to decorate and label it. At first, it was difficult to label the bottle because the panels supposed to receive the roll fed or adhesive label were vertical, limiting the bottle design. With its shrink sleeve solutions, Italian company Finpac is freeing the bottles from form restrictions, offering new ways to “dress” them. Today, the evolution of the sleeve system is clearly evident; simply going to any supermarket we can find hundreds of coated and coloured products. The problems that occurred on the way of reaching this level were multiple and complex: in 1994, the maximum speed for sleeving a 500ml bottle was 200bpm. Since then there has been an important evolution in both the film used (now 85% shrinkage is achievable) and for the application of the sleeve on every conceivable shape. To manufacture shrink sleeving machines with a range of models that reach 36,000/4,000bph, Finpac cooperated with major suppliers of complete production lines. This speed requires a high standard of design and construction to fulfill the quality demands for the final products. The sleeve application onto the PET bottle can be made on both empty and filled bottles. Today, producers in the beverage sector constantly request increases in line speed and this led Finpac to develop a line with two heads capable of 72,000bph (for 100/500ml bottles), with two parallel conveyors applying the sleeve. The machine has been designed to allow easy access for maintenance and changing bottle size. The system can also accommodate different bottle forms and volumes and cater for partial or total body sleeves on the same line. The DL HS model is said to have an attractive throughput because the two heads are completely independent. If one head has a problem, the other can compensate by increasing the speed to maximum with a minimal loss of production. Additionally, format change is claimed to be low cost and rapid. The system offers an integrated quality control for the application of the sleeve; this monitors the sleeve position and rejects any non-conformances. The system also includes two steam tunnels designed to make a perfect shrinkage even at temperatures as low as 70-80°C (to avoid deformations of the caps and possible adverse on the product). The DL HS machine is capable of achieving up to 72,000bph, suitable for filling lines that reach 48,000/60,000bph, as it has an overcapacity of 15-20%. www.finpac.it","@ID":65}, "BOTTLES 89 PETplanet Insider Vol. 17 No. 10/16 petpla.net Cooking oil in PET The particularly light and healthy “Huile de riz” of the “Alesie” brand, suitable for cooking, baking and frying, fills a clear 500ml bottle. The gold and yellow glimmering oil contains vitamin E, Omega 3 and 6 and other ingredients said to be beneficial to one’s health. The bottle is closed with a screw cap with tamper-proof protection. Two self-adhesive labels convey the necessary trade data. www.alesierice.com Supplements in the cap On its home market, the Canadian company Biosteel Sports is selling a drink with electrolytes, minerals and micronutrients which is particularly tailored to athletes’ needs. These are enclosed in an addition chamber in the cap with flavourings and a colouring agent. By peeling off a membrane and pressing down a seal, the granular substance is released and, by shaking the bottle, the motto of the drink “Drink The Pink” becomes visible before the eyes of the user. Mixing shortly before consumption supposedly guarantees maximum effectiveness of the ingredients. The grip-friendly bottle contains 500ml of water, a sufficiently big drink opening and is equipped with various creases and embossing. www.biosteel.com Strawberry sauce in PET With maple and carob syrup as a sweetening ingredient, the English company Clarks offers an alternative to conventional dessert sauces. The natural sweetener provides reduced calories and is lighter on the body thanks to its low glycaemic index. The product is a black-coloured squeeze bottle with a content of 320g. A screwed-on hinged lid with dosage function makes it easy to squeeze out and to decorate puddings, ice cream or similar desserts. www.clarksit.co.uk","@ID":91}, "LABELLING 62 PETplanet Insider Vol. 17 No. 10/16 petpla.net Updating tradition The labelling industry has been traditional in terms of manufacturing processes for a long time, but Rivella AG, a Swiss company, claims to have started a revolution. Wrap-around labels based on thin BOPP (biaxially oriented polypropylene) foils are the bread and butter of the soft drink segment of the beverage industry, whether white-opaque, transparent, or metallised. The product has been developed over the past 35 years and has become commoditised in the most classical way – the whole value chain is targeted at cost efficiency and performance. Generally speaking, it would appear that there is not much room for innovation beyond the annually exercised struggle for further cost saving. However, a Swiss company, named Rivella AG, claims that a turnaround can be observed over the last few months. It says that wrap-around labels can be developed beyond being just a more (or less) attractively printed sleeve, wrapped around a PET bottle in a standard and not particularly exciting procedure. Those who monitor the markets may have noticed some interesting examples of truly original product innovations. Dynamic appearance with precision Swiss company Rivella claims to be one such example. Their PET bottles’ new design has a young and dynamic appearance and features a completely redesigned wrap-around label. The bottle’s texture, with its distinct lines, symbolises the mountains in Switzerland. It is the same cross-design that was used for the contour-punched label and it is this that makes the new bottle catch the eye. The label’s punched outer contour has been precisely customised to the bottle’s texture. “We had a vision, and after intensive discussions and with the involvement of our suppliers, we managed to bring it to life,” says Heinz Hohl, head of supply chain at Rivella, and further claims that this design feature has never been seen before in the beverage industry, that it is a true innovation. “The greatest challenge was achieving the bottle’s perfect alignment in production, so that the labels are always positioned exactly.” This means that label production at Constantia Labels GmbH is not at all as trivial as with conventional wraparound labels. The production process of the in-line rotational punched and fabricated label rolls makes high demands on the manufacturer. Narrow tolerances must be complied with; the coordination of tools and materials requires the highest precision in order to punch the transparent OPP label material pin-sharp and keep tool wear to a minimum. New label generation “This innovation could be the breakthrough for a new generation of wrap-around labels,” says Gerd Blecken, head of R&D Constantia Labels GmbH. He explained that his company’s greatest challenge was to ensure compliance with the tight manufacturing tolerances, thus allowing for an undisturbed labelling process. “Leaving well-worn paths and having the courage to use contourpunched wrap-around labels for this kind of neck labelling for the first time is greatly to the credit of Rivella AG.” www.cflex.com www.rivella.com","@ID":64}, "NEWS 7 PETplanet Insider Vol. 17 No. 10/16 petpla.net i Developing economies are driving growth for the labels market Economic and lifestyle changes and the focus on sustainable packaging will drive market growth for the labels market by 5.4% annually in 2016-2021 to $44.8 billion, according to a report by Smithers Pira. In “The Future of Labels and Release Liners to 2021” Smithers Pira’s analysis shows label market growth is being driven by economic, social, demographic and lifestyle changes. These include brand owners’ increasing focus on source reduction and sustainable packaging, consumer demand for convenience food, and the growing presence of large retail chains. Label market demand is also being driven by the relatively low cost with which labelling can be replaced or changed; and a continuing need for barcodes and other secondary packaging applications that support food safety and pharmaceutical compliance issues. Drinks markets are dominating label consumption; alcoholic drinks are the main end-use market for labels, accounting for a projected 27.5% share of global label consumption in 2016. The alcoholic drinks market growth is supported by the booming hospitality and tourism industries in large cities, the influence of western culture on young people in emerging economies, and increasing disposable incomes among the growing middle class in Asia. “The outlook for label market growth will be negatively influenced by an expectation of moderate global economic growth over the forecast period.” states Dan Rogers, head of publishing at Smithers Pira. “The emerging and developing economies are forecast to grow at twice the rate of advanced countries and offer the best opportunities for label market growth.” The growing trend for sustainability in packaging and labelling means linerless labelling systems are gaining in popularity, because they eliminate the need for non-recyclable release liners, and the absence of backing material means that reel changes are quicker and easier. Linerless technology also provides full-colour, high-end graphics, together with the option to print on the back of the label for promotional, coupon and instructional applications. Linerless labels also eliminate waste and reduce cost associated with label production. www.smitherspira.com Mexico: collecting and recycling post-consumer PET The non-profit environmental association Ecoce is promoting the collection and recycling of post-consumer PET and other materials in Mexico. The association has now published new figures on recycling in Mexico: according to their own figures, Mexico has recorded the highest collection quota in America for PET for the past four years. In 2015 the collection quota amounted to 50.4% (364,000t) of national consumption (722,000t). The association also reported an increased demand from the Mexican recycling industry from 191,000t (46%) in 2014 to 218,000t (60%) in 2015. 