Bottle making
On this page you can find all contributions related to bottle making
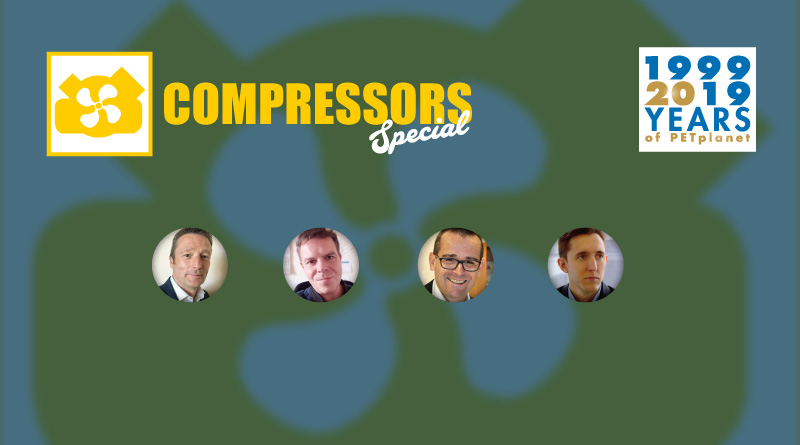
A review of PET compressor developments
A large amount of air is needed to blow PET preforms into bottles. The compressors that compress atmospheric air into compressed air must withstand extreme conditions such as high pressures, heat and continuous operation. But the success of the blowing process depends on a consistent and clean flow of air regulated at a specific pressure.
The first models of compressors constructed for the bottle-making process appeared on the market when the PET bottle industry took off in the late 1970s and early 1980s. Reciprocating piston compressors are the most common type in the stretch blow moulding field. Since the early 2000s, centrifugal compressors have also been found on the PET bottling market. Centrifugal compressors provide 7-13 bar air, which is compressed to the desired pressure by a booster. This type of compressor requires less maintenance than equivalent models of reciprocating compressors as there are fewer inbuilt sliding parts. Disadvantages are the amount of floor space and the need for two units to do the work. With piston compressors, the air becomes ever more compressed in different cylinders and then is cooled again. After opening the suctions valves, atmospheric air is fed into the cylinder through an air filter and is compressed for example to 4-5 bar when drawing back the piston to the cylinder head, and this warms it up. The compressed air is pushed out of the cylinder through a delivery valve and is cooled in an inter cooler. Moisture is removed. In the next step, compression, for example, to 15-17 bar is achieved. The air is cooled again and dehumidified before compression, for example, to 40 bar is achieved.
The required pressure depends to a certain extent on the container’s design and its wall thickness. Thick walls and sharp edges require higher pressures than simpler shapes and thinner walls. As a general rule, the stretch blow moulding process works with a pressure of 10-25 bar for pre-blowing and a maximum of 40 bar for the bottle blowing process. A pressure of 7-10 bar is needed to actuate pneumatic equipment. For most water or CSD lines, a maximum output of around 3,000 m3/h is sufficient; for plants with particularly high compressed air consumption, for example for hot filling, models with an output of around 6,000 m3/h are available. Depending on the layout of the cylinders, designs include L-shape; Y-shape; V-shape; or M/W-shape, horizontally opposed design.
Is the air clean?
The purity of the air is essential for the stretch blow moulding process. Water, dust and oil are the typical particles that must be cleaned from the air before bottle production by a separate air purifier system.
Some compressor manufacturers rely on oil-free systems. However, because of the lack of lubricant, these can more easily generate abrasion particles, making it necessary to filter out these typically larger particles.
In order to recycle the compressed air after blowing the bottle, it can be captured using an annular pressure vessel and is fed back into the network using an air recovery system.
A bundle of energy
Manufacturing PET bottles is an energy-intensive process. As the PET market has matured, plant engineers have come to realise that their choice of certain compressor models affects the profitability of the overall system. Ultimately, the compressors are the largest individual energy user in the system, taking around 50% of the total energy expenditure. To save costs and also because of rising environmental awareness, more and more companies are paying close attention to the calibration of the air pressure they actually require. As mentioned above, a pressure of 40 bar is the maximum required to manufacture standard PET bottles. Each reduction brings energy and cost savings, which explains the trend towards lower pressure settings. Depending on bottle volume and production performance, analysis is performed to establish which blowing pressure is needed for which product.
