Water filling in 100% rPET
Bottles: recycled, produced, filled and shipped in a real cycle
On the most northerly part of our tour we met Sandy Gott of Ice River Spring in Feversham, Ontario. She told us the amazing story of her family-owned business which is the only beverage company in North America operating their own recycling facility, self-manufacturing their bottles out of 100% recycled post-consumer packaging.
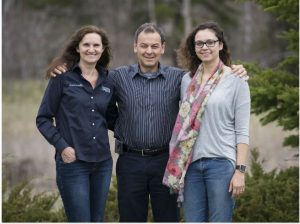
As an introduction let me tell you some impressive hard facts: Ice River Spring has six plants for bottle producing and filling and one recycling plant in Canada. In the US there are five manufacturing plants. Each factory occupies roughly 100,000-600,000 square feet. Here in Feversham, the largest plant, they have six Husky preform machines as well as capping manufacturing equipment from the same company. Two Starlinger lines and a number of Krones machines for bottling, filling and packaging. We also recognised Sidel and IMDvista equipment. Every day they ship around 100 loads from this facility.
We asked Sandy about how the idea to create this very successful business came about and the challenges that had to be faced:
Sandy and her husband Jamie Gott founded the company in 1995, and two of their three children and other members of the family have also joined the business. Sandy also told us about their second business; they are organic farmers and originally their aim was to protect water sources.
“We had a property with clean spring water, so we started selling tanker loads of water from our spring to bottlers in Toronto. Then we thought, why don’t we bottle the water ourselves? So Jamie built our first line in a 5,000 square feet bottling plant and it just grew from there.” The business model was easy, as it was focused exclusively on private label business. For the consumer that means having an alternative healthy beverage on the go. And the timing was good: “Here in Feversham we have the largest plant with about 600,000 square feet; there is a 5 km pipeline from our spring to the plant to limit the truck traffic. We expanded first in the West of Canada then in the US. At the moment we have six bottling plants in Canada and five in the US. Our recycling facility is located in Shelburne, Ontario. Caps collected from the recycling line are used at our sister company CRP Products to make outdoor furniture. All of our bottling plants are zero waste to landfill.”
With an annual growth rate of 6-8% in the bottled water industry, especially in the private label sector, Ice River Spring has enjoyed continuing growth because consumers are really looking for a healthy beverage option.
“This facility was built in 2000 and we added to it every year until completion in 2005. In the first five years of business we doubled our turnover every year. So we decided to build up a network across Canada to cut delivery times and to service the various regions more effectively. We have 800 team members in total and this increases enormously every year. Here we have Husky machines for preform injection, a number of machines for half litre and four litre bottles, 1.5 l bottles and the 15 l bottles. To give the complete overview: we have 6 preform machines in total, the Husky Hypet 500-144 cavity, and Hypet 400-96 cavity from Husky. The cap machinery is the Husky 6 Hylectric 300-72 cavity and Husky 10 Hylectric 300-96 cavity.”
Sandy continues: “We have invested significantly in light weighting our product. When we started, our bottle weighed in at 20 g now it’s 8.5 g. It was at this point that we contacted Husky with a view to injecting our own preforms and producing our own bottles, and we also began injecting our own caps. We were sensitive to consumer concern about plastic in landfill and we start to think about what we could do to reduce our carbon footprint?”
Ice River Spring tried two different options: “Initially we went with an aseptic packaging line which was paper based and learned very quickly that this is very difficult to recycle. We also worked with PLA resin but this was incapable of maintaining the integrity of a 2 year shelf life. We then began experimenting with recycled material and started to include it in our products, first 25% than 50%“.
Almost everyone in the bottle business told them that a 100% rPET bottle was impossible, but Jamie and his team went ahead anyway and succeeded. “In 2008-2009 Amut and Starlinger could produce food grade recycled plastic on their lines. We decided to build our own recycling plant in Shelburne, Ontario. We installed Amut sortation equipment and 2 Starlinger purification unit lines, a Star 1 reco-Star PET 165 iV+ and Star 2 recoStar PET 165 HC iV+. From the blue box from Ontario (the Provinces’ recycling system) only 16% was PET, the rest was other plastics. We buy 85% of the PET plastics collected in the blue box in Ontario, and that was about right. We have created a steady demand for material, and this was important because previously it was not possible as waste plastic was shipped to China whenever domestic demand was low. With our own recycling plant we now have a total closed loop business.”
Ice River Spring gave their consumers a real option: bottled water produced with a very low carbon footprint. “It is much more environmentally friendly because all bottles in every location in Canada are 100% rPET, from half litre and also the bigger 15 l bottle; we ship our rPET to all our plants in western Canada. In the US not yet every one of our partners is working 100%, but we are working on converting them. For private label producers, they now have the opportunity to advertise 100% rPET bottles and that is the best advertising.”
“We do two different colours for the 100% rPET bottles, blue for most of our private label customers, and the green, recovered from the green PET in the stream, we use for our own brand. Ice River is sold exclusively in Canada in a green bottle. At the moment we are having to buy more green flakes to meet consumer demand for our product.”
Sandy sees further growth on the recycling plastics side: “More of our US customers are converted to use rPET, and we are going to need a bigger supply and this will mean adding another recycling plant elsewhere in North America. The challenge here is to put it in a region where you have access to a consistent supply of material!”
Sandy had one final comment to add: our main driver is to be the trusted provider of healthy beverages through innovative and responsible methods. We want to redefine bottled water and give consumers a sustainable option they can feel good about. We believe that closed loop business models will encourage other manufacturers and brand owners to do the same.