Revolution, not evolution
Sipa’s Xtreme up and running with customers
Sipa introduce the injection compression process for preforms. Still in its secretive housing and with a limited view of the technology. Now, we have been allowed to put our heads in the machine in Italy and check out every screw.
Interview with Mr Gianfranco Zoppas, Chairman
PETplanet: Hello Mr Zoppas. We are standing here in front of an operational Xtreme. You have been coaxing this project along for six years. Finally the machines are with satisfied customers. How does that feel?
Mr Zoppas: In these difficult times, it is great to see that our ideas really work. This is not one of those typical technical evolutions where we are making progress in the region of 1/10 of a gram. It is a revolution where we have completely reinvented the entire preform production.
PETplanet: Revolution sounds a little bit extravagant.
Mr Zoppas: Revolution is not just about technology; revolution is expensive but the result is what counts and I am very proud of what we have achieved.
PETplanet: With the concept of the integrated Xtreme system from recycling through to the filled bottle, the so called Xtreme Renew Sincro Cube, the inefficiencies of the individual components add together so that overall efficiency would have to suffer.
Mr Zoppas: We heard the same argument when we started around twenty years ago with integrated stretch-blow moulding systems, fillers, labellers and cappers. Today, it is impossible to imagine the market without these synchronised systems. Our investigations show that the technology runs in such a stable way that the overall efficiency of the entire line is above 90%, and the advantages of significantly lesser logistics and enormous energy savings from working with a single thermal cycle are overwhelming.
PETplanet: Bottling systems are usually sold without profit and money is made on the subsequent servicing; preform systems usually contribute to company stability when sold. How have you placed the concept of the Xtreme?
Mr Zoppas: At my age I think the money should flow right away but of course we tried to take other factors into account.
PETplanet: Many thanks, Mr Zoppas.
Interview with Antonio Narder, General Manager
PETplanet: Hello Antonio. The first three Xtreme went to Japan. Two are with a flake recycling system from Erema. Why did the customer want this combination?
Mr Narder: The customer is a PET recycler in Japan already producing PET flakes. He has expanded his supply chain from the processing of waste PET bottles to include preform production. Now, with the Xtreme Renew technology he bought, after the flakes have been decontaminated to food grade quality and the IV raised to the required level, the melt from the extruder goes straight into the hotrunner of the Xtreme for the production of preforms. As the flakes are only plasticised once, this saves energy and reduces the material degradation. Therefore the production cost of a recycled preform with 100% rPET from flakes is greatly reduced.
PETplanet: Why is there a melt pump installed between the recycling extruder and the hotrunner?
Mr Narder: Because it is important that entry to the Xtreme is at equal melt pressure. In contrast to classic injection moulding, this is very low at max. 300 bar. And that is one reason why the material is not placed under great stress and the IV drop is kept to a minimum.
PETplanet: What is the savings potential in the design of a preform produced with Xtreme technology?
Mr Narder: Xtreme technology overcomes current preform design limitations offering extensive lightweighting especially around the gate and under the support ring, areas which are not stretched during the bottle blowing. All this without compromising the mechanical performance of the bottles.
PETplanet: Why Japan? In the IM sector, the Japanese rely on local products.
Mr Narder: The Japanese believe in innovation and trusted our Xtreme technology. They have very high standards of quality and cleanliness, even in production. Here, with the 100% inline preform quality control and the fully electric Xtreme compared to IM with hydraulic components, we have been able to come up trumps.
PETplanet: Here, in your factory, there are four more Xtremes for delivery.
Mr Narder: This machine here is for Mexico. Here too, the Xtreme with 96 cavities is integrated with flake recycling. Another Xtreme starting from flakes is for a well-known multinational company for their facility in Poland and the other two stand-alone Xtremes running are going one in Korea and the other one in UAE. The latter has the option of producing two different preforms at the same time, which enables the customer to operate a large system even when item quantities of a preform are lower. This saves retooling time and cost.
PETplanet: This means that all your Xtremes are going to or have gone to bottlers or, as Japan, to recyclers?
Mr Narder: We can clearly see the focus on these customers. Ultimately, we want to offer the Xtreme integrated with the stretch-blower and filler. We have already one system running in Brazil since last year. Only bottlers would need this. Thanks to the fact that Xtreme technology can be connected upsteam or downstream, it opens new business models. In its Xtreme Renew configuration allows recyclers to increase the added value of their offer selling preforms instead of recycled raw material. Converters can take advantage of the combination of Xtreme preform production with stretch-blow moulders and operate a wall-to-wall selling bottles.
PETplanet: Thank you, Antonio.
Interview with Anna Horecica Csiki, Xtreme Product Manager
PETplanet: Hello Anna. You have been Project Manager for the Xtreme for six years now. There has already been an attempt by another company to develop compression moulding for preforms. Are there no reservations in the market for your new technology?
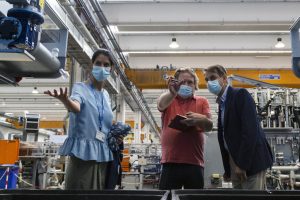
Mrs Horecica: The difference lies in the process. With the preform it is extremely important to be able to create reproducible conditions. The melt in particular requires a lot of attention. With us, the melt comes continually from the extruder at the relatively low pressure of 160 bar and flows into the rotational hotrunner. Each cavity has its own dosing and injection unit which holds exactly the quantity of melt for the preform in the allocated cavity. Then we increase the injection pressure to max 300 bar. This injection-compression process is completely different to other developments and it guarantees to us that there is an optimum filling of the material in each cavity to produce a perfect preform.
PETplanet: And each shot pot is individually adjustable?
Mrs Horecica: Yes, so we can adjust each cavity optimally. We have further enhanced the concept and you can see on the system for the Middle East here that by adjusting the shot pots and of course using different stacks, we can also produce two very different preforms on the carousel at the same time.
PETplanet: This means that individual cavities are mounted on the carousel?
Mrs Horecica: Yes, the entire unit consists of two parts that the customer can quickly and easily adapt. The lower part is the hot side with the shot pot which does not require any changeover; the cold side (the injection stack) is above and no crane is needed for the exchange; the parts can be quickly removed by hand. This makes working at the machine much easier.
PETplanet: How does this configuration influence the mould change-over?
Mrs Horecica: Xtreme technology and special design of hot and cold parts allows the preform to preform changeover in less than 2 hours.
PETplanet: How do the preform inspections work?
Mrs Horecica: Here at the transfer station to preform cooling, we have two cameras that inspect neck geometry and injection point. Above, at the end of the cooling zone, there are three more cameras that check the outside body of the preform. A special software is able to identify the two different preforms produced simultaneously.
PETplanet: Thank you, Anna.