Compressors for PET bottle manufacturing – some highlights 1999 to 2019 as reported in PETplanet
2000
The very first article on compressors in PETplanet Insider came from LMF Austria (issue 1/2000). The company had developed and brought onto the market a new compressor design, delivering from 353-1,413 cfm (600-2,400 m³/h FAD). The basic aggregate consists of either a 3-stage VC type compressor for 353 cfm (600 m³/h) or a VCL type for 706 cfm (1,200 m³/h). Its total capacity can be doubled by adding a Roots blower as a booster. It is possible to adjust the blower motor capacity via a PLC control system to produce exactly the amount of air required at any one time (e.g. when the size and/or number of bottles per hour is not constant).
Belliss & Morcom supplied their first PET compressor system in 1978, when PET bottle manufacture was still in its infancy. In 1995 the company merged with Hamworthy and became part of the Powell Duffryn group. The merger provided the newly-named company, Hamworthy Belliss and Morcom with the backing of a powerful industrial group. In issue 7 they announced three new versions of their oil-free PET system compressors range.
LMF’s development of a logic controller to control the pressure and flow rates of several compressors delivering air for PET bottle blowing is also a topic in issue 7. The company saw that many of their customers were using more compressors, or more compressor capacity, than was really necessary for the job being done. The first installation was realised at Coca Cola in Austria.
2001
In issue 4+5 AF Compressors explains why they chose an L-shape design for their compressors. The “L” shaped layout makes it possible for the number of moving parts to be reduced to a minimum. There are only two cross-head assemblies with two piston rods and associated bearings. The fact that the pistons at stages two and three are single-acting also means that a minimum number of valves are required. Having pistons 2 and 3 on the same piston rod means that the 40 bar stage (piston 3) does not require piston rod air packing seals between the 40 bar compressed air and atmosphere.
In issue 11+12 we report about the joint forces of Boge and Siad in the field of oil-free compressors. The oil-free system, called the Superflow, makes use of an oil-free screw compressor from Boge and an oil-free piston booster made by Siad. The whole unit can be supplied completely skid mounted, complete with driers, receivers, water coolers and control panel. The range of installations offers 19 different options, with blowing air outputs from 1,150-3,000 Nm3/h.
2002
When Atlas Copco introduced their Petpack compressed air system in 2000 they took a novel approach by combining oil-free screw and piston technologies. In issue 4/2002 the company announced a new standard in cost effective bottle blowing with the introduction of Petpack VSD. The Variable Speed Drive technology in both the screw compressor and the piston booster introduces power savings.
2003
Kaeser has created a system solution to satisfy the requirements for control and blow-moulding air at different pressures with the “Sigma PET Air” system, which consists basically of a low pressure stage (at least one fluid-cooled rotary screw compressor with a refrigeration dryer for the control air) and a high pressure stage (at least one booster with a high pressure refrigeration dryer) plus the necessary filters and condensate treatment equipment (issue 12). The screw compressors are fitted with modulating control, which ensures that the compressor’s air delivery always matches the air demand from the blow-moulding machine.
2004
A centrifugal compressor for PET bottle blowing was highlighted as a world first in issue 1+2. It is Ingersoll Rand who make compact centrifugal compressors available for PET bottle blowing at 40 bar. Reasons for that were their long life, due in part to an inherently simple and rugged design (there are only four basic moving parts – a bull gear and three rotating impeller assemblies); the dynamic compression process in which the air is compressed by converting velocity energy, imparted by the impeller, to pressure energy without any contact between mechanical components, ensuring oil and particle free air; the energy efficiency through the use of multiple stages in conjunction with constant pressure control operation.