40% of the PET collected is exported. Export countries are China, the USA and others. Mexico has 14 PET recycling plants (total capacity: 300,000t/a, total investment: US$314m) There are currently efforts to further develop the national recycling capacity. The experiences of the past 14 years have encouraged Ecoce to push for the collection of further packaging waste materials such as aluminium, PE and other materials. In relation to these efforts, Ecoce has been carrying out a threetiered campaign “Reciclamos tus envases” (Let’s collect your packaging) since March 2016, which aims to raise public awareness about the collection and recycling of packaging materials over the long-term. Ecoce brings together 24 member companies from the food and beverage industry. These represent 64% of the national PET consumption. www.ecoce.mx Upcoming PET-relevant events The major players in the PET value chain are taking part in many local and global PET events, from trade shows to conferences or company events. For full details, see the Events Calendar in WikiPETia. You can also find details of PETplanet’s activities as the media networker and expert partner for many events. Are you an event organiser? Has your event been included? If not, contact us at [email protected] and send relevant information. www.wikipetia.info","@ID":9}, "TRADE SHOW PREVIEW 73 PETplanet Insider Vol. 17 No. 10/16 petpla.net Flexibility as a concept For most PET converters, the overall market is growing while average bottle quantities per contract are getting smaller. This means a variety of different orders have to be produced within the same time frame, for example to include different neck types. To meet such demanding circumstances, increased flexibility is the only way forward. 1 Blow PET blow-moulding machines perfectly meet the demands of this changing market with preferential heating, neck orientation, hotfill and deep grip, which can be installed on new as well as on existing machines (as upgrades). In other words, the machine’s investment is perfectly in accordance with the market’s expectations. The 1 Blow range is being continually expanded with the 2XLS and 4XLS types, allowing bottles of 5l and 1 gallon to be produced.All types of existing moulds are interchangeable. www.1blow.com 1 Blow Hall 13 Booth C85 Colour explorers Repi is attending K2016 with a new image and communication approach, in line with the company’s expansion strategy. Under the banner “Colour Explorers”, the company’s team will guide visitors on the Repi stand through a unique sensorial experience of colour gradations blending into a total white look, the “non-colour” for excellence, underlining the company’s capability to offer every solution in its core business. Video projections and multimedia contents dominate the space and tell the history of the company, as well as outlining the portfolio of products, testing and services available to customers. In its 43 years of business, Repi has tirelessly explored the world of colours, pioneering the use of liquids for plastics and building ties with customers and partners which are based on trust and the exchange of knowledge. These are the keys to turning clever ideas into concrete solutions, thus offering the market what it is looking for. Repi’s intuition to specialise in liquids was revealed to be even more successful, allowing it to reach a leading position in the field of colourants and additives for plastics. www.repi.com Repi Hall 6 Booth B24","@ID":75}, "88 PETplanet Insider Vol. 17 No. 10/16 petpla.net BOTTLES PETbottles Beverage + Liquid Foo Natural mineral water by Vöslauer Vöslauer Mineralwasser AG fills lightly-coloured bottles with natural mineral water from the artesian spring known since Roman times. The bottles branded with the name “Junior” are aimed to give children an understanding of healthy drinking habits. As well as the colourful bottles, the labels are supplied with detachable adhesive stickers which aim to direct children’s interest to the product. The bottles are closed with a drinking cap with resealable hinged lid and a colourful spout. www.voeslauer.de Cooking wine Under the brand “La Villageoise” various wines are on offer in France that are particularly intended for the preparation or refining of dishes. These wines fill coloured 150ml or 250ml plastic bottles with a waisted design. Wraparound labels contain product information. At POS, several bottles are stacked together on a cardboard tray as a sales unit, and in campaigns measuring cups are put on the screw caps in the shape of chefs’ hats. www.la-villageoise.com Cocktail to go A two compartment package - with the bottom container snapping into the base of the larger top bottle - is being used to launch a new portable, shelfstable cocktail line. Called the Clasper bottle, the package development was driven by brand owner Yumix’ desire to give adult consumers a great tasting cocktail, which they could mix themselves anywhere, anytime. The Clasper bottle, engineered by Plastic Technologies, Inc. (PTI), is a combination of two PET containers and a shrink label. The bottom holds 50ml of premium alcohol and features a heat-applied aluminum-foil seal. The main bottle holds 6.5oz of hot-filled, shelf-stable juice and is topped by a 38mm PP closure. Added visual appeal is provided by shrink-label graphics which also include usage instructions. To use, the consumer simply separates the shrink sleeve at the seam between the top and bottom containers, via a perforation, unsnaps the bottom container from the base of the primary bottle, removes the heat seal and closure from the bottom and top components respectively, and pours the alcohol into the juice. www.drinkyumix.com www.plastictechnologies.com","@ID":90}, "TRADE SHOW PREVIEW 84 PETplanet Insider Vol. 17 No. 10/16 petpla.net From initial design to ready-to-produce bottle The future of PET processing At K 2016, KHS GmbH will present its current highlights in plastic packaging. Among other innovations, the manufacturer of filling and packaging systems will exhibit modules for special packaging formats which have been specifically designed for the InnoPET Blomax Series IV stretch blow moulder. The Bottles & Shapes program for individual bottle design will also feature at the trade show. The preferential heating system (PH) developed by KHS Group enables bottlers to achieve high bottle quality with extremely oval bottles in an energy-saving, safe and reliable process - especially when processing cleaning agents, laundry detergents or personal care products, which are very often filled into oval PET bottles. The systems provider offers this option for its InnoPET Blomax Series IV stretch blow moulder. During preferential heating, the preform is selectively heated depending on its later bottle shape to prevent any uneven distribution of materials. Preferential heating is made possible by a special heater section at the end of the heating segment. The system first rotates the PET preforms through the heater to obtain a basic heating profile. In the downstream PH section rotation is stopped, giving the preform its selective heating profile. Also on show will be new systems for special stretch blow moulding requirements, such as PET packaging with 70mm necks. These receptacles are known as wide mouth containers and used for various types of food packaging. For this purpose, KHS has developed a heater box which is specially tailored to suit the wide neck preform and thus requires very little heating energy. In addition, when the containers are changed over, no manual conversion is needed. The heater box is available for various container formats on the InnoPET Blomax Series IV. In the form of a video presentation, KHS will also be showing visitors its future-proof block system; with the KHS InnoPET TriBlock the KHS Group has launched a filling and packaging system for PET bottles to market which incorporates a stretch blow moulder, labeller and filler. With consistent neck handling, KHS also enables lightweight PET to be processed. From initial design to readyto-produce bottle Another focus of the trade show will be sustainable bottle design. With its Bottles & Shapes program, KHS GmbH offers beverage and food producers an all-round service which starts with individual suggestions for possible designs and ends with a bottle that is ready for production. One of the developments to come out of the Dortmund systems provider’s Bottles & Shapes program is a lightweight 1l PET bottle for milk and mixed milk beverages. Weighing just 20g, it is intended to demonstrate an attractive and light solution which is also easy on resources. In order to protect the milk against external influences, two different types of UV light barrier are used. Unlike the classic milk carton, this bottle is fully recyclable. www.khs.com KHS Hall 13 Booth A75 .com 100815dmyL","@ID":86}, "LABELLING 53 PETplanet Insider Vol. 17 No. 10/16 petpla.net be distinctive, versatile and attractive in order to be appealing to customers when it arrives on the supermarket shelf. A consequence in PET bottling production is the increased use of rollfed labels made of either paper or plastic and applied with hot glue. These labels have physical and practical qualities that make them both attractive to consumers and advantageous for the producers. For example, if the body of a transparent, colourless, plastic label with a high-gloss finish remains unprinted, the bottle can be made to look as if the lettering is applied directly onto its surface. Creative use of this illusion can, where appropriate, lead to much more aesthetically pleasing labelling. The plastic labels are also waterproof and therefore not subject to the damaging effects of damp conditions during transport and storage. Thinnest labels for PET bottles The simple step of reducing the thickness of labels on the many millions of PET bottles produced can drastically reduce the total amount of raw materials and resources used to create them. As a result, suppliers of labelling solutions are working to ensure that the thinnest labels possible can be handled efficiently and effectively by their equipment. Sidel has focused its efforts in this direction when it comes to sleeve labelling solutions to offer efficient, high-speed machines capable of handling ultra-light bottles with a label thickness of less than 20 microns. This offers the potential for significant savings on material by creating a tubular form for the sleeve in the machine and then wrapping