Flavoured milk in aseptic bottles
Amul has hit upon a new field for PET in India. It is filling PET bottles with 200 ml of flavoured milk. The market for aseptic packaging is booming. Amul already have three aseptic PET bottle filling lines, while a fourth line had been ordered to start production before the end of 2019.
With the present handling of 20 to 25 million litres of milk per day, Amul has become one of the largest milk processors in India and Gujarat Co-operative Milk Marketing Federation Limited (GCMMF) (Amul Federation), which markets the popular Amul brand of milk and dairy products, is the fastest growing dairy organisation in the entire world. As per latest report by IFCN (International Farm Comparison Network – a leading, global dairy knowledge organisation) Amul ranks 9th among the largest milk processors of the world.
Being a co-operative Amul is well supported by the association of 3.6 million farmers and hence Amul always ensures a sustainable income to their farmers.
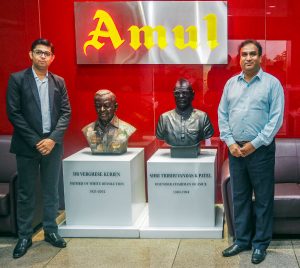
Amul processes the milk into every conceivable dairy product, from classic milk to cheese to chocolate to ice cream. To do this, Amul relies on the latest production technologies with the highest standards of hygiene. This is why, early on, Mr Anil Bayati GM installed pasteurisers and aseptic equipment for dairy products. Particularly for flavoured milk in single serve 200 ml packaging, Amul has gone beyond the pasteurised can and beyond the aseptic Tetra Pack.
In 2013, the first aseptic system for PET from Gea Procomac was installed in response to the boom for flavoured milk. The system provides the market with 30,000 bph. Just like the can and the carton, the flavoured milk need not be cooled for transport; the BBD is 6 months.
Flavoured milk viz. Saffron (Kesar), Elaichi, Rose, coffee etc. are different in colour and the customer can see through the transparent PET bottles to make their choice from a distance. In total, the milk beverage range in PET consists of 30 different products. These have a screw cap on a 38 mm wide mouth, from which the consumer can drink directly, comfortably.
Later in 2017, second and third line (One each from GEA Procomac and Krones) were installed. Now Amul could produce 1.5 million packs per day. Further to meet the increasing demand, Amul has ordered a fourth line, this time an aseptic linear filling system from KHS. Even these additional quantities of products were no problem for Amul to sell.
Crucial to the selection of KHS was the dry aseptic process, while Gea Procomac uses the wet aseptic procedure. “We must work very sustainably. Here in Gujarat, the use of water in particular is of immense significance. We recycle all the water we use and when it is no longer useful for processing, we water the green spaces and then it comes back sometime as rain,” says Bayati in his statement.
Amul already processes around 2,700 MT of plastic per month into packaging (poly film) for the food sector. So it was only a matter of time before Amul started producing the preforms and caps themselves for the aseptic lines. “First, we decided on caps. Our calculations showed that there was a higher hidden profit in cap manufacturing than in preforms, so we started with those.” Amul has bought one Husky closure injection moulding system and planning for another closure system by the 2019 year end.
At 38 mm and 3.1 g, the closures provide superior safety to protect the product’s sensitive contents. Bayati played into his own hand by producing caps for his two filling systems only. This meant that the injection moulding process and the sealing system on the filling line could be adapted to one another so that the capping system ran smoothly.
For the distant future, he is thinking about his own preform production for the 13.2 g preform. “When we have four aseptic systems with a total of 2 million bottles per day, then we can also build up a profitable preform production system,” says Bayati.
Another unsolved issue is that of recycling. “We have to take back and process the empty bottles,” he says with certainty. The bottle is also covered with a PVC sleeve, which makes recycling more difficult. But Amul is working closely with other major players of PET to come out with long term sustainable solution.