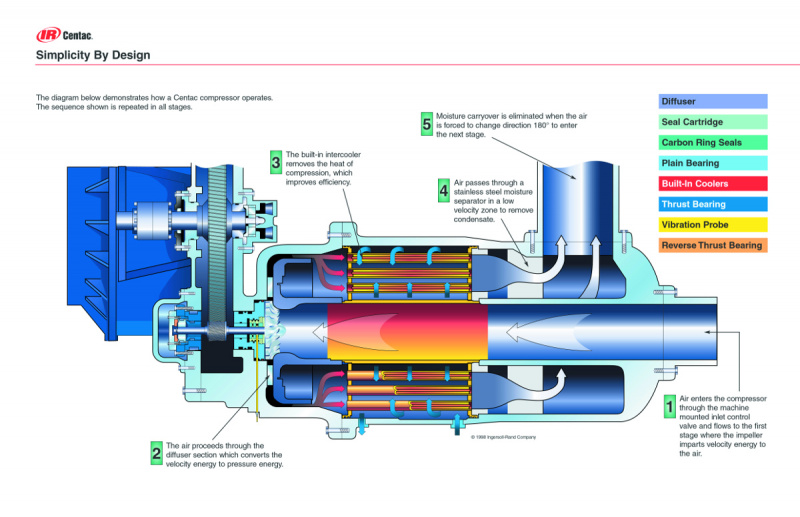
In Issue 9, we presented an alternative approach to compressed air: renting rather than purchasing a reserve compressor minimises capital outlay and the maintenance costs associated with a unit that may not be utilised year-round. All the plant manager has to do is to provide level ground and a power source.
Atlas Copco’s new ZD line has been developed specifically for PET bottle blowing (see issue 12). The company took a fresh look at some other aspects of a PET compressor, which had previously been regarded as unalterable characteristics of a 40 bar system: A first in PET compressor design is the piston compressor’s integral concrete base plate which eliminates the need for special foundations of any type and allows the compressor to be picked up and moved by fork-lift. The base-plate absorbs all of the vibration, with no transmission to the ground. The base plate also includes buffer capacity for 10 bar air – no need for a separate 10 bar receiver. In combination with a newly developed silencer housing it is now possible to locate the compressor in close proximity to the blowing machine.
2005
1998 saw the introduction of the LMF EcoPET range of compressors with smooth speed regulation. Seven years later we reported in issue 9 on the extension of some models (from 950-2,700 m³/h) and the development of Eco-Speed-Control for efficient use of compressed air. A single-stage, oil-free, rotary blower is used as what LMF call their booster (the term booster normally being applied to the latter, i.e. piston stages of a multi-stage system). Its strong point lies in its ability to compress large quantities of air at low pressures. To cater for the periods under partial load, typical of a blowing air compressor, LMF developed and introduced the Eco-Speed-Control. The advantage of this system is that only the booster (rotary blower) is controlled by a frequency converter that matches it to the final pressure of the unit as a whole. This means that the piston compressor downstream is fed with less air, so reducing its power requirement proportionally.
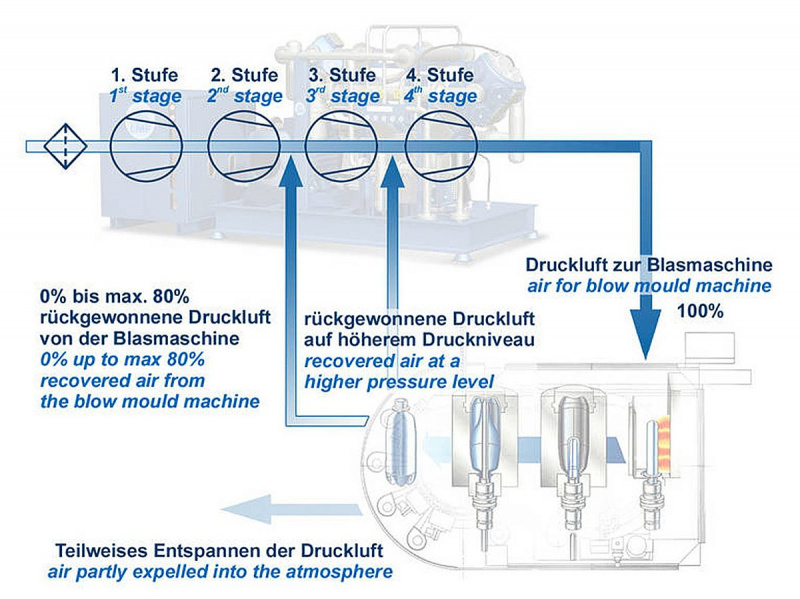
PETpoint exhibition in September 2005 saw the unveiling of Atlas Copco’s latest compressor system ZD, developed specifically for PET bottle blowing (see also 12/2004).
