Review on the PETinar series: Technical highlights at Drinktec 2022, day 1
A positive excitement could be felt by everyone in the last days before the Drinktec fair. The PET and beverage industry was shuffling its feet and could hardly wait to get back to exchanging ideas with customers and visitors. To make the wait easier, PETplanet initiated a preview series ahead of the fair. On two consecutive days, a total of six talks on PET-relevant technical highlights took place at the PETinar online conferences. As an industry expert and Editor-at-Large at PETplanet, Ruari McCallion led us with his charm through two highly interesting days.
The series started with an introductory interview by Alexander Büchler, Publisher of PETplanet Insider with the Exhibition Director of the Drinktec trade fair, ‘Ms Drinktec’ Petra Westphal. The twenty-year cooperation between Drinktec and PETplanet gives an idea of how much both sides enjoyed exchanging ideas. After some remarkable memories such as the idea, development and implementation of the PETpoint hall at Drinktec, Petra Westphal delivered some hard facts about the upcoming Drinktec 2022.
According to the fair’s data on visitor numbers, every third visitor comes from the dairy and liquid food industry, every fourth from the wine industry, whilst every second visitor comes from the beer sector. The majority of visitors represent the non-alcoholic beverage industry. Petra went on that the 1,001 exhibitors from 55 countries not only present their highlights across the entire value chain but also in relation to the four hot topics of the fair: sustainable production of packaging, water & water treatment, digital solution & digital transformation and finally consumer demand & consumer development. Petra stated that in the newly established innovation hubs, exhibitors would have the opportunity to present their best-case studies dealing with the four main topics of the fair. Despite the well-known very difficult circumstances such as the pandemic or the Russia-Ukraine conflict, 22 exhibitors from China and three from Ukraine are expected. Even though there would have been more representatives from these countries in a normal trade fair year, Petra gratified by the presence of the exhibitors who were now presenting their technologies. She closed with an invitation to the Drinktec 2022 and thanked PETplanet for the opportunity to present Drinktec at this special PETinar.
More ECOnvenience
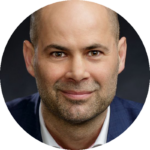
After this positive introduction, Mr Thomas Schmidt, Group Marketing Director at Bericap, presented Bericap’s new sustainable and consumer-friendly closure solutions. Thomas briefly introduced Bericap: the quality-oriented family business is represented in 100 countries with 26 factories worldwide. With specialised R&D centers and its own mould shop, Bericap has intensively driven the development and industrialisation of tethered caps solutions. The development of the closures targeted to improve the beverage experience in multiple aspects: convenient pouring at home, comfortable drinking on-the-go and finally consciously protecting the environment by the joint collection of bottle and cap. After the first successful customer market launches with the Bericap ClipAside the company has executed a consumer survey and has put his own closures to a daily-life test.
The result was very positive in terms of closure handling, hygiene and especially from an ecological point of view. Bericap recognised and already solved one potential issue for the consumer specially for on-the go-dairy products: after shaking the package some foam stays in the cap. To avoid liquid dropping out of the closure when drinking from the bottle, Bericap developed the patent pending capillary ribs with a frosted head plate surface. This technology improves the retention of the fluid in the cap.
The ClipAside tethered caps solution is available for all relevant neck finishes. The opening angle is between 170-180 ° depending on the neck finish. It has a consistent performance on all relevant neck finishes from 26-38 mm. Production on an industrial scale was carried out with a trial, in which 80 million caps were cut with one knife. In order to produce the ClipAside cap it is not necessary to change the neck area and little or no adjustment has to be done to the capper or on the inspection system. A flexible transition is possible due to the slitting technology: the transfer to a new shell design with standard slit or changing the slitting geometry to tethered whenever required. At Drinktec, Bericap presented an already lightweighted tethered cap solution for CSD beverages. Thomas continued that Bericap also showed its new generation of sports caps. For example, the new two-piece closure Monet, which is available in HDPE (single material) with a tamper evidence overcap and visible drop ring. The closure is suitable for dry and wet aseptic application.
AC-E: the new all-electric high-speed benchmark

Mr Arnaud Nomblot, Director of Business Development Packaging at Sumitomo (SHI) Demag, announced the premiere of a new machine at Drinktec. He briefly mentioned some facts about Sumitomo (SHI) Demag. The company belongs to Sumitomo Heavy Industries which is headquartered in Japan. Sumitomo (SHI) Demag accounts for 12% of the group’s activities. Each year, 7,000 IMMs are manufactured in four production plants, one in Japan, two in Germany and one in China. Arnaud explained that Sumitomo is very proud to be the world leader with around 80,000 all-electric machines in operation. The focus of Arnaud’s presentation was on plastics packaging.
The new Sumitomo (SHI) Demag PAC-E injection moulding machine has combined the strengths of two machine types from Sumitomo, the El-Exis SP and the IntElect. The fast, reliable and proven technology of the El-Exis and the low energy consumption and all-electric competence of the IntElect are newly combined and reinforced. With the expertise of the two specialised competence centers in Japan (electrical drives and control knowledge) and Germany (packaging know-how), the PAC-E will be available worldwide. Arnaud said the new machine meets the requirements of the global beverage market. Performance, reliability, energy efficiency and finally cleanliness are the key parameters.