it around the container without moving it. Labelling without glue The amount of glue used to adhere the labels to the finished bottles is something that most producers would like to reduce substantially. This desire is driven by sustainability and the desire to remove the drawbacks of using glue. The more glue used, the greater the negative effect it has on the efficiency of the labelling machinery. Eliminating the gluing process would make it possible to keep machines cleaner, more hygienic - and therefore safer for the consumer - and less maintenance intensive. The cost of glue is another factor. Although it is estimated to account for less than 1% of the total bottling cost, without it, costs could still be reduced. More importantly, the complete removal of glue from the entire labelling process would be beneficial to the production of PET bottled beverages because its presence can make the recycling process more difficult. The recycling of PET is fundamental in confirming its position as a sustainable material. Producing the virgin material naturally requires the use of finite resources, and analysis has shown that recycling uses two-thirds less energy. However, the use of label glues has sometimes affected the uptake of material in food grade applications, so work is underway to overcome the problem. In Japan, for instance, researchers are trying to develop a glue that adheres mainly to the label yet is readily released by the surface of the PET bottle. Elsewhere, some manufacturers of labelling equipment are already eliminating the use of glues altogether. Some developments, for example the design of shrink sleeve labels (SSL) with perforated seams, allow the simple removal of the label before recycling. Indeed, SSL is one area that is growing more rapidly than any other labelling technology. The growth of sleeve labelling As more companies discover the potential of SSL, the market for this kind of labelling is growing faster than any other labelling process. In 2014 it accounted for a projected 12.5% share of global label consumption by area. It continues to develop, with global consumption forecast at a compound annual growth rate (CAGR) of 5.6% from 2014-2019, according to findings by Smithers Pira Market Intelligence. The increasing use and success of this full-body labelling is due to several factors. One significant factor is the current market trend to customise the end product. The sleeve is perfectly in line with this trend, providing the capability to decorate the packaging. It offers a greater surface area to accommodate the information to be shared with the consumer, enabling product differentiation through colour, shape and messaging. This is important when you consider the buying process. When a potential customer is, say, 10m from the supermarket shelf, it will probably be the label colour that is the main focus; when they get a little closer, then its shape: and when they are really close it is the product contents. The introduction of new substrates and technologies has also brought about the potential for significant cost savings in SSL production. Until recently, substrates were heat-shrunk after being turned - or ‘oriented’ - in a ‘transverse (lateral) direction’ (TDO) and pre-formed into a tube, ready for further processing. However, substrates in PET or Oriented Polystyrene can now be shrunk ‘machine direction oriented’ or MDO. As the step of creating a tube is removed from the production process, the cost for each label is less. Greater creativity for designers Usually viewed by the consumer both when the beverage is bought and consumed, the label is still regarded as the product’s main interface with the consumer. For those charged with ‘building the brand’, the label therefore remains one of the drink’s prime means of direct communication with the Sidel Rollsleeve labeller","@ID":55}, "CAPPING / CLOSURES 41 PETplanet Insider Vol. 17 No. 10/16 petpla.net F.l.t.r.: Michael Chen, Managing Director of Bericap China and Alexander Büchler, PETplanet Insider in front of the Editourmobil Patented cap increases shelf life for sensitive beverage ingredients The cap with the built-in lid CapAble AB was founded in 2008 and is headquartered in Stockholm, Sweden. The company is 90% owned by BioGaia AB and is specialised in functional packaging. It is the exclusive supplier of LifeTop closure products. The LifeTop cap is a patented bottle closure where sensitive powder ingredients are placed in a protective aluminium blister inside the cap. This protection increases shelf life considerably longer compared with ingredients mixed into the drink. When the top is pushed, the blister breaks open and the powder is released into the beverage. This new solution makes it possible to develop shelf stable beverages with sensitive ingredients, such as probiotics. The packaging system handles room temperature storage and offers a longer shelf life for sensitive ingredients. Compatible with existing PET bottles and production lines, the LifeTop cap is designed to fit standard bottlenecks. Customers can get production swiftly underway with minimum modifications to the production lines. The available finish for low and high profile is about 30 and 25mm. The blister capacity is around 300g of powder. The material of the blister has a full aluminium laminate barrier. The LDPE closure is available in seven different colours. Mass Probiotics, Inc. is a partner of LifeTop. The company researches, develops, produces and markets a family of probiotic and prebiotic beverages and powder packet products under the brand name GoLive. Additionally, the company is developing products for clinical and institutional use. All GoLive products contain a complex blend of human-commensurate probiotic strains, coupled with a variety of prebiotic organic sugars and prebiotic soluble fibres, to provide superior support for the body’s digestive, metabolic and immune functions. All GoLive probiotics are kept freeze-dried in individually-packaged servings to ensure the probiotics are delivered alive when it counts: at time of consumption. www.lifetop.eu www.golivebewell.com www.biogaia.com","@ID":43}, "TRADE SHOW PREVIEW 82 PETplanet Insider Vol. 17 No. 10/16 petpla.net Xtreme injection-compression moulding of ultralight PET preforms Xtremely thin walls Sipa Hall 13 Booth B11 The Xtreme injection-compression moulding system is different from other injection-compression systems: preform moulds in blocks of three cavities are mounted on a high-speed carousel, and an extruder delivers melt to dosing devices mounted under the moulds. Sipa will present the smallest version of the Xtreme at K 2016, capable of holding between 12 and 24 cavities. Xtreme is said to produce preforms that are up to 10% lighter than the lightest injection moulded preform - without losing any key properties when blown into the bottle. It is possible to make a preform for a 500ml bottle that weighs just 6g. Injectioncompression moulding makes it possible to use lower injection pressures and lower clamp forces. With less stress being put on the melt, acetaldehyde (AA) levels are reduced by as much as 40%. The drop in intrinsic viscosity, IV, is also much less than in injection moulding: over 70% less, in fact. 100% part inspection, fastest-inthe industry mould changeover and no hydraulic system are some of the benefits delivered by the Xtreme. As a continuous process centered on a rotary production platform, Xtreme is well suited to downstream integration into rotary bottle blowing, thus benefitting from lower energy costs (no IR oven) and higher uptime (no preform feeder). Sipa has begun selling Xtreme Sincro, the first monobloc injection-compression-stretch-blow moulding system. The first unit will go into commercial operation next year. Xtreme has also been shown to be ideal for upstream integration: Sipa has partnered with Erema, a leader in recycling technology, to develop Xtreme Renew, an integrated system for inline production of food contact approved preforms starting from 100% post-consumer PET flakes without the need for pre-drying. Another alternative to preform lightweighting: X-Mould For PET preform producers wedded to conventional injection moulding, Sipa launched a preform","@ID":84}, "BOTTLING / FILLING 37 PETplanet Insider Vol. 17 No. 10/16 petpla.net “In 1989 we saw a developing trend towards PET bottles in Japan and other countries across South East Asia,” Hans Hou recalls. “We got off the ground in 1990 as ‘China Resources C’estbon’ and we were one of the first bottlers to focus on production of purified water under our own brand name, packaged in PET. We are still producing own-brand water to this day. Until around the year 2000, the key focus of our products was on southern China; we went nationwide in 2010. Our success throughout the country is based on the strategy that we embarked on with China Resources Holding in 2008, of rolling the brand out from the regional level to the whole of China, in the form of both sales and production.” The product’s history of popularity in southern China was an important factor in its nationwide success. In a market like China, where water plays a dominant role, the price, quality and brand of a product deeply influence the ultimate purchasing decision. Bottled water accounts for over 90% of C’estbon’s business; in 2015 it bottled 7m tonnes of water, the majority (approximately 85%) packaged in small bottle sizes. It offers the following packaging sizes: 350ml, 555ml, 1.555l, 4.5l and 18.9l. With a total of 40 factories in China, including two aseptic lines – one each in Guangdong and Shanghai – the company has achieved substantial market coverage. It also deploys its production capacities as a co-packer and, in addition to still water, offers mineral water, RTD tea, coffee, and functional drinks. C’estbon consumes around 180,000t of PET annually and works with up to eight suppliers of preforms, who manufacture primarily on Husky, Huayan and Unique equipment, Lu Jing explained. Complete systems from CBE, Sidel, Tech Long and Newamstar, along with others, are used for bottle blowing and filling. “It is important to us that we convey our company philosophy along with our product,” Hans Hou explains. “C’estbon aims to stand for trust, quality and culture, and those are the values that we want to convey to our customers. It is also important to us that we further improve, all the time, and that we continue learning.” www.cre.com.hk Swiss Made | www.imdvista.ch K16 Düsseldorf, 19.