2006
In issue 11+12, LMF Austria discussed the topic of air recovery and demonstrated the possible savings if the compressed air is fed directly back into the blowing compressor using the patented EcoPET C.A.R. (Compressed Air Recovery) after the stretch blowing process. The pressure level of the return air, which is available for further use, is between 6 and 18 bars, and the amount of air fed back into the compressor can be between 0-80%. This optimised air control system is made possible by the use of “smart” valves integrated in the compressor control circuit.
2008
At the 2008 edition of Brau Beviale, Kaeser Kompressoren featured a powerful booster used to deliver air at up to 45 bar as well as the compact “Sigma PET Air” complete compressed air system for stretch blow moulders. Also on show was the Kaeser screw compressors and the “Sigma Air Manager” which controls and adjusts the flow and pressure from several compressors for maximum economy and efficiency (issue 10).
2009
Gardner Denver Ltd used Drinktec to show its new VH25 oil-free compressor for PET bottle blowing and a new, low-maintenance, shaftless and water-cooled motor, as reported in issue 10. In common with other compressors in its VH range, the VH25 features its AirPET air recovery system, which is designed to accommodate a returned pressure from the blow moulding machine that can be recycled back through the compressor.
At PETpoint, Kaeser Kompressoren exhibited its new dry-running rotary screw compressors and the ‘Airbox Centre’ – a compact compressor system offering all-in-one compressed air production, treatment and storage. The compact system is an all-in-one solution for compressed air production, treatment and storage, with a dry-running industrial reciprocating compressor at its core, providing free air delivery of 0.9 cubic metres (issue 9, photo above right).
2011
Compressor coordination and regulation: In issue 4, ABC Compressors presented its works on savings in compressor central units and made recommendations to guide distribution line set-up. Coordinating the work done by all the compressors together helps to provide energy savings in a number of ways: it minimises the number of compressors running idle and the number of start-ups; it helps to stop machines that are not required and identify which compressors should be adapted to total air demand at any time; and covers possible compressor stoppages due to maintenance requirements or breakdowns.
2014
The name is Vito. In PETplanet 1+2 we introduced Siad’s new compressor technology, the result of a complete re-think both of the design and production of an entirely new compressor concept. The new model should be suitable for all performance categories above 1,200m3/h, with variable speeds to ensure flexibility in production. Covering all performance ranges with just one compressor generates cost savings in the manufacturing process: a number of identical parts can be used. This of course includes the pistons, piston rod and crankshaft.
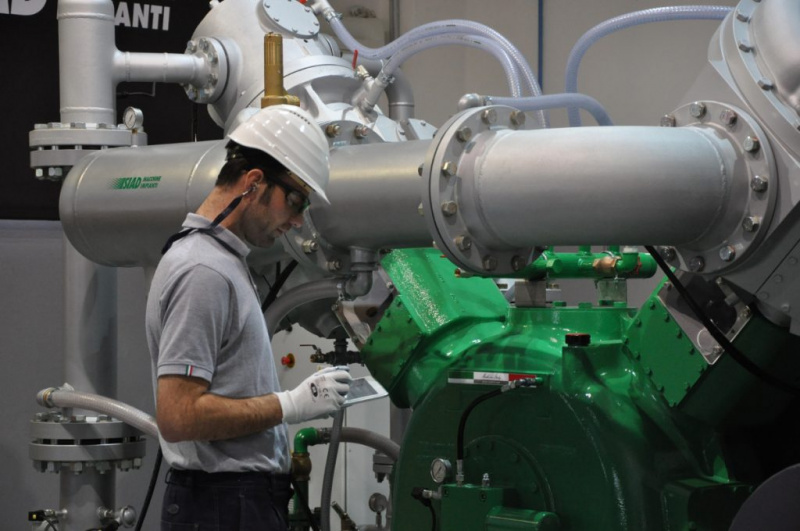
2015
With the launch of a new machine, the WH35 high-pressure reciprocating compressor, the celebration of Gardner Denver’s 45-years anniversary festivities at its Redditch, UK site, hit its peak, as we reported in issue 9. The oil-free system offering 2,120m3/hr at 40barG was claimed to bridge the gap between their WH29 model, with its output of 1,800m3/h and the WH40, with its output of 2,300m3/h.
