“The challenges for the plastics industry are varied”
In the run up to the K’ trade fair in Düsseldorf, excitement is in the air in the plastics industry. The topics of sustainable production and recycling are on everyone’s lips and they are high up on the K trade fair agenda this year. PETplanet spoke to Stefan Bock, CEO and founder of company ReduPET GmbH and an old hand in the field of blow moulding and preform injection moulding. He shared his strategy for conscious production and discussed the future challenges for the PET sector.
PETplanet: You have worked in the plastics industry for over 30 years. Plastic has never before been so controversially discussed in society. What do you make of this discussion? Are there aspects that you think are being missed?

Stefan Bock: The current discussion is crucial to the survival of the plastics industry. Of course, we all know that we cannot continue like this with a material that is so important to our living standards. This means that the pressure building up from the current discussions is a driver for rethinking the industry and becoming more innovative and responsible. First and foremost I think what is missing is legislators in more countries adopting sensible and well thought out laws. For example, as far as I know, plastic waste from Germany is exported by ship. Once the plastic is loaded onto the ship, it is considered in Germany to be recycled, even if it is then disposed of improperly in Asia.
The consumers themselves must have a much greater awareness of plastic as a recyclable material and act accordingly, whether voluntarily or through incentives or legal enforcement. There is a clear need for global action here.
PETplanet: In your opinion, what does this discussion hold in terms of effects on the plastics industry and the PET industry in particular?
Stefan Bock: Plastic is regarded more critically and so is receiving significantly more attention and is unfortunately getting a negative reputation. This pulls plastic products into the focus and calls them into question, which is surely a positive effect. Basically, awareness is being raised around the world; it is just a shame that this is often done in a sensational and therefore media-attracting way instead of it being constructively explained and handled. This is urgently needed – wake up calls are no longer enough.
Especially in my sector, the beverage industry, we can see that containers have become increasingly “convenient”, i.e. smaller. This means that more and more plastic is used. This also happens in hot countries, where these small packages bear no relation to people’s needs. Meanwhile, packages are so small – and therefore so large in proportion to their content – that they now have to have a multilayer construction to increase the barrier effect. This means that the valuable recyclable PET material is now contaminated with an incompatible barrier material and this makes recycling much more difficult. Surely it would be more appropriate to divert discussion to these absurd developments that are no longer in keeping with the times and to ask ourselves why the EU is clutching at plastic straws – in the face of these absurdities.
PETplanet: You founded ReduPET GmbH two years ago. What was the deciding reason for this?
Stefan Bock: As you said, I have been working in the plastics industry for over 30 years, primarily in the packaging industry. Most of the time, I was employed in engineering but I was also able to make a contribution around the world in production operations for different applications and in different cultures and to get to know and assess these. Because of mass production, the plastic industry is extremely resource intensive in terms of both energy and raw materials. As already mentioned, the industry works with narrow margins, meaning that operating staff are not always well educated or do not have deeply held expertise to understand the processes in great detail – robust production with good products is the objective. Often, it is not recognised that the machines are not running efficiently and both raw materials and energy are wasted unknowingly in huge quantities.
Once I had settled on the idea of acting in a resource-friendly way in my own environment, especially at home, I could see in my work environment a much greater potential and also therefore the responsibility to support the plastic processing industry in saving energy and raw material resources.
At that time, I was not in a position to act upon these convictions and put them into reality. However, with greater experience, my global network and my innovative efforts, I was encouraged to take action and so I founded ReduPET GmbH.
PETplanet: Have you achieved your ambitious objectives from that time?
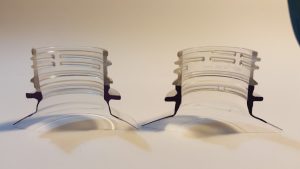
Stefan Bock: My activities were divided into two focal points. I started by writing down all of my experiences in a logical and practical way so that I could work out practicable solutions for conserving resources. These were documented and translated into several languages. I then presented these to the PET processor industry as a package, whereby their operational employees could do a workshop and together work out the potential new measures that they could adopt in their production facilities. I would be on hand as a consultant throughout implementation so that these projects did not grind to a halt. This works well in the processing industry because it is realistic, understandable for all participants and the measures always lead to a noticeable success. My customers and I are very happy with this development.
I brought to market maturity the material saving innovations Mint-Tec and Neck-Lite in partnership with company CPS (Creative Packaging Solution) as holder of the patents. Even when we have experienced enormous support, as experienced with the blow moulding machine manufacturers, the market reaction is very varied. Drinks manufacturers in particular, who are among world market leaders, are especially taken with the technologies. Some have already issued market releases for their products. The technologies Mint-Tec and Neck-Lite are revolutionary and provide a bridge between established injection moulding and blow moulding – therefore calling into question the previous interaction of these technologies. And this is all kept relatively far away from the end customer. There are some hurdles to overcome as acceptance is not easy to obtain and each individual wants to benefit from a technology like this. Without profit, interest is usually almost nothing. This is why CPS has been working on this development for over seven years and has brought in enormous resources in terms of finance and time. ReduPET GmbH is doing this in the same style to guarantee longevity. Of course, motivation comes from our successes. Today, we are very proud that Mint-Tec is now running industrially.