–26. October 2016 Inspection Systems for the Plastic Packaging Industry IMDvista TWIN «Flying Closure» for true, 100% inspection. See newly invented closure testing @ Husky, Hall 13 Stand A61 IMDvista PRINT «Roll to Roll» print inspection for a perfect design. See this well integrated system @ PackSysGlobal, Hall 3 Stand D90 IMDvista LAYER «Multi-Layer» measurement for transparent & opaque plastic. See the new terahertz technology @Milacron, Hall 15 Stand C06","@ID":39}, "LABELLING 59 PETplanet Insider Vol. 17 No. 10/16 petpla.net the 200ml and 250ml bottles very popular. With labels coming in pink and many other cartoon colours, PET bottles are becoming progressively more attractive to children and are seen more and more often in their lunch boxes. Indeed, it is the children’s market where the effectiveness of labels in sales, marketing and promotion is most obvious. The availability of cheaper labelling technology also helps broader adoption. For example, premium water brands such as Sparkle Water and Flavoured Water have, for a long time, used selfadhesive labels. When compared to ordinary bottle packaging, selfadhesive labels and their application machinery cost five times as much. They have been able to survive primarily because of goodwill and a large existing market share in the beverages sector. However, as pointed out earlier, PET cups sealed with aluminium foil – the dominant product for many years – are on their way out. As a result of wider adoption of PET bottles, the use of OPP (oriented polypropylene film) and PVC labels has increased by several multiples. They are more receptive to attractive graphics than is aluminium foil. The most convenient labels for juices and premium drinks are the shrink sleeves, which facilitate the use of the entire circumference and length of the label for graphics and with more text, in higher resolution. The printing of cartoon characters and their long lasting value during display in shelves are the key elements in attracting customers, children especially. ENPI Group has the capability to print in Flexo at 200 lpi (lines per inch) resolution, as well as gravure. Flexo can be used for small quantities; depending on bottle shape, the material can be PVC or PET. For soft drinks, energy liquids and water, shrink sleeves labels are quite expensive; OPP labels, on the other hand, are quite economical for this category. Price is a key component for any product; the main difference between shrink sleeves and OPP wraparound labels is that in the case of shrink sleeves, the material is expensive but the applicator is not, and it is the other way round in the case of OPP wraparound. The choice of label will depend on the product, the bottle concept, price and other factors, but clients can be assured that both options are available. Clean and clear packaging A radical change to beverage labels has been the greater use of clean and clear packaging. Any information that is clear and not lengthy will always be welcomed by the customer. Clear and transparent labels have been well received, both in OPP and shrink sleeve form. See-through packaging can boost sales, whether totally transparent or with see-through windows. Companies that are transparent about their ingredients, sourcing and business practices are reaping the benefits of consumer goodwill and trust. Transparency in the food and beverages sector is a key element for the consumer to be drawn towards the product through the package. See-through packaging has now entered all segments of beverages, including water. www.futurepack.ae www.stf-group.de ENGINEERING WITH THE COMPETENCE OF THE RECYCLER rComplete Plastic Sorting and Washing Lines engineered by Europe’s largest PET Recycler rBottle-to-Bottle rPET Recycling rMore than 60 PET Recycling Lines installed worldwide www.stf-group.de Booth 12 / F56","@ID":61}, "LABELLING 61 PETplanet Insider Vol. 17 No. 10/16 petpla.net Body care products manufacturer Mann & Schröder relies on Gernep labelling solutions A multitude of cosmetics reliably labelled Mann & Schröder GmbH, a German multinational specialist in body and hair care products, successfully installed two Gernep rotary labelling machines in early 2016. The servodriven machines, model Soluta, are reliably labelling a multitude of cosmetic products. Mann & Schröder have been developing and manufacturing highquality hair and body care products for more than 60 years. The company has production plants both in Germany and in Russia and markets its products worldwide. Mann & Schröder’s philosophy is to supply cosmetic products for a healthy and smart appearance across all age and income groups. When choosing suppliers, the family company, whose sales exceed €100m, places great importance on high quality and sustainability. It were these two factors in particular that favoured the Gernep equipment. In addition to the technical solutions, the quality and capacity of machines, and the use of Herma applicators were other factors that made Mann & Schröder opt for Gernep. A fast machine… The project began with a labelling machine model, Soluta 18-1320 5Sk SD. Like all rotary labellers of this series, the machine efficiently applies self-adhesive labels from the reel onto a large variety of containers. The label feed is controlled by SPS controlled servo technology, which is said to guarantee high precision labelling. The round design of the machine table at the operator side offers ease of use for the self-adhesive labelling stations that can be completely removed from the machine. Two dispensers per label position ensure a non-stop operation. Products are fed in bulk, single or upright to the Soluta 18-1320 5Sk SD installed at the Sigelsbach plant. For maximum flexibility, different printing systems like ink-jet and hot embossing are integrated into the machine. The containers are oriented by servodriven bottle plates, while the orientation of dispenser bottles has been solved by moving the spouts to the correct position. The Soluta 18-1320 5Sk SD operating at Mann & Schröder has a capacity of 220 containers per minute. Labels are always positioned Heinrich Dick, head of filling operations at Mann & Schröder, would opt for even more Gernep labellers, but lack of floor space in the factory currently prevents this wish from coming to fruition. The higher-capacity Gernep labeller applies self-adhesive labels onto eight packaging formats, the smaller machine can label up to 18 different packaging formats. exactly, even on bottles fitted with a pump dispenser, an operation ensured by an integrated label control system. Like most labellers currently supplied by Gernep, the machine is equipped with remote control and production data capture. The Soluta 18-1320 5Sk SD applies labels onto eight different containers formats, ranging from 250 to 500ml. … and a slower machine The second machine supplied by Gernep to Mann & Schröder is a Soluta 8-784 3Sk SD with a capacity of 100 containers per minute. The machine features servo-driven bottle plates, a label position control and remote control and production data capture. The “small” labeller is used to apply self-adhesive labels onto 18 different formats, from 50 to 500 ml. www.gernep.de","@ID":63}, "TRADE SHOW PREVIEW 74 PETplanet Insider Vol. 17 No. 10/16 petpla.net Terekas Hall 1 Booth 26 ALPS machines leak test more than 25 billion , Booth B65 or visit FIND OUT WHY Reduced size, increased attention International trade fairs constitute an important tool when knocking on the door of new markets. Terekas Sweden AB takes part in several exhibitions each year and finds them useful. “We are currently preparing for the K show in Düsseldorf where we will be introducing our latest PET stretch blower, FlexBlow, that we have been developing for two years. It is a reduced size blower intended for those who need flexibility in relatively small production quantities. Normally PET blowers are rather sizeable and take up a lot of space, so we came up with the idea of building a compact machine that takes up no more space than a saloon car and is easy to operate,” Gintautas Maksvytis, Head of Export, notes. According to Maksvytis, interest in the new model is so high that to support inquiries Terekas Sweden AB is looking to hire 12 additional sales representatives by the end of 2016. The all-electric FlexBlow machines range from 1-5 cavities with a bottle output from 1,000bph up to 7,500bph. It was built for quick bottle format changeover that takes 30m including the change of neck standard, mould, fine tuning and start-up, and will be demonstrated in two continents at the same time in October 2016: at the K-Show, Düsseldorf and at the showrooms of K&G Machinery Works Ltd in Toronto, Canada. In combination with the Sales Conveyor promotion method, Terekas Sweden AB has tripled their flexible PET blower sales this year compared to last year. The company has already signed 17 contracts across the world to date, having sold six flexible series machines last year. The latest contract signed with a South African Republic company at the beginning of August was the first sale on the African continent. “We believe that more are on the way. After visiting a number of potential clients in SAR this summer we received the first inquiry immediately from the company that was looking for what we had to offer. They signed a reference agreement with us after purchasing the machine, indicating that we will be allowed to bring other potential customers from the country to see our technology in operation at their premises“, said Maksvytis. www.flexblow.com Integration of production and storage Chinese Newamstar Packaging Machinery will show solutions for integrating and intelligentising the liquid food beverage production, packaging, storage and logistics through the integration of a blowingfilling-capping Combi production line and intelligent stereoscopic warehouse. With the help of “internet+” technology and intelligent terminals, food safety traceability and food & beverage safety has been improved. www.newamstar.com Newamstar Hall 12 Booth D31","@ID":76}, "PETcontents 10/16 4 PETplanet Insider Vol. 17 No. 10/16 petpla.net INSIDE TRACK 3 Editorial 4 Contents 6 News 88 PET