In respect of performance, Sumitomo has adopted all the mechanics from existing packaging products, such as the clamping unit and platens, which are critical parts in the production of packaging parts. The performance of the clamping unit and the opening and closing speed of the mould were maintained. The machine has a fast injection speed of 550 mm/s and a high-performance plasticising drive to meet the production requirements of short cycle times and high output in terms of kilograms of plastic converted per hour. The ejector is designed for the high speeds required for the applications and the application-specific interfaces have also been taken from proven technology and meet all the required packaging specifications.
In terms of energy efficiency, the drives and motors are specially designed for processing plastic packaging. All components of the motors and drives are manufactured by Sumitomo Heavy Industries itself. The last key parameter Arnaud mentioned was cleanliness. All the main axes, such as the clamping unit drive for opening and closing the mould and the injection drive, are completely encapsulated. The machine works with a closed lubrication cycle. This ensures that the closures and packaging are produced in a clean environment and the effort required to clean the machines is reduced by this closed system. The closed lubrication circuit means that fewer lubricants are used. Costs are saved from the sustainable use of lubricants. All in all, the machine is the result of best-in-class development in collaboration with best-in-class partners such as z-moulds, Intravis, Sise, Piovan, Eisbär and Ineos, Arnaud concluded.
Does size matter? – New challenges for the closure production require new mould solutions
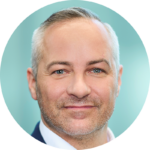
As the final highlight of the first day of the PETinar conference, PETplanet has invited, as Ruari aptly remarked, a good friend of PETplanet. Mr Michael Fink, Vice-President of Sales & Marketing from z-moulds came up with an equally remarkable innovation.
Michael first presented some facts about the company z-moulds. The company is headquartered in Dornbirn, Austria, with a subsidiary in Atlanta, USA. Its global presence stretches from Canada to Mexico, Brazil to the U.A.E., India and finally China. He continued that z-moulds, as a mould making specialist for caps helps it customers to develop the best design for any cap application. All global testing standards are possible in the approved z-moulds laboratory. After designing, testing, and developing, z-moulds supports the inline work at its customers’ premises.
Michael explained the well-known, proven, and patented z-slides technology. It differs from other mould systems in the following aspects: the front of the mould has a complete flat parting line. Centring of the cavities is not necessary. The cavities and sliders are located inside the mould. The mould itself is centred with guiding bars; this results in an almost wear-free system. Each cavity is accessible from the front. The entire cavity stack can easily be pulled out so that each part of the cavity can be replaced (eg. core, cooling top, slider). The 70 mm frame of the mould stays the same for all kind of closures. It is a completely modular system. Also, the cavity pitch remains the same, and in addition the same hot runner system can be used. Michael continued that the z-slides technology is still used but has now been extended. For a tethered cap, for example, the sliders must be higher because the parting line is moving up. By changing the angles on the demoulding face, where the height is increased to 15 mm, it is possible, to produce a 29/25 closure design entirely on the cold half of the mould. The extended z-slide technology can easily be implemented in the existing z-slides system. Michael concluded that all z-moulds technologies like the z-slides, z-slides extended, and the z-folded system are compatible with each other.
With such cutting-edge technology, new ground can be broken. Michael asked what can be enhanced for tomorrow and talked about the mould size. He stated that in general the z-slides are known for their compact size because no sidewards movement is necessary. In the future could it be possible for the mould size to be even smaller? He presented two case studies.
The first one was a project for a customer where a 23 mm light weight closure has to be produced on a high speed 128 cavity system in less than 2 s. The problem today is that existing 128 cavity moulds are very big, and because of that they need big machines (eg. 650 t). From a closure point of view, these big machines are not necessary. As far as the clamping force goes, a 420 t machine would be enough, but the mould is then too big.
With a new mould design with a pitch of 55 mm the mould fits in a 420 t standard cap machine and this common machine size range allows faster cycles. Also the weight of the moving part of the moulds is important. With the smaller mould there is a 52% weight saving which in turn reduces the overall cycle time. The reduction in cycle time results from the falling distance being cut to 300 mm, leading to a saving of 0.07 s. falling time per shot. Michael concluded by saying that with a new frame a smaller machine range can be used. Mould-handling is much easier and the reduction in cycle times can be achieved due to the lighter weight and height of the mould. And finally, the less weight that needs to be moved leads to an enormous energy saving.
The second case study focuses on a 96-cavity moulding system running in a 420t machine. Some new closure designs require less clamping force, and consequently, a 250t machine would be enough. As in the first example the size of the mould is too big. With the new z-slides pitch of 55 mm the fall height is reduced, resulting in less falling time; the weight of the mould is reduced which leads to a more rapid opening and closing time, resulting in a lower energy consumption.
The answer to the question ‘does size matter?’ seems clear: energy savings, fast cycle times, a smaller machine are important parameters on which purchasing decisions are made!