Get connected
Co-injection for absolute flexibility
Kortec (now Milacron Co-injection) is a leading supplier of co-injection solutions to the plastics and especially packaging Industries. The company’s systems are used to produce high-barrier multi-layer containers featuring three-layer construction that optimises clarity and strength while maximising the shelf-life of the end-use products. PETplanet talked to Mr. Oliver Lindenberg, President Mold-Masters Americas, Ms. Cheryl Sayer, Director of Engineering about their systems and future developments in the plastic packaging industry.
PETplanet: When and why was Kortec or Co-Injection Milacron founded? What was the decisive point of this system to market?
Milacron: After almost 20 years of developing technology for plastic packaging by Kortec, Milacron decided to acquire this compelling technology and technologically driven company (first system shipped in 1999) to complete our offering to the injection world and pursue a growing and wide range of opportunities.
PETplanet: How has this brand developed under the Milacron umbrella since its inception?
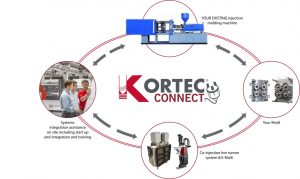
Milacron: We have integrated Kortec under Mold-Masters, as co-injection is the knowledge of the melt distribution of the different melt layers (process) and the molding process, which is the core competency of Mold-Masters. Mold-Masters has over 50 years of knowledge and expertise with our hot runner and controller history to drive this technology to the next level, enter new markets and enable our customers to differentiate and be prepared for the future.
PETplanet: Where do you see particularly lucrative future markets for this system?
Milacron: The market drivers are part cost reduction, product differentiation, sustainability and increased shelf life and the percentage of injected scrap material, which can be added to reduce virgin plastic consumption. The main markets as of today are single serve coffee capsules, where we are the market leader, as well as in pet food containers with approximately 30-40B units, and general canned food, like soups, veggies with 80+ bill units, with our Klear Can co-injection solution as well as the beverage closure market.
PETplanet: Where and how is the co-injection system used?
Milacron: Co-injection is the simultaneous injection of two materials. Material A is the skin and Materials B is the core, where the core B is fully encapsulated by the skin A. Because they are injected simultaneously so there is no cycle time penalty. Co-injection is used typically to introduce a barrier, for example, to block transmission of CO2, O2, light. But it can also be used for introducing a high-volume low-cost core (PCR), mechanical advantages (injecting a core material of a different durometer) for a sealing application, and for the aesthetics for on the shelf differentiation.
PETplanet: What are the key benefits of the system? (Especially for PET applications)?
Milacron: Milacron’s Kortec technology is the industry leader in barrier distribution and control. The system delivers excellent leading-edge control and barrier core weight control from shot to shot, run to run. It is world class due to its barrier distribution capabilities.
A monolayer machine can easily run as co-injection process with Kortec Connect. This enables the machine to be used for multiple purposes, one day it can be used for co-injection molding, the next day it can be used for monolayer molding. Because Kortec Connect enables customers to make better use of their existing assets; it is the most cost competitive entry to co-injection on the market!
PETplanet: How much weight is gained by the co-injection process e.g. saved in comparison to other multilayer preforms?
Milacron: Weight is not gained, in fact, since for example in a PET barrier application, the core material has 10 times better permeation rates than PET, the part is typically light-weighted with the introduction of a barrier layer.
Excellent distribution and control of the barrier layer allows us to accurately dose the barrier and place it where it is needed to minimise the use of the barrier material; which is typically more expensive than the skin material. It also allows the customer to light-weight the container knowing the barrier will be accurately distributed where you need it, to achieve the shelf life requirements for the application.
We are also seeing a lot of interest in co-injection for UV light blocking applications like in dairy applications (i.e. milk preform- and bottles). In this case we can replace an injection over inject system with a co-injection system and automatically double the cavitation yields since we will be injecting simultaneously. The Klear Can is another area where we are seeing a lot of interest with customers asking about different size cans to substitute the metal can by a clear plastic container (Klear Can), which is already in stores.
PETplanet: Recyclability is a big topic in the plastic and packaging industry. Where do you see future development?
Milacron: We see two big areas in the future: One is on material development and the other one is introduction of PCR due to the directives e.g. from the European Union.
Biodegradable skin and core materials are currently already being used in our systems. We are studying these materials and working with materials suppliers to test them, on customers’ specific applications. We are also working with the University of Massachusetts Lowell to see how these materials perform.
We are getting a lot of requests to co-inject a high core content of PCR into what would be normally a monolayer part. We have done this for industrial segment and showcased this at NPE a few years back. Now we are getting the same requests from packaging applications.
We believe the European directive is driving a lot of this. By 2030 all plastic packaging should be designed to be recyclable or reusable. By 2040 USA and Canada are proposing complete recyclability and/or recovery of plastic products. As a result we are getting a lot of requests for co-injecting large percentages of low-cost PCR. At the end we can reduce the consumption of virgin resin, by substituting it with recycled material, in the inner layer. This is fully supported with our technology and realized already. As an example, we have molded a 5 g pail, with 50% scrap material in the inner layer. Similarly we can apply this in packaging. PETplanet: Thank you very much.