bottles for Beverage + Liquid Food 90 PET bottles for Home + Personal Care 92 Patents MATERIAL / RECYCLING 10 A circle of PET life - displaying the whole supply chain, part 1 12 Concepts for bottle grade PET MOULD MAKING 16 Customer services for moulds 19 A top 3 moulds manufacturer 20 The vision of 25% exports PREFORM PRODUCTION 22 Injection moulds made in Guangzhou BOTTLE MAKING 24 From glass to PET INSPECTION 26 Control is better BOTTLING / FILLING 30 From plastics processor to OEM bottler 34 rPET for purified water 36 40 filling factories in China CAPPING/CLOSURES 38 Strengthening business relations with a second plant 41 The cap with the built-in lid 42 Bottles, Preforms and Closures, part 9 MARKET SURVEY 50 Suppliers of compressors LABELLING 52 The labelling of PET bottles today and tomorrow 56 No contact, no wear 58 Labels for a changing market 60 Without leaving traces 61 A multitide of cosmetics reliably labelled 62 Updating tradition 63 Dressed up bottles 64 Labelled as required 66 CMYK digital printing on beverage closures TRADE SHOW PREVIEW 68 K Show preview 77 Colour: from idea to production 78 50l in PET 80 Winfactory 4.0 81 Purified polymer 82 Xtremely thin walls 84 The future of PET processing 86 Bundled expertise on PET recycling BUYER’S GUIDE 93 Get listed! The China Road Show Page 61 Page 22 Page 78","@ID":6}, "BOTTLING / FILLING 34 PETplanet Insider Vol. 17 No. 10/16 petpla.net SPONSORS The China Road Show F.l.t.r.: Michael Chen, Managing Director of Bericap China and Alexander Büchler, PETplanet Insider in front of the Editourmobil rPET for purified water By Kay Barton August 3, 2016, A.S. Watson Group, Watsons Water We met: Mr Kim Siu, General Manager Marketing Ms Tracy Yuen, Brand Manager “What many people don’t know is that, in historical terms, the company actually started in Guangzhou in the year 1828 as a pharmaceuticals business, before moving to Hong Kong in 1841,” says Kim Siu, launching the discussion. He has been at the company for four years, since joining from Coca-Cola. “Hong Kong is often thought to be where the company started life, but its history goes back quite a lot further. And another thing a lot of people don’t know is that it began manufacturing its first beverages in 1875.” The company was founded in 1828 by Dr Alexander Skirving Watson, who wanted to be able to provide poor people with good quality, hygienic and medically safe water. He began distilling water for this purpose. After moving from Guangzhou to Hong Kong, the year 1875 saw the initial bottling of six differ nt CSD drinks. Sinc 1903, A.S. Watson has focused exclusively on the commercialisation of purified water. Over over the following decades, the product - then sold in glass bottles - gained a firm local foothold. The glass bottles were superseded in 1977, with the company progressing subsequently to the production of PET bottles. In 1981, A.S. Watson became a subsidiary of the CK Hutchison Holdings, which serves a variety of market segments, including retail. With the A.S. Watson Group and the internationally acknowledged Watson Stores, it is now the biggest Health & Beauty retailer in the world. Its first PET bottling system began operating at the Hong Kong facility in 1989. The first factory for carboy production opened in Beijing, in 1994; production has been in PET since 2012. The year 1996 saw the opening, in Guangzhou – the company’s original home – of another plant for can filling of CSD and tea. The three locations serve the local market as well as Macau, Taiwan, Singapore, the Philippines and the The Tai Po Industrial Estate in Hong Kong is home to the current headquarters of Watsons Water, a leading international water brand, which is part of the A.S. Watson Group, itself part of CK Hutchison Holdings. The water bottling business has a history stretching back nearly 200 years and now holds one of the biggest market shares in the purified water segment. As part of the China Road Show Tour I met with Kim Siu, General Manager Marketing, and talked about the company’s roots and philosophy, its impact on the markets in Hong Kong and China, and the ideas and trends of both today and tomorrow. General Manager Kim Siu in front of Watsons Water’s entrance area","@ID":36}, "Milliken presents Milliken’s ClearShield UV absorbers offer safe protection for home and personal care PET packaging To better meet consumer needs and demands, makers of home- and personal-care products increasingly are using more natural ingredients, while also embracing memorable colors, active ingredients and special additives. But they’re finding that UV light can negatively impact some of these new ingredients, and current UV filters come with their own challenges. This dish washing liquid was exposed to 45 accelerated QUV hours. The ClearShield protected PET bottle (right) retained its color while the unprotected bottle (left) lost the color. without ClearShield with ClearShield Specialty chemicals supplier Milliken & Co. has developed a better alternative. It created its ClearShield UV absorber specifically to address these issues in PET packaging. This crystal-clear additive offers a wider range of UV protection than other products (up to 390 nm), has proven efficacy in protecting sensitive ingredients such as vitamins and dyes, and retains the high transparency of PET without unwanted shading. Use of Milliken’s ClearShield UV absorber in the packaging offers an alternative, simpler way to provide UV protection to formulations without reworking the composition. It also gives more freedom in formulation design and confidence in the end-product quality, as it is possible to extend the formulation shelf-life and avoid color fading while keeping the visual appeal of a product in transparent packaging. Adopting Milliken’s ClearShield UV absorber in your PET packaging can allow brand owners to use sensitive, natural ingredients, extend their products’ shelf life, and remain friendly to recycling streams — all while avoiding regulatory uncertainty and the complexity of an extra formulation step. Milliken ClearShield UV absorbers — for better, brighter, more stable and more sustainable PET packaging. Naturally. © 2016. ClearShield is a registered trademark of Milliken & Company. Milliken is a registered trademark of Milliken & Company. Stop by to see us at K 2016, Booth A27, Hall 6and learn more online at www.millikenchemical.com/K2016","@ID":42}, "LABELLING 65 PETplanet Insider Vol. 17 No. 10/16 petpla.net The Innoket Neo in Nałęczów ensures a smooth labelling process. The result: Cisowianka in 1.5l bottles. The Innoket is claimed to combine state-of-the-art technology with simple operation. vers, for instance, the entire station can be extended by 40cm on special runners. This provides access to areas which, on standard machines, are hidden inside the machine body behind other parts and only partially accessible. In addition, the entire label magazine is mounted on a swivel table, enabling the important magazine head to also be perfectly adjusted with its fixing clips. Another definitive factor in the success of the project was the cooperative partnership during the planning phase which continued on into the fast commissioning phase and beyond, explains Banaśkiewicz, with the systems supplier from Dortmund in Germany putting together the best complete package. www.khs.com MHT MOLD & HOTRUNNER TECHNOLOGY AG Your Machine - Our Solution 1996-2016 20YEARS Booth 1C35","@ID":67}, "CAPPING / CLOSURES 38 PETplanet Insider Vol. 17 No. 10/16 petpla.net SPONSORS The China Road Show F.l.t.r.: Michael Chen, Managing Director of Bericap China and Alexander Büchler, PETplanet Insider in front of the Editourmobil Strengthening business relations with a second plant Production Manager Jackie Hu (left) and Kay Barton in the manufacturing area By Kay Barton August 12, 2016, Bericap (Zhuhai) Co., Ltd. We met: Mr Eric Eng, Plant Director Mr Jackie Hu, Production Manager In 2014, Bericap opened its second plant in the People’s Republic of China. Its first - and main - manufacturing plant is in Kunshan, in Jiangsu province, not far from Shanghai. The new facility, which represents a US$26.7 million investment, is located in the southern coastal city Zhuhai, in the province of Guangdong, approximately 100km south of Guangzhou. Around 60% of its area of 20,000m2 is dedicated to manufacturing. It supplies to the regions around southern China and Hong Kong, and exports to customers in Vietnam and the Philippines. This plant will also eventually support Bericap China’s customers in South-West China until Bericap China builds a South-West China manufacturing plant in about 2-5 years time. The Zhuhai plant’s main customers are, currently, sauce makers market leaders, namely the Lee Kum Kee Group of Hong Kong, and Hai Tian of Foshan China. The balance of production output is destined for more than ten smaller-scale PET bottlers, who primarily bottle water and other beverages. The plant is also planning for production lines for some major edible oil and sauce customers in the next two years. When I visited the new Bericap plant, I discussed the strategic factors that led to the choice of Zhuhai as the location for it, along with current and future potential opportunities. I spoke to Eric Eng, who has Malaysian roots, was appointed to the position of Plant Director in June 2016, and to Jackie Hu, Production Manager, who moved to Zhu ai in 2014 after more than ten years at Bericap’s Kunshan plant in Eastern China. “We use HDPE and LLDPE in our materials mix. We have 15 injection moulding machines available for manufacturing, plus the corresponding periphery. Our sales forecast for 2016 is currently in the region of US$13.5 million. While sales of closures for PET applications tailed off a little last year, they now appear to be increasing again,” Eng says. Jackie Hu provided figures for output since the launch of the location. Its first year of operations, 2014, saw the production of about 100 million closures, in 2015: about 400 million closures. The 2016 forecast is for 650 million closures. “We supply the standard 38mm caps for all PET bottlers,” Eric Eng continues. “For liquid food, such as sauces and cooking oils, we manufacture three different types of closures in 29mm and 36mm which caters to our customers’ glass and PET bottles applications. Since Bericap does not