0.25 litre CSD bottle with internal coating
We met: Mr Girish Chhablani, Factory Manager HCCB
First production of the 0.25 litre CSD bottle with inner coating began nearly three years ago at Hindustan Coca-Cola’s plant in Hyderabad, India. There are currently four plants on the sub-continent with two more in the pipeline. So, it is time to drop in and get to the bottom of the technology.
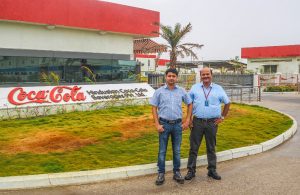
Hindustan Coca-Cola Beverages Pvt Ltd (HCCB) was looking for an alternative to their returnable 0.2 l and 0.3 l bottles. Due to the long sales distances, a different option needed to have a shelf life of at least six months. To this end, an attempt was made to develop a PET bottle involving Coca-Cola Atlanta and KHS. The bottle still had to be affordable. That is why HCCB called the packaging affordable small sparkling package or ASSP. The lack of barrier properties in the small PET bottle size only achieves a 60 days expiry date, which allows the Plasmax coating system to be used. A three-layer inner coating (adhesives, glass barrier, coating) can achieve the necessary shelf life. The original facility was built in Hyderabad in 2016. With a capacity of 36,000 bph, Coca-Cola was able to capture the Indian market. A second plant was built the following year in Vijayawada, which achieved a figure of 46,000 bph using similar technology. It differs from the original plant in that it is blocked (triblock), with unreliable air conveyors having been removed from the single machine layout. The stretch blow mould, Plasmax and shrink packer components are supplied by KHS Germany while the capper fillers, transporters and palletising are provided by KHS India.
Box kipper
A completely new greenfield plant was built by HCCB in 2018 in Sananda, near Ahmedabad which we were allowed to visit. The plant manager is Mr Girish Chhablani who explained everything to us. There are two Triblock Freshsafe machines next to one another in the bottling building. In the filler zone, the control positions face each other, which means that just one operative is required in this area. As the blow moulding machine always rotates clockwise (from Blomax Series 5, anti-clockwise), the unit has been mirrored point-symmetrically. As a result, the preform material flow, bottle, filling and capping counter-rotate on both units. The two machines can be run by three operators on each shift. One is responsible for the filler area on both units, from the blowing stage to full bottle inspector and the second for the labelling and packing machines on both units. A third operative takes care of the palletising zone.
The process begins with a preform inspection. Preforms containing foreign matter (1 ppm or more) are removed. They then enter a 24-cavity SBM. The heating tunnel is not very long as only preforms weighing less than 10 g are heated. Each blown bottle has its own code which is later covered by a label showing cavity and production time. Air vents cool the floor area via several transfer stars and the Plasmax enters the unit’s main system. The bottles go into vacuum chambers in batches of four. On evacuation, three layers are deposited on the inner bottle wall via ignited plasmas. First there is an adhesive layer, followed by the actual glass barrier layer which is only a few molecules in diameter, and finally a protective layer. The glass layer is clear in contrast to the yellowish carbon colour of other coating processes. After evacuation, the bottle’s temperature is around 50 °C. It is cooled from the outside using a water aerosol to approximately 20 °C before being filled in a 144-cavity volumetric filler and secured by a 24-fold servo-capper. Finally, there is another full bottle inspection, followed by further coding which can be used to make a decision on the filling valve and capper head. Production information is recorded in a text box which can be read by the customer.
Preforms weighing between 9.61 g and 9.68 g are processed by the preform supplier. HCCB blows a total of three different bottle geometries for its 17 different products. The cap on the 22 mm neck is supplied by Bericap. The unusual outer curvature for a CSD cap offers a high level of stability at low weight, thus providing a secure seal against loss of CO2.
The chief component of the units is the plasma coating. The quality of the coating cannot be determined by conventional inline measuring methods which is why monitoring of process parameters is carried out. If these exceed a certain tolerance level, the bottles are rejected. Special attention has to be given to the vacuum pumps which are contaminated by residues sucked in via the vacuum. At each CIP (every 48 hours), the units must be thoroughly cleaned to ensure the process parameters remain within prescribed tolerance limits.
HCCB are very pleased with their units. Soon after commissioning, they received an efficiency level of over 90% despite the sensitive nature of the plasma coating. It is therefore no surprise that two more have been ordered for the Indian market. In addition to the four already in India, the other two in Indonesia and Nepal, Coca-Cola now have eight in all.
Hindustan Coca-Cola beverage factory at Sanand, Gujarat, is now a Gold Certified Green Building
The Indian Green Building Council (IGBC) has awarded the Gold certificate to HCCB newest factory at Sanand, Gujarat. The factory – a fully digital and world-class facility, became operational in mid-2018. The Sanand factory is only one of nine Gold certified Green Buildings (factories) amongst the FMCG / Food industrial facilities in India. It is also the only factory run by HCCB, which employs more than 40% women. The Gold certification to the Sanand factory is based on an assessment of the site in the categories of sustainable site, water conservation, energy conservation, indoor environmental quality, material conservation and innovation. Initiatives such as prevention of soil erosion, group transportation and shuttle services, on site solar power generation & effective usage, rainwater harvesting, re-use of wastewater, vehicle charging facility, and several others, have been undertaken at Sanand to develop it into a green site.