2016
Improved volumetric design and optimally balanced compression ratios were introduced in issue 3 by ABC Compressors and their Horizon models’ cylinders. To avoid losing energy in the transmission between the electrical motor and the compressor shaft, a direct coupled configuration has been constructed. Reducing the moving parts of the cylinders by 33% also affects the maintenance costs in a positive way.
Issue 5 highlighted two energy saving features, the Variable Speed Drive (VSD) and the Heat Recovery System from ABC Compressors. The VSD adapts, by means of a pressure transmitter, the compressor rotational speed to the actual high-pressure air consumption needed, maintaining at the same time the required working pressure in the pipe line. This reduces or even eliminates the compressor idle operation and the resultant wasteful energy consumption. The Heat Recovery System recycles the heat generated during compression to provide hot water (above 80°C) for the operation, allows extra savings and reduces the CO2 footprint. After each compression stage, hot air enters a first phase cooling chamber from where hot water can be provided while the air continues to the next cooling phase.
For the Gropper Group, Gardner Denver installed a piston compressor with a focus on energy efficiency. This included a roof-top cooler and a heat recovery system (also issue 5).
Also in Issue 5, we reported on tools from Kaeser Kompressoren that aim to increase energy efficiency: the integrated Sigma Control 2 controller ensures comprehensive monitoring and straightforward connection to communication networks via i.e. Ethernet or databus interfaces. The integrated web server enables clear visualisation of current machine status (e.g. process data) via Kaeser Connect.
2018
Induction motors, as used in compressors, have a very high starting current; often many times the nominal current. This can cause problems with plant power networks if, for example, several motors in the factory start at the same time. Using standard electric motors, AF Compressors addressed this problem in issue 1+2 with its SIS (Smart Inverter Starter). Developed by Ateliers François Liège, this inverter system for starting purpose only, ensures that the starting current never exceeds the nominal current and that the full load power never exceeds 100%. Another way to save energy is to adjust the air flow in cases where less than full air capacity is needed. AF’s Adjustable Air Flow System (AFS) does this by deploying a special working protocol around the acting compressor cylinder.
In Issue 8, Atelier Francois announced improvements to its “L-shape” design compressors: the compressor cylinders themselves have been redesigned, new piston ring technology has been introduced, and improvements to the interconnecting pipework and intercoolers have increased air capacity and output. In the same issue, Bellis & Morcom explained the advantages of the shaftless motors, which are built directly onto the compressor crankshaft to ensure direct transfer of the power into the running gear. Kaeser Kompressoren demonstrated in the same issue possible energy savings that can be realised through analysis by its energy saving system, KESS. Air treatment systems, which recycle the warm exhaust air from the compressors, were also presented.