have a production plant in Vietnam or the Philippines, Zhuhai partially supplies to those markets as well. “We want to further strengthen our business relations with our key customers,” he says. “We have the technology and products that can customise to cater for their closure solutions. We have at least four new projects pending in 2017, three of which have PET relevance.” www.bericap.com Talks at Bericap with Eric Eng and Jackie Hu (f.l.t.r.)","@ID":40}, "MATERIAL / RECYCLING 13 PETplanet Insider Vol. 17 No. 10/16 petpla.net MATERIAL / RECYCLING 13 Production cost savings and flexibility The production cost comparison in fig. 2 shows that MTR still has a big cost advantage in the rage of 15% compared to “new style” SSP and more than 20% compared to “old style” SSP. The reason behind this is that MTR technology makes total use of the latent heat of the chips and does not require any energy input for the final AA-removal step. This results in great Opex savings for MTR, because even the “new style” SSP requires heat input into the crystallisation, massive energy input to the SSP reactor and lots of electrical energy for running the huge nitrogen circulation blowers and nitrogen cleaning systems. The biggest cost factor that contributes to the production cost is the raw material with approximately 90% of the cost. Other contributions to production cost are capital-, energy-, maintenance- and labor cost. Additionally MTR technology provides higher flexibility noticeable in the fast transition time from one product grade to another (e.g. IV change) and low respectively zero inventory in the system. Fig. 2: Cost comparison MTR technology versus “old style” and “new style” SSP technology Fig. 3 Comparison of cost savings and flexibility","@ID":15}, "BOTTLING / FILLING 30 PETplanet Insider Vol. 17 No. 10/16 petpla.net SPONSORS The China Road Show From plastics processor to OEM bottler By Kay Barton August 1, 2016, Taiwan Hon Chuan Enterprise Co. Ltd. We met: Mr Keith Dai, Chairman Ms Julia Tang, Sales Representative Mrs Joanne Liu, Project Manager Trading Department If there is one name that stands out in the drinks market in China and its bottle industry, it is processor and bottler Taiwan Hon Chuan (THC). As its name suggests, the company is based in Taiwan, but the fact that it is not located on the mainland has not prevented it from playing a leading role in the markets throughout Asia, and particularly in China; it is in the mainland that THC has most of its locations and employs the majority of its staff. During PETplanet’s China Road Show, it seemed entirely natural to take the time to visit the city of Taichung in Taiwan. Once there, we were able to meet with the Chairman of THC, Keith Dai, and to gain a better understanding of the company itself and its philosophy towards its extended home market. THC was established as “Tai Hong Industrial” in Zhang Hua in 1969. Over subsequent years it developed from being a supplier of packaging materials into a provider of shelf-ready drinks products. In 1988, the rapidly expanding company moved into an industrial estate in Taichung. Over the course of the 1990s it launched a variety of wholesale companies to serve clients in a range of markets. Among its subsidiaries was the biggest manufacturer of aluminium sealing caps in Taiwan. In 1993 THC opened its first plant on the mainland, in Suzhou, China. After the liberalising of the Chinese market in the early 1990s, China offered opportunities for external investors to gain a local foothold. THC benefited from this culture, which provided the basis for its decision to make further investments. The company adopted its current name in 1999 and floated on the stock market in 2001. In 2003, further plants and additional expansion in mainland China followed. 2004 saw the installation of its first in-house bottling lines, which completed its drive to full vertical integration, from the production of preforms, bottles and sealing caps to the bottling and labelling of drinks. In the following years, THC conquered further markets in Asia. It installed its first aseptic line at its base in Taichung in 2006, with more to follow in other countries, including mainland China from 2013 onwards. In 2016 it opened its first plant for preforms and sealing caps in Mozambique, which was established to serve the African market. Today, THC is the biggest manufacturer of preforms and plastic bottles and the biggest bottler in Taiwan, and is one of the top three in the South-East Asia market. Altogether, THC now has eight plants in Taiwan, 17 in China and another 15 spread across Myanmar, Indonesia, Thailand, Cambodia, Vietnam and Malaysia. Just under 4,900 employees and 738,000m2 of production space are dedicated to the The China Road Show meets Taiwan, f.r.t.l.: Hon Chuan Chairman Keith Dai and Kay Barton, PETplanet","@ID":32}, "CAPPING / CLOSURES 47 PETplanet Insider Vol. 17 4.8.8 Carbonation Retention Non-top Load Capped and filled bottles are conditioned at 22°C (72°F). The carbonation level is checked after 24 hours and 1, 3, 6, 9, and 12 weeks. These intervals may vary by container size and beverage company. If one or more samples show significantly larger carbonation loss than the group average, the cause must be found. This is important because both closure and bottle contribute to the loss. Acceptable carbonation loss during the test period also varies greatly, but 10–15% is used by many companies. 4.8.9 Carbonation Retention at Elevated Temperature Capped and filled bottles are conditioned at 42°C (108°F) for 16 hours. They are then removed from the chamber and stabilized at room temperature for 24 hours, and the carbonation is measured. Carbonation loss must not be significantly different from the carbonation retention non-top load test. 4.8.10 Carbonation Retention withTop Load Capped and filled bottles are conditioned at 42°C (104°F) for 24 hours. They are removed from the chamber and left to stabilize at ambient conditions for another 24 hours. Then the top load of 45.5kg (100lb) is applied for 5 days. After another 24 hours and 1, 3, 6, 9, and 12 weeks at ambient conditions without top load, the carbonation is checked again and must be within the agreed specification. 4.8.11 Plastic Ball Impact Test Both at ambient and “cold” conditions, a 286g (10oz.) heavy steel ball is dropped against the closure at various angles from a height of 762mm (30in). None of the closures may release or chip under both conditions. 4.8.12 Drop Test Both at ambient and cold conditions, capped and filled bottles are dropped from a height of 1.5m (5ft). Bottles are dropped in the vertical and horizontal directions. None of the closures may come off during the test. Of course, all these tests are in addition to cap measurements and visual checks. The cost of setting up a quality control laboratory and the manpower required to run it should not be underestimated. Failing to constantly monitor cap quality, however, can result in shipment rejections and additional audits and must therefore be avoided.","@ID":49}, "NEWS 8 PETplanet Insider Vol. 17 No. 10/16 petpla.net Label Industry Global Awards 2016 The winners of the 2016 Label Industry Global Awards were announced at a gala ceremony which took place after the opening day of Labelexpo Americas. Held at the Rosemont Theatre, Chicago, USA the awards recognize the notable achievements and commercial creativity of label industry manufacturers, suppliers and converters over the last twelve months. In addition to the Lifetime Achievement Award, paying tribute to Belmark’s Bruce Bell, three other category winners were unveiled. The Award for Innovation (for companies with over 300 employees) was presented to Jindal Films Americas for its development of Platinum Thermal. A white surface-printable polyolefin film, Platinum Thermal looks set to revolutionise thermal/bar code printing, replacing both coated and direct thermal substrates and thermal transfer ribbons in many thermal label applications. It is said to be one of the few ‘breakthroughs’ that come once every 20 years. Eshuis BV collected the Award for Innovation (for companies with less than 300 employees). Eshuis was requested by Coca-Cola to develop an industrial 3D bow label which, after a year and half of research and development, resulted in a threelayer bow which could be applied at 40,000 bottles per hour as a standard Coke wrap-around label (see photo). In association with Constantia Flexibles, more than 130 million labels were produced, divided over 21 different sizes of bow label. Dow Chemical Company received the Award for Sustainability for its Chemical Sustainability Tool initiative, designed to enable teams to quickly evaluate sustainability challenges and opportunities, document their thoughts and create an effective visual way of communicating the results. www.labelawards.com Krones acquires Trans-Market to strengthen process technology footprint in the U.S. The manufacturer of filling and packaging technology Krones has signed and completed the purchase of 80% of the business of Trans-Market Sales & Equipment Inc. Trans-Market is based in Tampa, Florida, USA and is a proven leader in providing process engineering and automation solutions for the liquid food industry. The company has revenues of approximately $30 million and has a workforce of more than 50 employees. The previous owners of Trans-Market will retain a 20% ownership. Krones is financing the acquisition with available funds.This acquisition is regarded as a further step in the implementation of Krones’ strategy to build-up local engineering and sourcing capabilities. By acquiring Trans-Market, Krones enhances its process technology capabilities in the U.S. and expands its geographical footprint in North America. Besides Tampa, Florida, Trans-Market operates two locations in Texas. Together with the capabilities of Trans-Market Krones can offer its customers in the liquid food segment in North America the complete product portfolio ranging from process technology solutions, filling and packing equipment to logistical solutions, thereby covering the entire plant of its customers. Trans-Market will be part of the “Machines and Lines for beverage production/Process Technology” segment. The headquarters and management of Trans-Market will remain in Tampa, Florida. www.krones.com Erratum In