PETplanet: With ReduPET GmbH, you are trying, for example in the product process for preforms, to save up to 8% of material consumption and costs; at the base of the bottle it is up to almost 20%. What kind of technology is behind this? What are Mint-Tec and Neck-Lite all about?
Stefan Bock: Mint-Tec and Neck-Lite are two material-saving innovations for PET bottles. In the manufacturing of a PET bottle, two processes usually come into play – injection moulding and stretch-blowing. However, the two processes do not fit optimally together, as each is subject to the laws of physics. In the injection moulding process, the preform is manufactured. This preform is then reheated in a further process and stretch blown into the finished bottle, where the plastic undergoes high-grade hardening. To achieve optimum hardening, the preform would have to demonstrate a geometry which cannot be manufactured purely through injection moulding technology. For example, the preform base would have to demonstrate a much lower wall strength to enable the optimal stretch blowing of the subsequent bottle base. But this is not possible with injection moulding. With thin walls, the material would freeze too quickly and the unavoidable shrinking process caused by cooling, primarily in the seal area, could no longer be compensated.
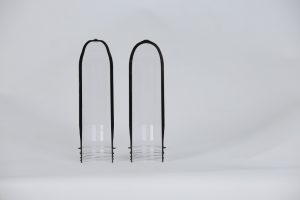
This would result in leaky bottles. By contrast, the blowing machine is not really capable of stretching out the material accumulation in the base to a satisfactory level. So the material remains unnecessarily in the base area of the bottle – a not inconsiderable waste. If you cut the bases off PET bottles in the supermarket, this waste can more or less be observed on almost all bottles. It must also be noted that the blowing process benefits a great deal from the light base. It enables a blowing machine to produce products more quickly with lower energy consumption in the heater oven. The shorter cooling time in the base enables a faster production run. The blowing pressure can also be reduced, as the base can now be formed more gently, which means another significant energy saving.

The same idea is the basis of the Neck-Lite innovation. In the neck area, beneath the transport ring, the melt channel is shaped in a way that is just as unnecessarily thickened, so that the PET material does not freeze too quickly and the shrinkage, again caused by the cooling process, can also be counteracted. The idea here is to leave only small channels to supply the compensating material at the neck during the shrinking process, while the rest of the material can be omitted. This leads not only to a material saving but also the blowing process requires significantly less energy for the reheating process before the stretch blowing – the smaller mass of PET material can be heated much more easily. A side effect is that Neck-Lite is visible at the bottle neck and can therefore be advantageous from a marketing perspective.
PETplanet: Where do you see development opportunities for ReduPET GmbH?
Stefan Bock: The training sessions and system evaluations are currently establishing themselves well on the market. Practical specialised training sessions for production staff are more in demand than I expected. This also applies to refresher courses. This is definitely because the efforts pay off in many ways in production. Furthermore, we are also active in implementing individual measures for system optimisation, working closely with component manufacturers for these systems and thus developing innovative technical approaches.
The main focus however is Mint-Tec and Neck-Lite. We are convinced that with the ongoing discussions about plastics among processers and through the pressure on legislators and machine manufacturers, innovations like these will be implemented. The PET bottle is a plastic product that hardly any other product can replace. But we must deal with the PET bottle more responsibly. And it is exactly here that ReduPET GmbH can offer further development opportunities, when we take on this responsibility.
PETplanet: In your opinion, what are the greatest challenges for the plastics industry over the next ten years or so?
Stefan Bock: Plastics are generally better than their reputation. The main problem is that they are not always in the right place, or are used wastefully or not in the right composition. After fulfilling their task, they are seldom seen as recyclable, i.e. as an important resource. And this is precisely where the tasks of the plastics industry lie in the next ten years. But I am convinced that here too, global legislators have a great responsibility and task to tackle. Because the plastics industry, and primarily the packaging industry, lives on low margins but on mass production, it is comparatively sluggish and inflexible in terms of changes to products or processes through innovation. As changes are almost always very cost intensive, there must be reconsideration to avoid the risks that are hindering the plastics industry. This is why new guiding principles and support measures applied by legislators to whole countries are so important.
Unnecessary, resource-guzzling products must disappear from the market and the focus must be on guiding the material flows to after use and recycling. In my opinion, the focus doesn’t necessarily have to be on making plastic available again at the same quality level, as this also brings up the question on whether premium recycling also has a negative impact on the environment.
It is also the responsibility of the suppliers of production systems to be encouraged to supply systems that take all of this into consideration and reflect on the future in a holistic and responsible way. Often, high-performance systems are delivered to developing countries with great pride, possibly even in exchange for financial incentives. But these high-performance systems ultimately produce rubbish on a grand scale, such as single use ice cream spoons – individually wrapped in foil – and the receiving country simply cannot deal with this. And it is here that there is little consideration.
In short, for the next ten years, the challenges for the plastics industry are very varied, not only in our own back yard but globally.