Circularity and innovation – Shaping the future of PET
Petcore Europe Conference February 2020
Circularity and innovation – Shaping the future of PET
Each year the European PET value chain meets in Brussels for the annual Petcore Europe Conference. This year the two-day conference was held in Brussels to welcome more than 300 industry delegates. Under the theme “Circularity and Innovation – Shaping the future of PET”, the complete PET industry sector shared perspectives and strategies for a succesful and more circular future.
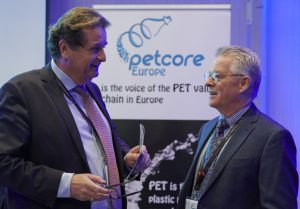
From PET resin producers, masterbatch producers, packaging designers and manufacturers, equipment manufacturers, label producers to major brand owners, EPR schemes, waste management organisations, recyclers, waste sorting and recycling machinery manufacturers – the entire value chain was represented. Additionally, speakers and participants from the European Commission, the European Parliament, the Ellen MacArthur Foundation and Eunomia shared their thoughts on the PET market as well as the plastics industry in the Circular Economy.
“Petcore Europe represents the entire PET value chain since 1993. The strength of the organisation is the engagement of over 90 participating member organisations working together on the circularity of PET through working groups and projects”, stated Stephen Short, President of Petcore Europe, when opening the conference. “This engagement of all members, in combination with Petcore Europe’s commitment to look for the entire sustainable packaging solution as a united industry, is a great value for all stakeholders involved. Petcore Europe’s growth over the past two years is remarkable, we could welcome over 50 new members”, added Christian Crépet, Executive Director of Petcore Europe.
Perspectives and strategy for the PET value chain
The focus of the first session was the current PET market. Andy Grant from Eunomia gave an overview of the PET collection and recycling rates for 2018/2019 as well as the key drivers of the market. According to Eunomia, significant improvements have been made in recycling processes and with the increasing quality of materials, rPET could reach as much as 55% of total PET demand by 2030. “A long-term trend shows overall growth in production and demand for PET, particularly in high viscosity PET”, Andy pointed out. According to Eunomia 3.4 mt of PET is placed on the market for PET bottles, 0.9 mt for PET trays.
Alessandra Funcia, Head of Sales and Marketing Sukano, presented Petcore Europe’s two major working groups: The WG PET Thermoforms Recycling and WG on Recycling of Opaque and Functional PET packaging (former ODR). Alessandra focused on design for recycling as well as solutions for the uptake of recycled material from PET trays and ODR packaging.
Sebastian Lemp, from Petcore Europe then focused on the need for the PET industry to communicate and showcase the (environmental) benefits of PET. Sebastian introduced some projects e.g. ZeLoop, the first circular economy rewarding plattform and strategies of other like-minded organisations and iniatives and concluded: “It’s time to work together and make the circularity of PET understood amongst policy makers and the public”.
In the second session of the first day, experts from the PET value chain gave strategic outlooks from the PET producers’, converters’ and recyclers’ point of view.
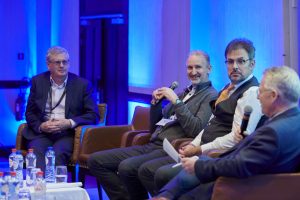
Steve Scott, Chairman of the Committee of PET Manufacturers Europe (CPME), addressed the PET market from the European PET producers’ perspective, providing his analysis of market developments as well as innovation and investment challenges. For 2020 3,466 kt PET will be produced. It is a growth of 0.9% according to 2019. The big players will be Indorama with 33%, Neo Group with 13%, JBF 11% and Alpek UK with 11% of PET production.
Nicolas Lorenz, from PACCOR, gave a converter’s vision for the future in his presentation, in which he focused on PET trays. The presentation showcased key areas for the future of PET and contained a strong message to the value chain: “We, the packaging manufacturers must work together to find out how packaging can be connected with the environment in the future.” He highlighted that the packaging of the future has to have the ability to communicate within the complete value chain but also with the new generation of consumers. For him the key lies in the digitalisation of packaging.
In the third presentation Casper van den Dungen, Plastics Recyclers Europe (PRE), gave a summary on what has changed in the past 12 months as well as an overview of the efforts needed to meet future recycling targets. To reach the targets of rPET production in 2025 a capacity of 520 kMT plus are needed and have to be manufactured in 20 new recycling plants. By comparing the current situation of already existing deposit systems and planned systems for 2025 there will be a lack of 420 kMT in PET collection. Casper concluded: “The PET bottle collection is the main development which needs to advance in reaching 77% collection target in 2025. New deposit bottle countries are planned until 2025 but more is needed. 520 kMT new bottles to bottler PET capacity is required, target 4-5 plants/year, new or upgrades. Standards are needed for both feedstock & rPET for mineral water or soft drinks.” The third and last session of the day focused on technical challenges for the PET industry. Marie-Catherine Coquin from Danone and Cesar Velilla from Nestlé Waters provided an overview of good practices for NIAS (non-intentionally added substances) evaluation and the work of the Petcore Europe Special Industry Group on PET NIAS (PING).