issue 09/2016 incorrect subheadings were given in the market survey on pages 41-43. The market survey was about bottle-to-bottle recycling plants. In the survey the questions related to three different types of converting: bottle to granulate, flakes to granulate and bottles to flakes. The first subheading “bottle to granulate” is shown, the next one should have been “flakes to granulate” in line 14, and “bottle to flakes” in line 23. The lines 14 and 23 contained just the word “question”. This was an error, for which we apologise to our readers. You will find the corrected version online.","@ID":10}, "PREFORM PRODUCTION 22 PETplanet Insider Vol. 17 No. 10/16 petpla.net SPONSORS The China Road Show Injection moulds made in Guangzhou By Kay Barton August 10, 2016, Guangzhou Huayan Precision Machinery Co., Ltd. We met: Mr Kenneth Yao, General Manager Sales Mr Simon Chen, Project Engineer Kenneth Yao, General Manager Sales, who I interviewed as part of the China Road Show, has been part of the team since 2007. In the late 1990s, before joining Huayan, he worked for SinoChem China, the state-owned chemical materials import and export company, and then at Husky Injection Molding. His market expertise and differentiation is appropriately extensive. “At SinoChem China, which bought KraussMaffei at the start of the year, I was responsible for selling the imported rigid plastic injection materials to the customers in Guangdong,” Yao explains. “At that time, it was the only company that was authorised to import plastics. China’s domestic plastics industry was very small back then; 95% of all chemical materials were imported.” Huayan itself occupies a 38,000m² site and employs approximately 580 members of staff. In addition to injection moulding machines for the manufacturing of preforms and closures, preform moulds with 6-144 cavities and removal robots are also developed and built here. “Many of our moulds are used on Husky and KraussMaffei equipment, as well as on our own – a total of around 180 machines, currently, mainly in the area of 72-128 cavities. We also supply bottle blow moulds and hot runner components,” Yao says. We talked about the Chinese beverage packaging market and discussed C’estbon, the water bottling firm from Shenzhen, who I have also interviewed. Yao informed me that almost 80% of their preform supplies are moulded using Huayan equipment. During the subsequent tour of the plant, I saw once again a new 12 cavities HY-F250 injection moulding machine that manufactures 300g performs for 5 gallon for a Turkish customer. Huayan demonstrated it at the Chinaplas 2015 trade show (PETplanet Insider 07+08/15). “Our sales ratio is evenly balanced between machines and moulds,” Yao says. “In 2015, our turnover was roughly US$80 million, which was equivalent to approximately 20,000 cavities and 80 machines.” Around 20% of Huayan’s turnover is accounted for by exports to South East Asia. “Strong growth of 30%, which was the reality for us just a few years ago, has more or less stagnated since 2013. We are currently considering cooperations with companies in Europe and the USA, with the intention of entering the mould manufacturing markets there.” www.gzhuayan.com Kenneth Yao, General Manager Sales With around 600 of an estimated 1,100-1,200 PET preform injection moulding machines in the Chinese market, machinery and mould manufacturer Guangzhou Huayan Precision Machinery has a 55% market share. The development and manufacturing divisions of the company, which was founded in 2002, are situated at the Zengcheng Industrial Estate in Guangzhou. It originated in the Guangzhou Machinery Research Institute, which specialised in mould making for and servicing of ASB and Aoki PET machines from 1990 until 1996. In 1996 the founders left the Institute and founded Rijing, with the intention of manufacturing PET bottle blowing machines. In 2002 Rijing was sold and became the basis of a new company, which we know today as Tech-Long, a bottling line manufacturer. The current Huayan identity was registered in 2002.","@ID":24}, "Hong Kong Chongqing Xi'an Taiyuan Shenyang Qingdao Nanjing Guangzhou Shanghai Beijing Jinan Sponsors The China Road Show The worldwide round trip with www.china.petpla.net 2016 is both the Year of the Monkey in Chinese astrology and the occasion of our first Editourmobil quest to sample the far-eastern culture of China. Our China Road Show Tour into the Middle Kingdom successfully began in Shanghai in April. Since then we have met many interesting PET companies, both machine and equipment suppliers and their bottling partners and customers. All the interviews with the people we met - and the travel experiences we have had so far - can be read along with photo material at our Editourblog at www.china.petpla.net The first interviews with the leading players in the market have already been published in PETplanet Insider and there are many more yet to come! We still have some way to go until we reach the China Brew China Beverage exhibition in Shanghai. There, we will be showcasing our Chinese Editourmobil, along with information about all companies that we have visited along the way. We look forward to our last stage of the Tour and to meeting you during China Brew China Beverage, October 11-14, 2016 in hall W2, booth no. 2Y445. Come and join us on an incredible exploration of the Chinese PET market! As the saying goes: (A journey of a thousand miles begins with a single step). April – October 2016 Meet us at China Brew China Beverage, October 11-14, 2016 Hall W2, Booth no. 2Y445","@ID":41}, "LABELLING 60 PETplanet Insider Vol. 17 No. 10/16 petpla.net CCL’s Ecostream facilitates contaminant-free PET bottle-to-bottle recycling Without leaving traces Pressure Sensitive Labels are continuing their advance in the beverage market. The main advantages claimed for them are a premium appearance, wider design possibilities than other labelling methods, and optimised application and performance. CCL Label has sought to complement these characteristics with the development of new technologies that are intended to ensure a smooth post-consumption recovery and recycling process for containers and decoration. In addition to its innovative WashOff Labels for returnable glass bottles, CCL has already implemented a successful technology for one-way glass bottles with Eco-Emballage in France. EcoStream, CCL’s latest development in labelling technology, was developed with the intention of maximising the efficiency and facility of bottle-to-bottle recycling for PET containers with self-adhesive premium decoration. It enables the advantages of pressure sensitive labels to be utilised without being restricted by concerns over contamination from inks, adhesive or the label material itself. What CCL has done is to create a low-density label construction that makes the recycling of PET container and decoration much easier and more efficient. Easy, residue-free separation The EcoStream labels shrink in hot washing baths and detach from the PET material without leaving traces of ink or adhesive behind. While the label flakes float to the surface, the PET flakes sink, making separation of materials much easier. As the inks and adhesives stay on the labels, neither the washing bath nor the recovered PET are contaminated or discoloured. CCL says that EcoStream labels meet the critical guidance of the two leading recycling associations: namely, EPBP (Europe) and APR (U.S.). Because the low-density material is cleanly separated from the PET flakes, valuable raw materials can be returned seamlessly into the recycling stream, ensuring complete reuse. The EcoStream technology thus helps to maximise both the yield and the quality of the B2B recycling stream. Intrinsic & Extrinsic Values Besides being beneficial to the recycling process, EcoStream labels offer the widest design possibilities currently available. CCL says that all types of labelling can be accommodated, whether clear or opaque, with special inks or varnishes. In order to guarantee reliable functionality CCL sought and achieved approvals from the recycling associations for an extended range, named EcoStream+, which features additional varnishes. These new developments support brand owner objectives and help them to meet the higher recycling requirements from the food & beverage industry and from legislative authorities. CCL maintains that these developments will help producers and bottlers in segments like premium water and juice & soft drinks to re-invent their market presence, while at the same time meeting recycling obligations without any restrictions on POS or consumer convenience. CCL says, that, in summary, EcoStream labels represent a “great leap forward” from an ecological, visual and operational perspective. The technology has already been favourably received by a number of leading beverage companies. www.ccllabel.com","@ID":62}, "LABELLING 52 PETplanet Insider Vol. 17 No. 10/16 petpla.net Growing in both importance and sustainability The labelling of PET bottles today and tomorrow Author: Raffaele Pace, Labelling Product Manager, Sidel Research indicates that consumers take only an average of around three to seven seconds to pick their drink of choice from the shelves of our supermarkets. Admittedly this choice will often be influenced by the consumer’s past experiences and consumption habits. However, in those instances where a shopper is looking to make a spontaneous choice, the packaging plays a significant role - and labelling today is an area of growing importance in the overall bottling of liquids. No longer just a label Years ago, the bottle label was simply a vehicle for carrying the beverage or product name, a little corporate branding - usually in the form of a namestyle - and the minimal product information that was required by law. Typically this would be the content’s minimum volume and its ingredients. In today’s sophisticated marketplace however, much greater emphasis is placed upon the label and its marketing value as an important interface with the consumer. It is now recognised as a fundamental marketing element that helps establish and build brand awareness among potential customers. A label design that is striking and memorable will place its brand firmly in the memory of the customer and reinforce its position in a very competitive marketplace. Greater demands