Companies
1 blow |
ADS Single Stage Molds |
Agr International |
ABC Compressors |
Absolute Machinery |
ADEKOM |
Aeroflon |
AF Compressors |
Airpack GmbH |
Alpla |
ALPS |
Amcor |
AMS Ferrari |
Amsler Equipment |
Ant Packaging |
Aoki |
Arburg |
Atlas Copco |
Automa |
AVE Technologies |
Aventium |
Awanti Polymoulds |
Bahubali Group |
Baijinyi |
B&G Products |
Beaubury Precision |
Bekum |
Berry |
Belvac |
Bevazar |
BJY |
Blue Air Systems |
Boge Kompressoren |
Büsser Formenbau AG |
Caiba |
CanNeed |
Chen Hsong Machinery |
Chemco |
Chumpower |
CKS Packaging |
Clever Pack |
Comep |
COMPETEK |
CompAir |
CPS |
Creative Plastic |
Creative Blow Mold Tooling |
Cypet |
Dalgakiran |
Demark |
DEMO Design and Moulds |
DOLOOP |
Dong-A |
Europlast |
E-ProPlast GmbH |
Eskapet |
Ferromatik Milacron GmbH |
First Circle |
FlexBlow |
FOBOHA |
Full Shine |
GS4PLASTIC |
Gefit S.P.A. |
GDXL |
GEA Group AG |
Gerresheimer |
Graham Packaging |
Green Box |
Greiner Packaging |
Global PET Industries |
Guozhu Group |
Guanghzou Sharelemon |
Gulf Packaging |
HAIDLMAIR GROUP |
Hallink |
HEATLOCK |
Hertz Kompressoren |
Himalayan |
HO.BAG |
Hokkan Indonesia |
HRC |
Huayan |
Huiyuan |
Husky Injection Molding Systems |
Indoair |
IMD |
Intravis GmbH |
IntraPac |
Integrated Plastics |
KEENPRO |
KIEFEL GmbH |
Kiefer Werkzeugbau |
Kirin |
Köksan A.S. |
IPR |
JMS International Packaging |
Jomar |
JSC Plastikse |
KHS |
Kisan |
Klöckner Pentaplast |
Kosme |
Krauss-Maffei |
Krones |
Lanfranchi |
Lightweight Containers |
Limner Tech |
LMF - Leobersdorfer Maschinenfabrik |
Logoplaste |
Lonzapet |
Luxber |
Maag |
MAG Plastic Machinery S.A. |
Maguire |
Mahathanee |
Manjushree Technopack |
MAGIC |
MAS |
Measom Freer |
Meccanoplastica |
Mega Machinery |
MHS |
Mold-Masters |
Moretto |
Motan-colortronic GmbH |
Mould & Matic Solutions |
M/S Mechanical Systems |
M. Tanner |
MULLER |
Nampak |
Negri Bossi
Newamstar Packaging Machinery |
Nishant Mouldings |
NIIGON |
Nissei ASB |
Ngoc Nghia Industry |
Novapet |
O. Berk Company |
P + S Technology |
PACCOR |
Packsys Global |
Parker Plastic Machinery |
Pass Card Co. Ltd. |
Pearl Engineering Polymers |
PET-Verpackungen GmbH |
PDG Plastiques |
PEGASO |
Petainer |
PET ALL MANUFACTURING INC. |
PETCO Gulf |
PET Engineering |
PET Machinery |
Petmorocco |
Petka Mold |
PET Solutions |
PET Technologies |
Piovan |
Plama |
Plast Engineering Knauff |
Plastic Metal S.p.A. |
Plastipak |
Profile Solutions |
PROMEC |
Promix Solutions |
PTI Plastic Technologies, Inc. |
Reiken (Osaka Reiken Co. Ltd.) |
Resilux |
R&D/Leverage |
Robinson plc |
Röders |
ROUXEL MOLD |
RPC Group |
Sacmi |
Saniton Plastic |
Samkin |
Schoettli AG |
Serac |
Seitz Valve |
Shyam Plastic Machinery |
Siad |
Siapi |
Sidel |
Simex |
Sipa |
Shangair |
SMF Maschinenfabrik GmbH |
SMI |
Solent Mould Tools |
Somex |
SPPC - Saudi Printing and Packaging Co. |
StackTeck |
Steidle |
STM |
Teamplast |
Tech-Long Packaging Machinery |
TechnoPet Machineries |
Terekas |
Terrachim |
TES |
Tisse Makine |
Torus |
TPS Tooling Preform Systems |
TPAC |
UAB Putoksnis |
Urola |
Vanta |
VBF |
[[Wellmei] |
Zecchetti |
Zhangjiagang Eceng Bottle Machinery Co. Ltd. |
Valspar |
Vasantha |
Vetromeccanica |
Vitalii and Son |
Wentworth |
Zhongya |
... |
Market surveys
Market survey are available for the following categories: