Circular economy in action
PET bottle-to-bottle recycling the focus of attention at Sipa Open House
At an Open House in Vittorio Veneto, Italy, Sipa and its partner Erema demonstrated how their co-developed Xtreme Renew technology converts post-consumer PET bottle scrap into food-grade preforms and bottles with excellent properties and colour. A unique example of closed plastic loop.
“Xtreme Renew is the first system in the world to produce food-grade preforms from 100% washed post-consumer recycled PET – rPET – flakes in a single thermal cycle,” says Gianfranco Zoppas, Chairman of Sipa parent company Zoppas Industries. “It is both cost-effective and highly energy-efficient.”
When PET bottle preforms are produced from recycled material using previously developed rPET processes, the amount of carbon dioxide created is already 60% lower than when using virgin PET. With Xtreme Renew, these emissions are cut by an additional 25%, and 30% less electricity is consumed, thanks to the integration of the various phases of the complete process into a single plant, states the company.
Erema technology incorporated into Xtreme Renew converts conventional washed bottle flakes into decontaminated PET food-grade melt with an increased viscosity (IV). The melt is then immediately fed to the Sipa section of the plant, which creates preforms using the new injection-compression moulding technology. Because the recyclate is put through a single thermal cycle, the overall quality of the preforms is higher than with other systems in which the recyclate is granulated and then re-melted. This is most evident in terms of aesthetics: the preforms are less yellow and more transparent.
Preforms produced using Xtreme Renew are up to 10% lighter than traditional injection-moulded preforms. According to the company, Xtreme Renew can also reduce logistics and transportation costs by 20% and the Total Cost of Ownership by 15%.
Sipa also offers the option of directly connecting Xtreme Renew to its stretch-blow moulding equipment for production of finished bottles – several months ago, the company unveiled a new generation of very high-speed rotary SBM equipment called Xtra – as well as filling lines, which it also manufactures in various versions according to the type of beverage to be bottled.
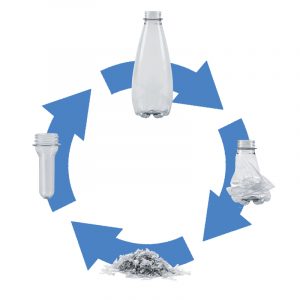
“I believe it is vital that a circular economy is implemented as quickly as possible, or our industry risks becoming a victim of its own success,” Zoppas says. “Without it, the levels of plastics packaging re-use will not be enough for a fully sustainable packaging sector. I hope and trust that our actions will provide an important boost in making PET packaging sufficiently sustainable for its future success.”
Xtreme Renew technology found its first commercial application late last year: Erema and Sipa collaborated with two Japanese partners – Kyoei Industry (a major recycling company) and Suntory (one of the largest beverage producers in the world) on an installation in Kasama in Japan. The system can produce over 300 million rPET containers per year. The Japanese companies have already ordered the second Xtreme Renew line.