are also being made on beverage labelling by legislated standards, as producers are required to give more detailed information on bottles. However, the design aesthetics, the promotional appeal and the necessary consumer data are no longer the only defining criteria for the finished label. Sustainability and lower costs In common with most manufacturing industries, the beverage industry is naturally looking to cut its operating costs in order to minimise overheads and maximise profits in a changing and challenging marketplace. The beverage producers are looking to increase the efficiency of their production lines, focusing these days on the overall TCO (total cost of ownership) of all their equipment. They are also striving to reduce power consumption and maintenance costs, and to cut the use of raw materials and all other resources used throughout the production process. As well as simply reducing the corresponding overhead costs, producers are also responding to consumer demand. For some time now, in order to protect the world’s diminishing natural resources, consumers have grown more vocal in their demands for greater sustainability in our manufacturing processes. This naturally applies to the labelling of our beverages as it does to other parts of their production. Reducing power consumption and keeping the use of raw materials and all other resources to an absolute minimum is therefore a ‘win/win’ situation for the beverage producer. Rollfed label solutions offer physical and aesthetic benefits As well as being easy and practical to transport, handle and use, beverage producers want packaging to Raffaele Pace, Labelling Product Manager, Sidel","@ID":54}, "BOTTLING / FILLING 35 PETplanet Insider Vol. 17 No. 10/16 petpla.net Netherlands. The proprietary brands include both “Watsons Water” and “Cool Water”. The Hong Kong plant manufactures 14 sizes of bottles on five production lines, from 280ml to 18.9l. In Guangzhou, 13 production lines manufacture 15 sizes, from 250ml to 18l (juices, cold-aseptic), and in Beijing, three lines manufacture 400ml, 600ml and 18.9l containers. “These days, the water is filtered first and distilled afterwards,” explains Kim Siu. “As was originally the case, the idea is to return the water to its original, pure H 2 O state, as it exists naturally.” The raw material source is the same for all three plants: the city’s water supply. “It isn’t so much the water that we sell, but the many different services with which we refine and treat it to make it pure and safe,” Siu continues. “At the same time, we aim to be as environmentally friendly as possible.” In line with this objective, the company not only informs the general public of the correct recycling procedures in specific information programs; it has also created the necessary infrastructure for the collection of PET and other plastic bottles at over 220 of the Watson’s retail outlets in Hong Kong. “In 2015 we introduced the use of 100% rPET for Watsons Water bottles,” he informs us. Watsons Water is the first bottler in Asia to have launched such a concept. The material collected is used for the 280ml, 430ml and 800ml bottles. Recycled material for the purchased preforms (30 to 45mm neck finish) comes from Taiwan, Siu told us. They are currently testing the possibilities for changing the labelling into PET as well. For now, Watsons Water has added a seam to the labels to enable its straightforward, separate recycling. The bottling company offers the water itself in two PET product lines, each with different coloured sealing caps: green for purified water, and blue for water with added minerals. The distinctive bottle design was launched in 2002, has gained international acclaim and won several different prizes. In addition to the bottle shape, the packaging has a double cap, which includes the standard HDPE closure with a PP screw cap over it. This serves both the visual appearance and the hygienic safety, as the whole of the neck area of the bottle and the actual internal screw cap are protected from external influences until the initial opening of the exterior cap. For many years, Watsons Water operated solely as a manufacturer for own brands and private labels. It has subsequently completed a strategic realignment and has begun working more strongly with co-packers, in order to be able to focus more intently on product development. It manufactures and distributes two well-known brands in Hong Kong and China - Mr. Juicy and Sunkist - which cover various beverage categories. Distribution of imported labels is also gaining in importance. The company currently manages local sales for Italy’s famous “San Benedetto” water and “if” coconut water from Thailand. When it comes to water, Watsons Water’s main competition is Bonaqua. “In terms of our brand awareness, preferences and consumptions, our analysis shows we are ahead of Bonaqua but, in terms of retail off-take scan sales data, we are in second place,” Siu says. The Hong Kong location is home to two main units: one for regular bottles and one for the carboy water market – a segment in which Watson’s figures show it to be the market leader by a long way. “Our share in carboy water market is very high; we believe that it is between 60 and 70% in Hong Kong. In mainland China, our business in that segment isn’t especially high but we do have a strong soda water business there – something that is pretty much non-existent in Hong Kong. In China, it is hard to compete with the local suppliers of still water.” Regarding current consumer behaviour, Siu observes that: “On the whole, sales of water are increasing all the time, as people are moving away from CSDs, fruit juice and tea to water, both in Hong Kong and in China.” www.aswatson.com","@ID":37}, "TRADE SHOW PREVIEW 86 PETplanet Insider Vol. 17 No. 10/16 petpla.net Bundled expertise on PET recycling Austria’s Starlinger emphasises the fact that PET is the only plastic material that can be recycled into high-quality form for reuse. At this year’s K Show, the company will be focusing on PET treatment and the processing of rPET in new and innovative packaging solutions. Starlinger says that it has, over the past two decades, acquired a great deal of knowledge and expertise relating to PET, and that these resources have enabled it to develop new packaging applications for both PET and rPET. contact, while increasing the intrinsic viscosity (IV) of the material. viscoSheet lines produce sheet from up to 100% rPET, including flakes from production waste, skeleton waste or edge trims. Along with the viscoStar SSP reactor, individual components of the viscoSheet line such as calender and winder will be on display. A sack for every purpose The AD*Star sack, which was first launched in 1995, now serves markets across the building, chemical, agricultural and food product industries. Starlinger produces over 7.5 billion AD*Star sacks each year. The blockbottom valve sacks, which are made of coated PP tape fabric, are a safe and – according to a recent life-cycle study – environment-friendly means of packaging for dry bulk goods such as cement, gypsum, chemicals, flour, rice or sugar. AD*Star sacks can be produced with valve or open mouth, BOPP coated, as the small and easily-handled AD*Star *mini sack, as the AD*Star *carry sack, which is equipped with welded-on handles, or even as a shopping bag. Another packaging product, the IC*Star sack, is welded at the bottom, rather than sewn. This new process makes for a stronger sack bottom as well as delivering material savings and lower maintenance during production. Starlinger will be showing for the first time how the integration of the latest information and communications technology - Industry 4.0: the ‘Internet of Things’ - into woven sack production can be realized. Focus on film recycling – and two world premieres Starlinger recycling technology will be showing a recoStar dynamic recycling line in operation, reprocessing heavily printed in-house film waste. The Smart feeder, one of the line’s most important components, features automatic temperature control that makes it possible to achieve uniform high product quality even when processing materials with varying moisture levels and fluctuating bulk density. The company will be presenting two world “firsts”: new technology for processing polyester, and a pioneering process for refinement of pellet material. As well as recycling technology in hall 9 stand D21, Starlinger will be showcasing textile packaging viscotec in hall16 on stand B47. In-house exhibition The latest technological developments in the fields of woven sack production and plastics reprocessing will be available for viewing at the inhouse exhibition on Starlinger’s premises at Weissenbach/Triesting, to be held from October 17-19 and 24-28. www.starlinger.com From PET bottle to high-performance fabric Since its presentation of the world’s first flexible intermediate bulk container (FIBC) made of 10% woven PET at K 2013, Starlinger textile packaging has developed proprietary technology for the production of woven tape fabric made of up to 100% rPET flakes. As the physical properties of rPET match those of virgin material, fabric woven from rPET has exceptionally high tensile strength coupled with a high creep modulus. It is very resistant and retains shape stability over a long period of time, even under the effects of load and temperature exposure – advantages that make it the material of choice for a wide range of new applications. PET fabric that is food-safe and suitable for attractive designs is also appropriate for packaging food products and consumer goods. Starlinger will be showing, for the first time, a “PET pet food sack” at K – a sack for dog food made of 100% rPET flakes. The pinch-bottom sack from the PP*Star product family consists of rPET tape fabric laminated with printed OPET film, which provides all the necessary barrier properties for the safe packaging of sensitive contents, such as dog food or fertilizer. Also in keeping with the focus on PET are the viscoStar SSP reactor and the viscoSheet line from Starlinger viscotec. With the viscoStar SSP reactor, PET pellets or flakes are decontaminated and rendered suitable for use in applications with food Starlinger & Co. Ges.m.b.H Recycling technology Hall 9 Booth D21","@ID":88}]}}
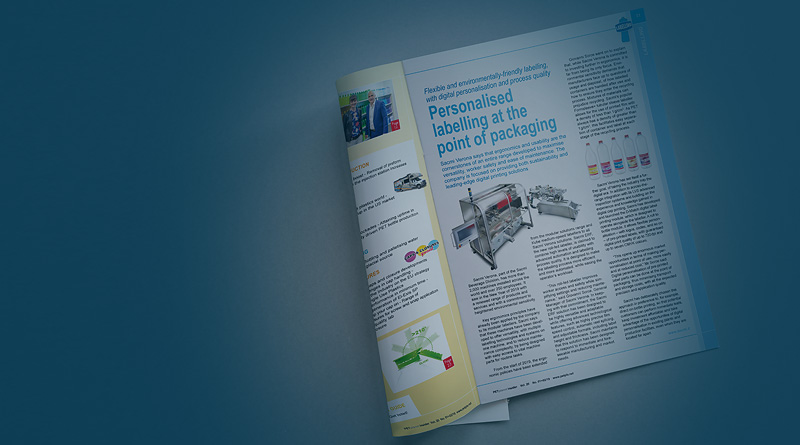