Doubling capacity; one third less cycle time
We met: Kota Aoki, Director of Nissei ASB, Japan at ASB Thane
Nissei ASB Machine Co., Ltd., together with its wholly owned subsidiary of ASB International in India, has introduced an innovative “Zero Cooling” process in which cycle time in single-stage machines can be significantly reduced, whilst at the same time improving preform geometry and with it, quality. The company has also invested in two new factories that have more than doubled its manufacturing capacity in Japan and India over the past 12 months with the result that up to 700 machines could now leave its plants every year. However, the focus of this increased capacity is mould making where the goal is to reduce delivery times and raise the number of moulds produced to 1,500 per annum. We spoke to Kota Aoki, Director of Nissei ASB, Japan at the company’s Indian plant.
PETplanet: Mr Aoki. Can a two-fold increase in capacity in just one year be seen as beneficial? How will you utilise this additional capacity?
Mr Aoki: We have significantly increased our capacity both here and in Japan which is in response to the constant high demand for our single-stage machines. However, our emphasis is very much on mould making, which is an area where we want to improve delivery times and output. This, of course, will be driven by our new patented Zero Cooling technology.
PETplanet: You reduce cycle time and at the same time improve bottle quality?
Mr Aoki: Our main focus is on reducing the amount of cooling time in the injection moulding stage, hence the term “Zero Cooling”, enabling us to make thicker-walled preforms which ultimately results in better quality bottles.
PETplanet: Your machines are principally used for pharma, household, liquor and wide-mouthed bottles. Everything that is, apart from beverages. Do you want to use this new technology in the drinks sector?
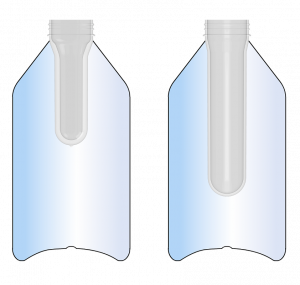
Mr Aoki: Our machines definitely have some beverage applications and I see some opportunity with the new technology in the drinks sector in the future. However, our current efforts for now will concentrate on the non-beverage areas you have already mentioned. Here, we also see great opportunities in moving from glass and PP to PET. Mould & process engineering will be our primary focus in the coming years.
PETplanet: And where would you want to sell your additional machine output?
Mr Aoki: It is noticeable that a lot of companies here which previously have only operated in India using our machines are now on the lookout for lucrative markets outside of the sub-continent, particularly in Africa, using proven technology from us of course. Many Indian firms have expanded overseas and established production facilities in the USA and elsewhere. Our machines are also used there.
PETplanet: In India, there is an anti-dumping tax on preform machines (injection-moulding) coming from China. Does this also apply to single-stage systems which also produce preforms?
Mr Aoki: No. This affects facilities that only produce preforms. However, I do not see any real competition here either. I have just come from China-plas where I saw exact replicas of our machines. These are purely mechanical duplicates – our cycle times and bottle quality cannot be achieved using replicas. Our mould making & processing expertise gives us a major advantage in this respect.
PETplanet: Which completes the circle again. Thank you Mr Aoki for sparing the time for this interview.