The second day of the conference started with the morning session focusing on “PET in the circular economy – a global perspective”. A significant highlight of the conference was the presentation by Rana Pant from the European Commission. Rana, Policy Officer at DG ENV focusing on the SUP Directive, gave a detailed overview of the SUP Directive and Essential Requirements in the PPWD. He insisted on an evaluation and follow-up of the new regulations by the European Commission as well as most likely an elaboration of a positive & negative recycling list.
Professor Kim Ragaert from the University of Ghent presented what is needed to make PET pots, tubs and trays roll down the bottles road into circular economy. Kim concluded her presentation by stating that bottle-grade PET made it to the posterchild of plastics recycling due to industry collaboration. PET trays have the same potential; with a few neat tricks provided by science it can follow the bottles into circular economy. After analysing the feedstock quantity, quality and collection, sorting, separation and pre-treatments polymer science to predict quality should be used.
Trends and solutions in PET collection and recycling
In the afternoon session of day two, the focus shifted to trends and solutions in the PET post-consumer collection and recycling. First, Wolfgang Ringel from Tomra gave an overview of the current state of Deposit Return Systems and it’s potential to grow. He was followed by Vincent Colard from Citeo, who spoke about the collection and sorting of ODR and PET trays in France and Citeo’s efforts to find circular solutions. Afterwards Gian de Belder from Procter & Gamble and Larry Logan from Digimarc presented the Holy Grail project on digital watermarks. Gian announced that several P&G brands will integrate digital watermarks with first shipments at the end of the year in Germany. To end this session, Nicolas Grotus from Pellenc ST gave an insightful presentation on Artificial Intelligence and its place in solving food and non-food as well as other sorting challenges.
The third session of the day focused on trends in PET trays recycling. Ana Fernandez, from Klöckner Pentaplast highlighted that “recycling PET thermoforms is the final step in closing the already successfull PET recycling loop”. Ana presented several projects that are working towards tray circularity. Afterwards, Mark Dawes from Dupont Teijin Films presented mono-material PET lidding flms and concluded that PET is a unique polymer that enables mono-material tray and lid solutions with high percentages of recycled content in direct food contact applications.
Trends in chemical or
back-to-monomer recycling
The last session of this year’s Petcore Europe Conference focused on monomer/enhanced recycling which was generally seen as one of the most important long-term solutions to make PET even more circular. Heike Fischer from PETplanet introduced and moderated the session in which Leela Dilkes-Hoffman from the Ellen MacArthur Foundation, Wim Hoenderdaal from Indorama Ventures Europe and Bruno Van Gompel from Coca-Cola presented their views on PET monomer recycling.
Leela described the recycling landscape: Prioritise where possible to preserving value. Mechanical recycling is a cost-effective form of recycling, but it can’t remove some additives and contaminants. There is a loss of material properties over time. The solvent based purification complements mechanical by removing additives. Material still has a decrease in average molecular weight over time. She stated: “There is a physical limit to how many times a polymer can go through that is why an “inner loop” is needed to complementary the outer loop.” She continued explaining the opportunities of depolymerisation:
This method helps to have more plastics circulate within the circular economy by complementing existing infrastructure acting as a ‘reset’ lever and allowing exchange of materials between different applications and value chains (e.g. textiles to packaging).
Leela concludes: “We can’t chemically recycle our way out of the plastic pollution crisis!” Depolymerisation needs to be developed as an integrated, not an independent solution. There is still a need of a systems perspective. It does not eliminate the role of design and is not a replacement but a complement to mechanical recycling as well as reuse and new delivery models.

Wim Hoenderdaal, Chairman of the PET Monomer Recycling Special Industry Group prepared ten most FAQs about PET monomer recycling. He started with the question: Which problems does PET monomer recycling solve? “With PET monomer recycling it is possible to recycle the hard to recyclable plastic which can now be transformed to the building blocks needed to create new, food-grade high quality polymer. Poor quality plastic packaging and other polyesters articles that are not currently recycled can be transformed and returned ‘as good as new’, not just once but again and again. PET monomer recycling in combination with mechanical recycling can make recycle contents of 70 to 80% feasible on a sustainable basis. It will also solve the waste problem: After all efforts from consumers and cost by the industry to collect and sort the plastic, we can give a guarantee that PET is recycled and not disappears afterwards in incineration or landfill.”
Another question Wim answered was: Is it competing with mechanical recycling or is it complementary? For Wim it should be no question that monomer recycling is always complementary. He went on that good quality feedstock can and should be recycled mechanically. “While Europe uses approx. 4.5 mio tonnes of PET for packaging, 50% might be good enough for mechanical recycling. Monomer recycling can recover the rest: coloured, opaque, multilayer, blends, thermoforms and other PET products (textiles).”
Bruno van Gompel explained the strategic direction of Coca-Cola towards a world without waste: Coca-Cola will remove unnecessary and hard-to-recycle single use packaging, will use 100% recycled and reusable content which is defined as a combination of mechanical, enhanced and plant-based PET to ensure a bottle made of no virgin fossil fuel based material. Coca-Cola is working to collect 100% of its packaging and is exploring refillable and packaging free delivery models. As an example Bruno introduced a 100% rPET bottle from Coca-Cola Sweden. Wim, Chairman of the PET Monomer Recycling Special Industry Group had the pleasure to announce that the first PET Monomer Recycling Forum 2020 will take place in Brussels very soon.